高溫合金的加工 - 進給率堪比鋁合金
2019-1-11 來源:瓦爾特 作者:-
航空工業(yè)的大量訂單給發(fā)動機制造商及其供應(yīng)商的能力帶來了巨大壓力。因此,減少零件加工時間將受益匪淺。對于高溫合金,硬質(zhì)合金銑刀的切削速度約為50米/分。陶瓷銑刀提供了一種不同的方法:其切削速度可達1,000米/分。
瓦爾特的產(chǎn)品包括兩個系列的陶瓷銑刀:具有通用槽形的MC275適用于大多數(shù)應(yīng)用場合; MC075為高進給銑刀。兩種產(chǎn)品系列(見圖1)均可提供8~25毫米的切削直徑。直徑為8~12毫米的刀具可作為整體銑刀使用,而直徑為12~25毫米的刀具可作為ConeFit銑刀使用。在這兩種情況下,只有刀具的頭部由陶瓷制成。該刀頭釬焊在硬質(zhì)合金接柄或碳化物ConeFit基體上。原則上,整個銑刀可以由陶瓷制成,但是硬質(zhì)合金接柄增加了刀具的強度和阻尼。與整體式陶瓷刀具相比,其懸伸長度更長,材料去除率更高。
圖1:陶瓷銑刀和ConeFit陶瓷銑刀
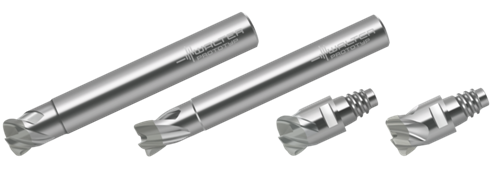
圖文說明:具有通用槽形的MC275陶瓷銑刀和具有高進給槽形的MC075陶瓷銑刀作為立銑刀和標準系列的ConeFit解決方案。圖片:瓦爾特
陶瓷切削刀具材料的應(yīng)用范圍包括ISO S組中的鎳基、鈷基和鐵基耐熱合金。例如典型的合金有Inconel 718、René® 80、Nimonic® 80A、 Haynes® 556®、Mar-M-247®和Stellite® 31。這些高溫合金(HRSA)是飛機發(fā)動機高溫部分的首選。
陶瓷切削刀具材料可定制用于銑削應(yīng)用。與晶須增強陶瓷相比,SiAlON陶瓷更耐溫度波動。正因如此,它們成為銑削加工工序的理想選擇。斷續(xù)切削導(dǎo)致切削刃上的溫度變化,并且冷卻介質(zhì)的使用可以進一步增加溫差,從而產(chǎn)生熱沖擊效應(yīng)。因此,瓦爾特建議在使用陶瓷銑刀加工高溫超合金時,采用干式加工。用戶得到的另一個好處是,由于不適用冷卻潤滑劑,加工作業(yè)環(huán)保,經(jīng)濟實惠。
使用陶瓷刀具銑削鎳基合金時磨損的主要原因是由溫度和積屑瘤引起的化學(xué)磨損。雖然化學(xué)磨損或擴散磨損持續(xù)削弱切削刀具材料,但是由于在切削刃上堆積而引起的磨損是不可預(yù)測的,并且會出現(xiàn)突然增加。由于加工溫度高(見圖2),以及高溫超合金的韌性高,即使在高溫下(例如Inconel®718;750℃時Rm = 880 N/mm²,),刀具上會有大量積屑。這些積屑可熔化到切削材料的表面上,并且在移除時,使陶瓷部分被削掉。刀具上的積屑瘤詳見圖3。即使加工HRSA所產(chǎn)生的高溫對刀具壽命有負面影響,但這是必需的。這是降低材料硬度并提高加工效率的唯一方法。
圖2:Inconel® 718 – 用MC275銑槽
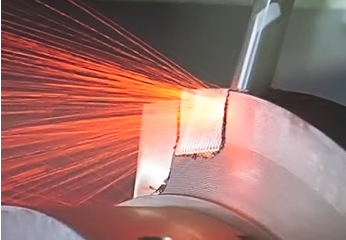
圖文說明:MC275陶瓷銑刀,用于Inconel®718的槽銑,切削速度為670米/分。生產(chǎn)效率和金屬去除總量明顯高于硬質(zhì)合金銑刀。圖片:瓦爾特
圖3:MC075的磨損模式(vc = 600 m/min;ap = 0.4 mm;fz = 0.15 mm;Inconel® 718)
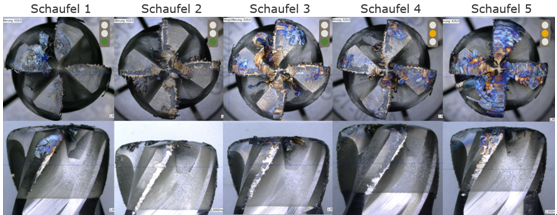
圖文說明:盡管積屑瘤和切屑量較大,但陶瓷銑刀在加工五張葉片后,仍然可以使用。粘附在刀具上切屑變色表明加工溫度很高。 圖片:瓦爾特
切削參數(shù)由切削刀具材料和需要加工的材料確定。脆而耐熱的切削刀具材料可在高溫下使用,但是低沖擊強度要求0.02~0.05毫米的每齒低進給率,全開槽工序ap = 5%Dc的小吃刀量和最大切削刃長度的輪廓銑削的ae = 5%Dc。其例外情況是,具有高進給槽形的MC075,其中ap≤apf時,fz = 0.15毫米。兩種產(chǎn)品的切削速度均在400~1000米/分。
具有硬質(zhì)合金切削刃的銑刀與具有陶瓷切削刃的銑刀的結(jié)果不可能相差很大。圖3所示的磨損照片顯示了陶瓷銑刀僅用于粗加工的原因。磨損跡象(例如切削刃上的切屑和寬度超過0.5毫米的磨損痕跡)只是表明硬質(zhì)合金銑刀的使用壽命快要結(jié)束,并不是停止使用陶瓷切削刀具的理由。通過對切削參數(shù)進行比較,也可清楚地看出兩類刀具材料之間的差異。例如,對Inconel®718全開槽所用的直徑為10毫米的立銑刀進行比較(見圖7中的表格):盡管使用碳化物的切削深度較大,但是使用陶瓷的進給率大得多,這種優(yōu)勢是無可比擬的。在這種情況下,使用陶瓷切削刃的金屬去除率在56%以上。此外,使用陶瓷銑刀去除的金屬總量比硬質(zhì)合金銑刀高180%。就金屬去除率和每個刀具壽命中去除的金屬總量參數(shù)而言,陶瓷比碳化物具有明顯優(yōu)勢。使用相同的機床,加工時間更短,加工批量更大;用戶可以選擇配置其現(xiàn)有機床,從而可使用更少的加工中心。總加工量大,刀具成本低。
圖6:Inconel® 718的硬度曲線
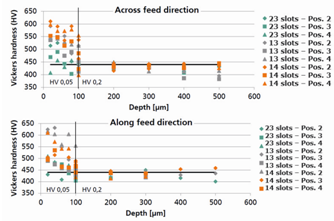
圖文說明:圖中顯示了材料在100微米深度下的硬化。無論刀具磨損或測量位置如何,在200微米或更深的深度都不會測量到硬化。 圖片:Fraunhofer IPT
圖7:硬質(zhì)合金與陶瓷的比較
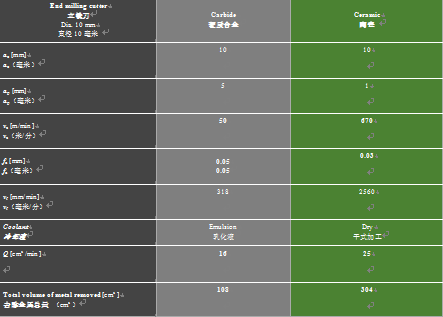
圖文說明:比較結(jié)果表明,與硬質(zhì)合金銑刀相比,采用陶瓷銑刀切削速度高很多,金屬去除率更高,金屬去除總量更多。 圖片:瓦爾特
鎳基合金部件加工的經(jīng)典案例是飛機發(fā)動機的整體式渦輪葉盤。此旋轉(zhuǎn)整體部件是一個具有大量葉片的盤。使用硬質(zhì)合金銑刀,通過粗加工,可銑出葉片之間的空間。加工時間約30分鐘。具有高進給槽形的MC075陶瓷銑刀可在10分鐘內(nèi)切出相同的空間。對于這種應(yīng)用,它在硬度為44HRC、抗拉強度為1400 N/mm2的耐熱鎳基合金中實現(xiàn)了9500 mm/min的進給率。這些進給速率值通常用于加工鋁,而不是鎳基合金。
圖4:槽內(nèi)測量點的位置
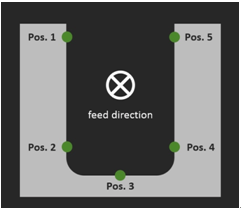
圖文說明:因為槽基體的溫度升高,關(guān)鍵測量點是位置2和位置4。 圖片:瓦爾特
圖5:測量點的分布
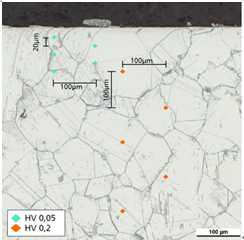
圖文說明:顯微照片顯示了硬度測量的測量點的分布。不允許有超出精加工余量的任何硬化。 圖片:Fraunhofer IPT
雖然陶瓷刀具提供了極好的加工機會,但是值得考慮的是,陶瓷銑刀達到的高加工溫度是否會導(dǎo)致材料的損壞。由于陶瓷刀具僅用于粗加工,所以唯一需要保證的是,材料損壞的深度小于精加工的偏差。與位于德國亞琛的Fraunhofer IPT公司通力合作,我們測量了硬化的深度和范圍 - 針對具有不同磨損水平的陶瓷銑刀,Inconel®718的全開槽工序。在陶瓷刀具銑削具有中等磨損的13或14個槽或磨損嚴重的23個槽后,我們分別對其進行了硬度測量。為了確定并評估最大熱負荷,槽上選擇的測量點如下文所示(見圖4)。為確保收集的數(shù)據(jù)正確,我們進行了如圖5所示的測量。材料的基本硬度為446HV。結(jié)果:在100微米的深度內(nèi)檢測到高達640 Hv的硬化。無論刀具的磨損或測量方向如何,如果深度大于200微米,都檢測不到硬化。由于通常適用的粗加工偏移量在3/10~5/10,所以不希望使用陶瓷工具進行的粗加工在精加工過程后,會導(dǎo)致任何其它損壞。
陶瓷銑刀是高效可靠加工高溫合金的理想選擇。
可視化視頻:https://youtu.be/4UC3jCdhi_M
圖8:Stefan Benkóczy
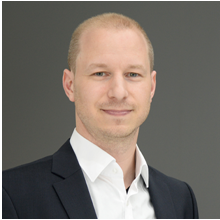
圖文說明:瓦爾特航空工業(yè)零件經(jīng)理Stefan Benkóczy 圖片:瓦爾特
投稿箱:
如果您有機床行業(yè)、企業(yè)相關(guān)新聞稿件發(fā)表,或進行資訊合作,歡迎聯(lián)系本網(wǎng)編輯部, 郵箱:skjcsc@vip.sina.com
如果您有機床行業(yè)、企業(yè)相關(guān)新聞稿件發(fā)表,或進行資訊合作,歡迎聯(lián)系本網(wǎng)編輯部, 郵箱:skjcsc@vip.sina.com
更多相關(guān)信息
業(yè)界視點
| 更多
行業(yè)數(shù)據(jù)
| 更多
- 2025年5月 新能源汽車銷量情況
- 2025年5月 新能源汽車產(chǎn)量數(shù)據(jù)
- 2025年5月 基本型乘用車(轎車)產(chǎn)量數(shù)據(jù)
- 2025年5月 軸承出口情況
- 2025年5月 分地區(qū)金屬切削機床產(chǎn)量數(shù)據(jù)
- 2025年5月 金屬切削機床產(chǎn)量數(shù)據(jù)
- 2025年4月 新能源汽車銷量情況
- 2025年4月 新能源汽車產(chǎn)量數(shù)據(jù)
- 2025年4月 基本型乘用車(轎車)產(chǎn)量數(shù)據(jù)
- 2025年4月 軸承出口情況
- 2025年4月 分地區(qū)金屬切削機床產(chǎn)量數(shù)據(jù)
- 2025年4月 金屬切削機床產(chǎn)量數(shù)據(jù)
- 2025年1月 新能源汽車銷量情況