剮齒加工技術與刀具設計
2019-5-5 來源:湖南中大創遠數控裝備有限公司, 作者:李錫晗
摘要:面對國內汽車市場的快速發展,以及機械行業對齒輪加工制造技術提升的需求,原有的齒輪加工技術已不能滿足當前的要求,文中介紹了一種新的圓柱齒輪加工工藝方法———剮齒加工,分析介紹了剮齒加工中存在的問題,提出了刮齒加工中存在問題的解決方案,以及在這種方案下的刀具參數的修正方法,經過實際驗證,在加工效率、產品精度、節能與環保等方面取得了良好的效果,尤其在內齒的加工上,展現出了更大的優勢,并提供了加工實例以供參考。
關鍵詞:圓柱齒輪;剮齒;刀具;刀具前角
隨著我國制造技術需求的快速提升, 制造業各項技術均得到了迅猛的發展,齒輪加工制造技術向著高精度、高效率、高可靠性、低能耗、綠色環保的方向快速發展,同時,由于國內工程機械、交通運輸業的快速發展,數控技術廣泛應用于齒輪制造,極大推動了齒輪技術的進步。隨著國內汽車業的發展,我國已在短短幾年成為全球第一生產大國,飛速發展的汽車業帶動了相關產業的提升,而圓柱齒輪加工一直被滾齒、插齒、銑齒、滾軋、剃齒、磨齒等傳統的加工方法所主導,陳舊的加工方式已不能滿足發展的需要, 廣泛應用的乘用車 AT 變速器行星輪減速機構的齒圈和行星輪, 由于加工技術上的不足而難于保證產品技術目標的達成,巨大的市場需求卻全面依靠進口。 德國 WERA 公司推出的 SCUDDING 技術成功在該行業展示出強大的技術優勢,而正因其技術具有非常顯著的優勢, 其對該項技術包括加工工藝、裝備、刀具等進行了全面的技術封鎖,近年來國際上的齒輪加工裝備制造商 (如美國格里森) 也加入該技術研究開發的行列,為此,我們對該種加工技術進行了深入的研究與試驗、驗證,并取得了較為理想的效果。
1、 全新的圓柱齒輪加工原理
該種加工方法命名為“剮齒加工方式”。 剮齒加工仍基于齒輪加工技術中成熟的展成加工技術理論基礎, 即采用齒形刀具,在刀具與產品之間模擬一對齒輪嚙合運動過程,同時,增加刀具相對于產品的連續的軸向相對運動和斷續的徑向相對運動,以實現刀具的進給運動,來實現齒輪產品的加工。 其加工裝備如圖 1所示。
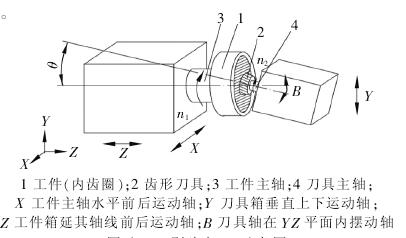
圖 1 剮齒加工示意圖
工件與刀具同時旋轉,工件隨其主軸的轉速 n1, 角速度 ω1運轉,刀具隨其主軸的轉速 n2,角速度 ω2運轉,刀具與被加工產品形成一對相互嚙合的齒輪。同時,為在這一狀態下實現嚙合點的齒向方向的位移,保證產品剮削加工的順暢,使工件主軸的軸線與刀具主軸的軸線相對傾斜,即模擬交錯軸齒輪嚙合狀態(圖2), 形成的軸交角設為 θ, 一般情況下根據產被加工產品的材質、規格、刀具材料、工藝等條件選擇軸交角,推薦軸交角的范圍為 5°~35°,確定 θ 后,即可確定刀具的螺旋角:
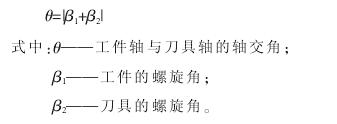
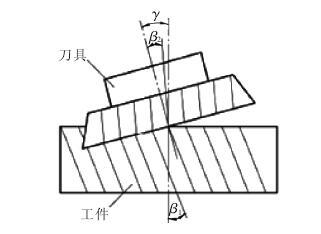
圖 2 交錯軸剮齒加工示意圖
根據刀具加工點的切削線速度來確定刀具軸的轉速, 而后可由工件與刀具的齒數計算得出符合齒輪嚙合傳動的工件軸轉速;在這 2 個轉速確定后,需對工件軸的轉速進行修正,該修正量是由于 Z軸的軸向進給和被加工齒輪的螺旋角 β1而附加到模擬嚙合傳動中的,即用 Z 軸軸向進給速度和產品螺旋角 β1等參數進行計算修正, 以保持在加工過程中的每一時刻刀具與產品之間正確的嚙合關系。
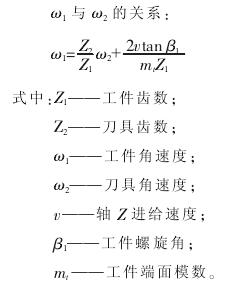
加工過程中齒深的進給運動, 由刀具與產品之間的徑向進給實現,徑向進給采用階段進給方式,由 X 軸分幾次完成齒全高的切削加工; 對于如汽車同步器中的錐形齒盤等特殊的錐形內、外齒要求,可以采取徑向連續式聯動進給來實現。刀具的刃形設計成與工件齒形共軛的形狀。加工時,刀具的刀齒從非嚙合狀態逐步進入嚙合狀態, 切削過程從即將進入嚙合狀態的刀齒的齒根部的嚙合起始點開始, 延刀齒的齒廓漸漸向齒頂方向移動, 再由齒頂推進到另一個齒廓面并逐步接近脫離嚙合的終止點;配合交錯軸傳動中的嚙合點的軸向位移、Z 軸的軸向進給即可完成指定齒深下齒槽的切削加工;而后由間斷的 X 軸徑向進給運動, 改變指定齒深重復 Z 軸的軸向進給加工,直到完成全齒深的齒槽加工,即完成了產品的加工。 切削過程的狀態如圖 3 所示。
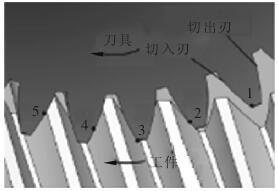
圖 3 剮削過程示意圖
2 、剮齒加工的主要問題
(1)按常規齒輪刀具的設計方式設計出來的刀具 ,在采用剮齒加工工藝方法時,在可選范圍內不論怎么改變軸交角,加工過程振動、噪聲均較大,齒面效果不好,齒面有明顯的擠壓印痕,以及由工件軸與刀具軸同步波動而產生的齒向波動誤差, 加工出的產品如圖 4 所示,產品齒面有由于擠壓而產生的凹凸現象,明顯不可接受。
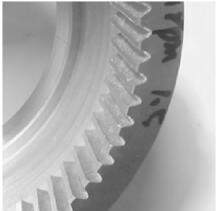
圖 4 加工完成后的產品圖
(2)加工后的刀具的齒頂及側刃有燒損(圖 5)。 剮削加工過程刀具在軸向進給方向的切入,在齒頂其前角為 γ,而在切入和切出的齒廓部分均小于 γ,越接近齒根其值越,若優化切削狀態,提升加工質量則需在刀具上進行改進設計。
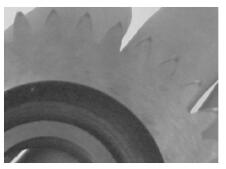
圖 5 切削加工后刀具正面圖
3 、單側刃剮齒刀的設計
運用新的加工工藝方法,其加工方法的變更,就必須配以加工工藝相關方面的變更。為解決剮齒加工中出現的問題,我們開發設計了專有的剮齒刀具,以保證加工狀態的正常。如圖 6 剮齒刀外形結構圖, 單側刃剮齒刀具設計成與產品具有共軛齒形的刀齒盤,刀具的法向模數與工件的法向模數相同,這些方面均與前述的剮齒加工方式保持一致, 特別的就是在刀齒的前刀面進行了專有的改進,設計了剮齒刀的刀齒側刃前角。
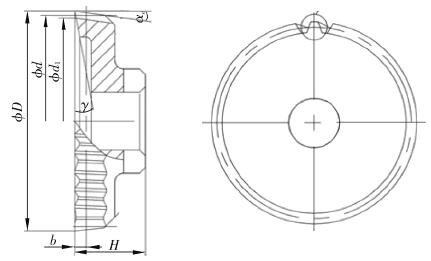
圖6 剮齒刀外形結構圖
(1)如圖 7所示,單側刃剮齒刀的每個刀齒均有與產品要求相適用的參數,如模數、壓力角、螺旋角等,同時,每個刀齒均有齒頂前角 γ,齒頂后角 αe,側刃后角 αc,分度圓螺旋角 β 等 ,單側刃剮齒刀的每個刀齒上有專門設計制造的側刃前角 γsc,其的大小范圍在 1°~15°;
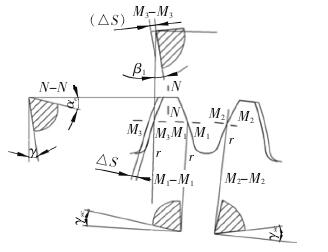
圖 7 單側刃剮齒刀主要切削角
(2)由于該側刃前角的出現 ,增大切削前角 ,大幅優化了加工狀態,但由于 γsc的出現,也會影響切削產品的壓力角,因此,要對刀具的齒形壓力角進行修正, 修正齒形角是為了在保證剮齒刀各切削角度的同時, 確保加工出的產品齒形面具有與產品要求一致的齒形角而進行的修正, 具體修正值可由下式計算得出:
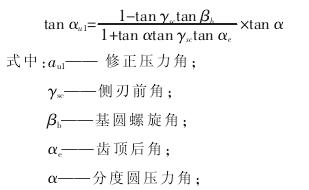
(3)由于頂刃前角的存在也同樣會影響齒形角 ,其修正值可按下式計算得出;
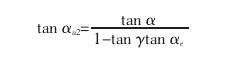
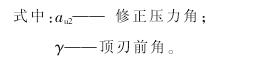
當同時存在頂刃前角和側刃前角的情況下, 修正齒形角 αu為由于頂刃前角和側刃前角引起的修正量的代數和。
(4)由于在剮齒加工過程中,刀具每一齒牙的左右面均參與加工,確定側刃前角 γsc后,由于切削前角的出現雖然可以在切入側保證理想的加工前角, 但在刀具齒牙的切出側則出現了更大的切削負前角,會嚴重影響加工狀態,而產生擠壓和振刀。 為此,在單側刃剮齒刀每個刀齒的 γsc的傾斜方向上,在相鄰的刀齒上是相對分布,并在加工的負前角一側的齒廓上進行修整,設該修整量的大小為 ΔS,刀齒漸開線上任一點 y 的修整量 ΔSy是在過 y 點的圓上的切線方向測量,ΔS 的修整面與 γsc對應分布,刀齒分度圓上的齒厚為 S:
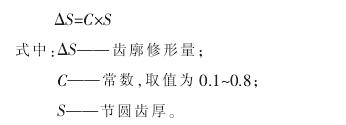
由于單側刃刀具的設計, 使得產品的加工每一個齒的兩個面是由刀具的不同刀齒的兩個齒廓刃加工出來的, 單側刃剮刀的設計要求,奇數齒的產品用偶數齒的刀具加工,偶數齒的產品用奇數齒的刀具加工。如果是奇數齒刀具,則其中一個刀齒上取削與之相對應的 γsc。
4 、剮齒加工試驗
(1) 選擇一內斜齒輪加工為具體實例, 工件參數如表 1 所示。
表 1 試加工產品參數
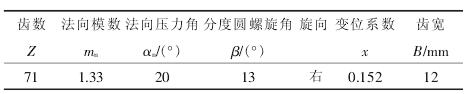
(2) 根據產品參數和結構進行刀具參數的計算與選擇 (圖8),目標產品為內斜齒 ,根據單面剮齒刀設計原則及插齒刀設計的相關原則,選用 34 齒的刀具。
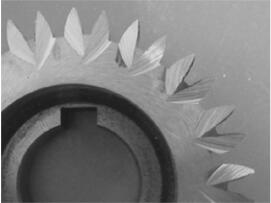
圖 8 單側刃剮齒刀
目標產品的齒向螺旋角為 13°,并且有大于 5.2 mm 的退刀空間,在滿足產品加工的前提下方便制造,刀具的螺旋角選為 0°。變位系數選為 0.2,試制產品加工刀具參數如表 2 所示。
表 2 試制產品刀具參數表
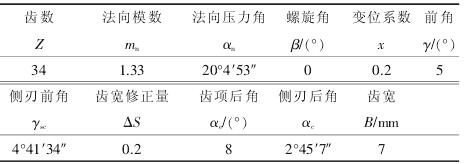
根據側刃前角計算方法,計算得出刀具刀齒側刃前角為 4°41′34″。 修正后的齒形角為 20°4′53″。 確定齒寬修正量為 0.20mm。 根據加工參數 , 確定加工過程第二行程起最大徑向進刀量 0.5 mm。 刀具精度等級:AA 級。
(3) 機床調整參數 : 軸交角為 13° ; 切削行程 (Z 軸軸向進給總行程)為 13.6 mm;工件軸轉速為 1 915.419 8 rpm;刀具軸(跟隨軸)轉速為 4 000 rpm;工件軸角度附加為 3°34′51″;Z 軸軸向進給速度為 100 mm/min; 精切工件軸轉速為 3 016.846 6 rpm;精切 刀 具 軸 轉 速 為 6 300 rpm; 精 切 軸 向 進 給 速 度 為 75 mm/min;實際切削時間為 43.52 s。
產品試加工結果如圖 9 所示, 加工的內齒輪精度達到 5 級精度,齒面效果良好,刀具加工壽命長,加工效率是目前數控插齒機的 11 倍。
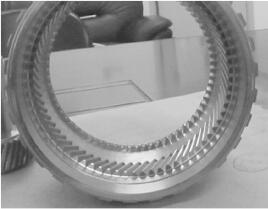
圖 9 加工后的產品圖
5 、結論
在剮齒加工過程中,由于加工參數和刀具角度的設計,很容易在產品與刀具產生嚴重的擠壓現象;運用單側刃剮齒刀具,可以改良剮齒加工的切削狀態, 具有適合于剮齒切削狀態的前角γ 和側刃前角 γsc,大幅減小了剮齒加工中的擠壓成份 ,降低了對刀具材料和機床剛性的要求,提升切削精度與效率,同時簡化了刀具的加工制造,提升了剮齒刀具壽命的同時,為剮齒刀具的刃磨提供了非常方便簡捷的方式。
投稿箱:
如果您有機床行業、企業相關新聞稿件發表,或進行資訊合作,歡迎聯系本網編輯部, 郵箱:skjcsc@vip.sina.com
如果您有機床行業、企業相關新聞稿件發表,或進行資訊合作,歡迎聯系本網編輯部, 郵箱:skjcsc@vip.sina.com
更多相關信息