基于PLC與GOT的CA6140臥式車床進給系統的改造計*
2016-9-2 來源: 廣東石油化工學院機電工程學院 作者: 喬東凱 趙晶英 陳軍 廖輝
摘要:闡述了CA6140臥式車床控制的原理與存在的問題,并細述了采用可編程控制器、觸摸屏、編碼器、步進驅動器和步進電機對CA6140臥式車床的進給運動自動控制的具體方法。從而實現了該車床智能化控制的目的。實踐證明該方法經濟實效。對其他類型的機床或電氣設備的改造具有借鑒和指導意義。
關鍵詞:可編程控制器;觸摸屏;車床;編碼器;步進電機
0、引言
CA6140臥式車床進給的轉速控制是通過轉動手柄來控制.要改變刀架的移動轉速,必須在刀架停止的情況下進行.速度轉換時要轉動手柄。操作不便。有時需要頻繁地更換其主軸轉速,加快了齒輪之間的磨損。導致轉速達不到要求。此外,齒輪在工作時,出現噪聲大,啟動、傳動不平穩,換速時沖擊力大等問題。進給運動的進給量是通過手輪來控制的,會出現手輪轉動后.存在一小段距離,刀架沒有移動。導致加工出現誤差。
1、調速改造方案的確定
未改造前.進給運動的轉速是由轉動手柄在不同擋位來控制,即改變齒輪之間的嚙合。其進給量則由手輪控制。機床改造后,用步進電機代替溜板箱縱向移動的大手輪和控制中滑板橫向運動的小手輪,并通過編碼器實時反映距離,采用觸摸屏和PLC技術控制進給運動的進給量和進給速度。
(1)調速原理
步進電機的轉速
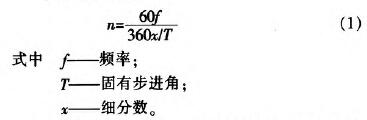
由式(1)可知,改變步進電機的頻率就可以調節進給速度,并且其頻率可在一定范圍內變化。所以轉速調節范圍寬。
步進電機的轉動圈數

由式(2)可知,改變步進電機的脈沖數可以改變步進電機轉動的圈數。進而改變移動的距離。
(2)PLC、步進電機、步進驅動器、觸摸屏和編碼器的選擇
根據實際情況,系統需要控制2個步進電機,即PLC需要2個高速脈沖輸出.為方便操作和保證系統的可見性。系統配備有觸摸屏.故所需PLC的點數較少,且要連接編碼器,需要晶體管輸出,最終選擇型號為FX3U一32MT的三菱PLC。由于代替手輪和手柄轉動的步進電機不需要太大力矩.選擇步進電機57BYG250B—SAFRMC-0152.其保持轉矩為0.7 Nm,步距角是1.80,相數為2相。相應地選擇步進驅動器為SH一20402A。編碼器選擇型號為E682一CWZ5B.觸摸屏選擇性價比較高的型號為M儒104X的威綸觸摸屏。
(3)PLC輸入、輸出點的連接PLC輸入點、輸出點的連接如表l、表2所示。
表1 PLC輸入點的連接
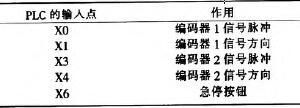
編碼器1(與大手輪連接)的脈沖與方向端分別與X0、X1連接:編碼器2(與小手輪連接)的脈沖與方向端分別與X3、X4連接:將一個急停按鈕與X6連接.用來緊急停止整個系統。
表2 PIC輸出點的連接
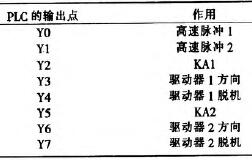
輸出點YO用于給控制床鞍和溜板箱縱向移動大手輪的步進電機驅動器1發送高速脈沖:輸出點Y1用于給控制中滑板橫向運動手柄的步進電機驅動器2發送高速脈沖。連接到Y2、Y5的中間繼電器分別控制步進驅動器l和2的通電與斷電。輸出點Y3、Y6分別給步進驅動器1和2發送方向信號,控制步進電機l和2正轉。輸出點Y4、Y7則是使步進驅動器1和2脫機。
(4)PLC與步進驅動器、步進電機的連接PLC與步進驅動器、步進電機的連接如圖1和圖2所示。
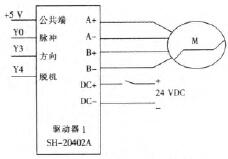
圖1 步進驅動器1的接法
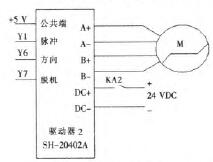
圖2步進驅動器2的接法
(5)PLC與觸摸屏的通訊PLC與觸摸屏的通訊如表3所示.PLC與觸摸屏接13類型為RS-485 4W,通訊端口為COMl,通訊線:觸摸屏(公頭)1、2、3、4,5對應PLC(公頭)4、7、1、2、3。
表3 PIG與艟摸屏的通訊
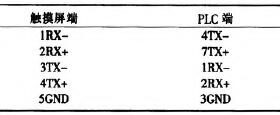
(6)主軸速度和進給運動的控制
步進電機通過步進驅動器來控制.即PLC通過步進驅動器來控制步進電機。具體方法是PLC給步進驅動器輸出一個高速脈沖、方向和脫機信號。因為系統采用的是64細分.所以要將步進驅動器的刻度盤調到64細分。編碼器則連接到PLC的輸入點,利用高速計數器記錄下脈沖數.進而通過程序處理。反映出實時距離。
PLC開機初始化的程序如圖3所示。
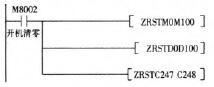
圖3 PLC開機初始化
當給PLC上電時,M8002接通一個掃描周期,系統對MO—M100,DO—D100,C247一C248進行清零。高速計數器計數并轉換為距離和清零操作程序如圖4所示。
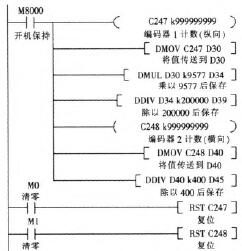
圖4高速計數囂計數并轉換為距離和清零操作
與縱向軸相連接的編碼器是通過式(1)進行距離轉換.編碼器的軸與齒數為120及模數為0.25的齒輪相聯。因此,可以求出齒輪的直徑
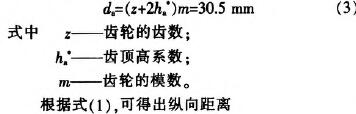
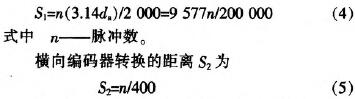
如圖4所示.當PLC開機后。編碼器轉換程序一直在執行,反映出進給移動的實時距離。編碼器輸出的脈沖用高速計數器計數。縱向編碼器的脈沖由高速計數器C247計數.然后保存在寄存器D30中,之后乘以9 577。結果保存在D35中。最后除以200 000。結果保存在D39中。橫向編碼器的脈沖由高速計數器C248計數。然后保存在D40中,再除以400。把運算結果保存在D45中。對高速計數器C247、C248的清零.則是在手動對完縱向和橫向刀后進行,確定零點位置。
主軸轉速和方向控制程序如圖5所示。
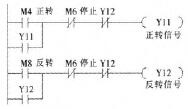
圖5主軸轉速和方向控制
當M4接通時,控制主軸正轉;當M8接通時,控制主軸反轉:當M6接通時,停止主軸轉動。同時正轉和反轉設計了互鎖。即正、反轉之間的切換,必須要停止主軸。從而保護了主軸電動機。
縱向進給速度、進給量和方向控制如圖6所示。
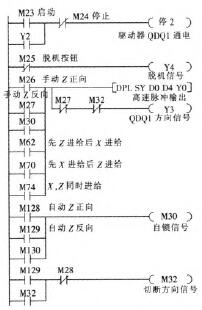
圖6縱向進給速度、進給量和方向控制
當線圈M23接通時。線圈Y2通電,給步進驅動器l上電;當線圈M24接通時,則步進驅動器1斷電。當M25接通時,線圈Y4通電,給步進驅動器1發送脫機信號。M26和M27是手動分別控制步進電機的正反轉.即前進或后退。當M28接通時,自動控制步進電機正轉:當M29接通時,自動控制步進電機反轉。當M27或M29接通時,切斷步進驅動器方向信號Y3,進而控制步進電機反轉。當M28或M29接通時.M30自鎖.給步進驅動器輸出脈沖。其中DO和D4的值可以根據需要進行改變.分別改變進給縱向的進給速度和進給量。
橫向進給速度、進給量和方向控制的程序如圖7所示。
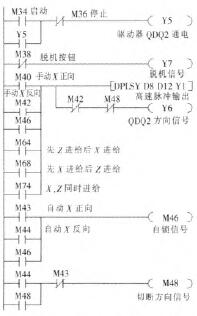
圖7橫向進給速度、進給量和方向控制
當線圈M34接通時,給步進驅動器上電:當線圈M36接通時,則斷電。當M38接通時.給步進驅動器2發送脫機信號Y7。M40和M42是手動分別控制步進電機的正反轉,即前進或后退。當M43接通時,自動控制步進電機正轉;當M44接通時,自動控制步進電機反轉。當M42和M44接通時.切斷步進驅動器方向信號Y6.進而控制步進電機反轉。當M43和M44接通時,M46自鎖.給步進驅動器輸出脈沖。其中D8和D12的值可以根據需要進行改變.分別改變進給橫向運動的轉動速度和進給量。
進給運動的速度和進給量轉換如圖8所示。
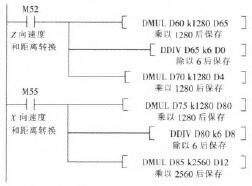
圖8進給運動的速度和進給量轉換
當M52接通時,將速度值D60根據式(1)轉換為頻率保存在D0中;將進給量D70根據式(2)轉換為轉動的圈數后.再轉變為脈沖數保存在D4。當M54接通時,將速度值D75根據式(1)轉換為頻率保存在D8中;將進給量D85根據式(2)轉換為轉動的圈數后.再轉變為脈沖數保存在D12。
進給運動的橫向與縱向運動的控制如圖9所示。
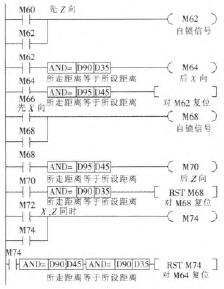
圖9進給運動的橫向與縱向運動控制
當M60接通時。M62自鎖。開始橫向運動;當所走距離值D35與所設距離值D90相等時.M64接通,開始縱向運動:當所走距離值D45與所設距離值D95相等時,復位M62,即停止運動。當M66接通時,M68自鎖,開始縱向運動;當所走距離值D45與所設距離值D95相等時.M70接通.開始橫向運動。當所走距離值D35與所設距離值D90相等時.復位M68,即停止運動。當M72接通時,M74自鎖,橫向和縱向運動同時進行.當所走距離值與所設距離值相等時,復位M74。即停止運動。
2、結語
本設計從電氣控制方案、元器件選型及機加工系統現場環境等因素綜合考慮.對CA6140車床的進給運動進行了電氣化改造.改造后的該設備控制電路簡單,穩定性和可靠性也增強。操作方便,實現了進給系統的自動化控制。進而提高了加工精度。
參考文獻:
[1]蔡厚道.渦旋式壓縮機動渦盤銑削加工宏程序的開發[J].煤礦機械,2015,36(7):282—284.
[2]王繼群.基于改進的遺傳算法及其在機床主軸箱加工路線優化應用[J].煤礦機械,2014,35(1 1):246-248.
[3]趙國勇,鄭光明,劉晨希.基于四次多項式的數控加工運動處理算法研究[J].組合機床與自動化加工技術。2014(2):13—15.
[4]喬東凱,黃崇林.PLC在C650臥式車床電氣控制線路改造中應用[J].裝備制造技術,2008(1):62—63.
[5]劉濤,陳明.基于人機工程學的數控機床設計與分析[J].組合機床與自動化加工技術.2014(1 1):49—52.
[6]張彥民.CA6140型普通車床的數控化改造研究[J].煤礦機械,2013,34(5):213—215.
投稿箱:
如果您有機床行業、企業相關新聞稿件發表,或進行資訊合作,歡迎聯系本網編輯部, 郵箱:skjcsc@vip.sina.com
如果您有機床行業、企業相關新聞稿件發表,或進行資訊合作,歡迎聯系本網編輯部, 郵箱:skjcsc@vip.sina.com