9600k W構架整體加工常見問題與改進
2018-8-7 來源:中車株洲電力機車有限公司 作者:劉榮
【摘要】本文主要介紹9600k W轉向架構架整體加工中,存在的一些常見而且具有代表性的問題,對其進行數據分析和探討,通過改進加工刀具,選擇合理的加工工藝路線,在實踐中針對不同的材質選擇合適的切削參數,優化加工程序等一些過程,從而使問題得以有效地解決,更好的達到工藝技術要求,提高加工質量,提高生產效率。問題具有典型的代表性,在以后的構架加工中都可以效仿和借鑒。
關鍵詞:構架加工;刀具;參數分析
1. 概述
最近的幾年中,轉向架事業部已先后引進了多臺大型數控龍門鏜銑床,用于城軌地鐵以及機車轉向架的構架加工。大型龍門數控鏜銑床,絕大部分已經滿足了構架加工的工藝要求,同時也保證了構架的質量。然而,有些工序的加工中,并不是單靠機床就能保證其質量。往往還需要刀具,以及參數設定、加工工藝、程序等一起保證產品質量。本文將對一些構架加工中遇到的問題,通過自己的理論和實踐經驗,探討一些可行的加工方法。在保證產品質量的同時,更好地提高生產效率。
2. 拐角加工分析
如在9600k W六軸車、神八、DJ4整體構架加工中,在加工吊桿座內框、拉桿座U型槽以及拉桿座內腔的時候,加工效率低,刀具損壞現象嚴重。因為加工中不可避免地會遇到拐角區域的加工,如果在拐角處采用直線軌跡時,由于刀具加工到圓弧拐角處時,刀具與工件切入角增大,銑刀的切削弧長發生了突變,而每齒平均銑削力與切削弧長相關,因此,平均銑削力在拐角處也發生了突變。使刀具的負荷猛然增加,超過了刀具的承受強度,造成立銑刀頻繁折斷。造成立銑刀折斷的主要原因是拐角加工時的負荷急劇增加。如果拐角的加工余量僅僅只有不足1m m,或者更小。當在遇到拐角的時候,立銑刀所受的負荷就會大大減小。那么,在拉桿座等拐角的時候,最主要的是先對其拐角處的余量先進行加工。如圖1、圖2所示的對比。先在圓弧拐角處采用φ32mm鉆銑刀(見圖3)將圓弧插銑到尺寸。鉆銑加工過程中刀具沿主軸方向做進給運動,利用底部的切削刃進行鉆、銑組合切削,對拐角加工具有重要意義,從根本上解決拐角加工難題。再利用強度高的φ32mm整體硬質合金立銑刀(見圖4)進行剩余部分的直線銑削來完成吊桿座內框、拉桿座U型槽以及拉桿座內腔的最后成形銑削。
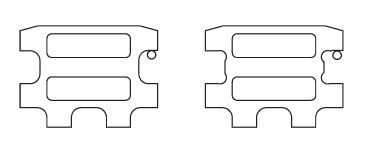
圖1不進行拐角余量處理 圖2進行拐角余量處理
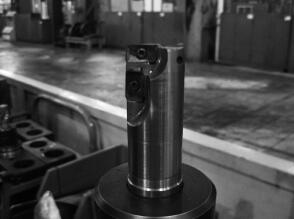
圖3 φ32mm鉆銑刀
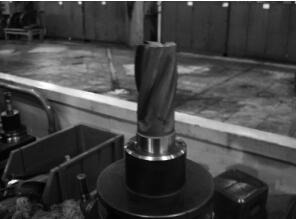
圖4 φ 32mm整體硬質合金立銑刀
3. 解決制動器吊座孔φ 28mm鏜孔精度
因為制動器φ28mm吊座孔剛性較差,粗精加工中,易產生震顫,表面質量以及尺寸精度達不到要求。重要的是φ28mm的孔是銷套配合,如果尺寸精度超差甚至會造成銷套的位移甚至脫落,嚴重影響了構架加工質量,加工后經常出現制動器吊座孔的返工現象。制動器吊座結構如圖5所示,制動器吊座板只有12mm厚,外表面沒有加工而且又是懸臂結構,原加工方法采用一鉆一鉸,用φ27mm普通麻花鉆頭鉆孔時軸向抗力易使制動器吊座板后倒、徑向抗力使支座左右擺動造成橢圓孔,精加工鉸孔時難以消除鉆孔造成的復映誤差達不到圖樣要求的φ28mm H7的精度。綜合上述分析,解決制動器吊座在加工中的剛不足及消除其造成的影響是提高質量解決問題的關鍵所在。改進措施如下:
(1)增加工藝支撐我們通過設計夾緊點和支承均可移動便于構架裝夾的支撐桿(見圖6),I為鋼管制作的撐桿,兩頭有內螺紋的端頭,2為撐桿的頂緊螺釘,3為焊接在撐桿上的夾板,4為夾板上的夾緊螺釘,5是構架側梁,6是制動器吊座。使用時先對好位置,預緊撐桿螺釘2,再用手動均勻擰緊左右夾緊螺釘4,頂在支承板或制動器吊座6上均可,最后把各螺釘擰緊。這樣就解決了吊座在加工時左右擺動剛性不足的問題。
(2)改進刀具 首先,φ27mm開分屑槽(見圖7),麻花鉆改用φ27mm群鉆(見圖8)。使用φ 27m m群鉆以減小鉆削產生的軸向抗力。群鉆是通過長期的實踐和研究,針對標準麻花鉆各角度在切削時暴露的弱點采取不同措施,對標準麻花鉆進行刃磨時各角度大改進的一種鉆頭,實踐說明,群鉆的出現為提高功效延長鉆頭壽命具有很大的意義。
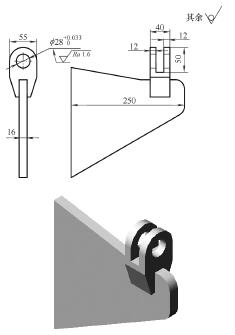
圖5 制動器吊座
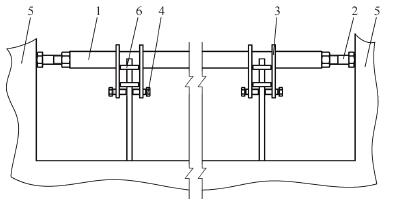
圖6 工藝支撐
1.撐桿 2.撐桿螺釘 3.夾板 4.夾緊螺釘 5.構架側梁 6.制動器吊座
群鉆與麻花鉆比較有下列優點:①切削輕快,省力。因前角增大,橫刃經修磨后窄又尖。軸向抗力下降35%~50%,扭矩下降10%~30%。②可以加大進給量,使生產率提高3~5倍。③使用壽命高。因為群鉆刃形比較合理,分屑好,排屑順利,散熱條件好。④定心作用好,孔的精度高。因為群鉆磨出對稱的月牙槽,在切削時受力分布合理,因此孔不易鉆偏。
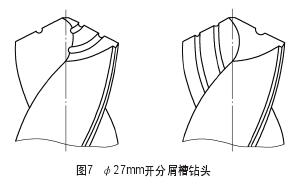
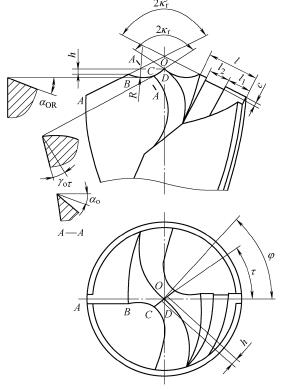
圖8 φ27mm群鉆
其次,φ28mm鉸刀(見圖9)改用減振性能好的精鏜刀,精鏜頭型號為R825A-AF11STUP06T1A刀柄型號C3-390.58-50 070,這樣精鏜孔時可以消除鉆孔留下的橢圓度以及保證前后孔的同軸度(見圖10)。
4. 電動機懸掛座圓弧槽刀具的改進
電動機懸掛座φ20mm半圓槽的中心與梁體的距離只有57mm,機床直角附件頭根本無法靠近電動機懸掛座,所以也就不能從電動機懸掛座的側面加工φ20mm的半圓槽。鑒于這種情況,我們設計了一把φ20mm專用的非標的硬質合金焊接球頭銑刀,從電動機懸掛座的正面進行加工φ20mm的半圓槽。在φ 20mm專用的硬質合金焊接球頭銑刀(見圖11)的使用過程中,由于硬質合金焊接刀是采用標準的φ20mm硬質合金刀片進行焊接的,硬質合金焊接刀具刀片與刀體焊接后位置精度較低,必須要進行刃磨,這樣加工的半圓槽就無法保證圖樣尺寸φ20+0.33 0mm。
如果刀具磨損后再進行刃磨,刀片的直徑尺寸就更小了。工藝上需要采用軸向、徑向多次進給以彌補刀具的磨損,這樣加工效率低,又由于焊接刀具刀頸最小處才φ20mm,刀頸容易折斷,刀具損壞現象較多,平均每把只能加工12個構架。加工后的產品質量也不穩定,經常出現轉向架總成在安裝電動機時發現防落塊銷子穿不進去的現象發生。針對以上的問題我們聯合有關刀具專家設計了一把機夾式可轉位D56R10銑刀(見圖12)來加工。其原理采用標準的φ20mm硬質合金可轉位圓形刀片,兩片圓形刀片在刀體軸向錯位的形式來保證加工后的半圓槽尺寸φ20+0.33 0m m。刀片磨損后可以轉位,這樣就可以完全保證產品的加工質量。關于圓形刀片在刀體軸向錯位的尺寸從0.005~0.25mm之間在瑞典
SECO公司的中國實驗室反復試驗,最后確定錯位的尺寸0.2mm為最佳狀態。

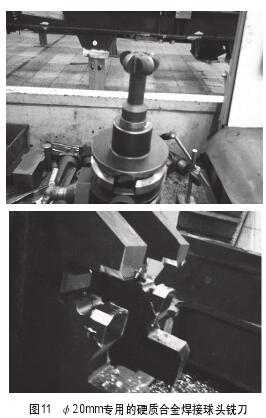
同時通過工藝的優化,切削參數選用轉速為682rpn/min,進給量310mm/min。一次切削加工效率提高2.3倍。因為使用標準刀片每片20元,每片而且可以轉位使用,大大降低了成本。刀桿φ32 m m,刀具剛性大幅提高,避免了加工時所產生的振動,提高了加工質量。所產生的經濟效益有:購買一把刀D47.2R10焊接刀要358元,可加工12個構架,而改善后用的可轉位D56R10銑刀,一片可轉位硬質合金刀片僅需20元,每把需2片刀片,可加工至少60個構架,1臺車可節約刀具費為58.34元。
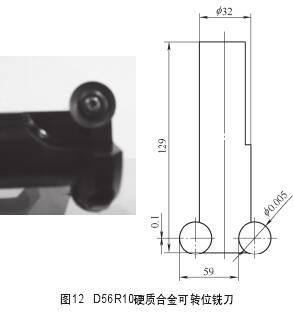
5. 結語
通過對以上三條工藝改善方案的實施 ,9600k W型機車構架加工時間得到進一步的縮短,再加上一線生產員工同工藝人員共同配合對切削參數的優化,最終將加工時間縮短至目前的9h。僅僅是鉆銑刀具一項改善,每年就可為公司節約刀具成本近9萬元。然而在改進的過程中我們并非一帆風順,也曾有過試加工失敗的經歷,例如到目前為止φ25mm的鉆銑刀加工情況還不是特別理想。在調查7米龍門銑床在加工六軸車構架側梁時粗加工拉桿座內框的可能性,確定此方案的可行性后,我們完善了7m龍門銑床加工六軸車構架拉桿座內框的刀具和工藝文件,條條大路通羅馬,采用工藝分流的辦法同樣減少了構架生產時間,縮短產品加工周期;在改善的過程中,我們成功改造了標準鉆銑刀具,為以后將標準刀具改造為非標刀具來提高生產效率積累了豐富的經驗。工藝改進不是憑空想象,通過各部門之間的相互合作,學習相關理論知識,運用并行工藝、科學的統籌方法,開放的、創造性思維是我們取得成功的關鍵所在。
投稿箱:
如果您有機床行業、企業相關新聞稿件發表,或進行資訊合作,歡迎聯系本網編輯部, 郵箱:skjcsc@vip.sina.com
如果您有機床行業、企業相關新聞稿件發表,或進行資訊合作,歡迎聯系本網編輯部, 郵箱:skjcsc@vip.sina.com