機床的坐標軸剛性輔助增強技術研究
2025-6-30 來源: 通用技術集團沈陽機床有限責任公司 作者:萬鵬宇 孔令友
1.背景
當今零件結構越發復雜,零件材料應用高強度合金也越來越多,因此,現代數控機床的發展方向是高速、高精度、高承載。如果僅采用傳統的多軸聯動機床切削加工,尤其是加工應用高強度合金材料且結構復雜的大型零件,會對各軸造成較大沖擊,導致機床難以長久保證定位精度和重復定位精度,無法有效完成加工零件的精度、表面光潔度和穩定性的要求。
2. 現狀
當前對工件進行定位加工時,僅靠驅動系統和傳動機構,通常不能滿足工件所需的定位精度要求。當刀具或工件承受較大切削力時,尤其是在重切削時,會帶來驅動電機發熱量大、傳動機構受力變形和傳動剛度不足而引起刀具或工件振動等問題,嚴重影響工件的加工精度。
3. 解決方法
針對上述問題,設計了一種應用于機床的坐標軸剛性輔助增強技術,這種技術是通過在機床的各坐標軸設置專用的液壓夾緊裝置。當機床加工時,通過控制液壓夾緊裝置張開閉合動作抱緊機床移動部件,從而使機床的整體剛性增強,減少因傳動機構受力變形和傳動剛度不足而引起刀具或工件振動等問題,提升加工穩定可靠性,保證加工精度。為了進一步說明該技術的獨特性和實用性,文章列舉了將 “機床的坐標軸剛性輔助增強技術” 應用在 “一種專用深孔加工機床” 中的技術方案以及一些主要裝置,并對裝置的工作原理進行說明。
機床結構整體為落地式側掛箱結構,如圖 1所示。各軸導軌副均是硬軌配鑲條滾動體結構,立柱在床身上水平移動方向為 X 軸,機床側掛大拖板沿立柱上下運動方向為 Y 軸,側掛大拖板上安裝可調整間距的 Z1 軸小拖板、Z2 軸小拖板。其中,Z1 軸為固定軸,Z2 軸可單獨沿大拖板上下移動,為 V 軸。Z1、Z2 軸小拖板上分別安裝獨立帶驅動的主軸,Z1 和 Z2 兩個獨立的主軸沿小拖板導軌前后移動方向為 Z 軸。其中,X、Y、Z、V 軸應用夾緊裝置 A 進行鎖緊,由于 V 軸結構功能特殊原因,V 軸在應用夾緊裝置 A 的同時,增加夾緊裝置 B 進行復鎖,以達到坐標軸剛性增強的效果。
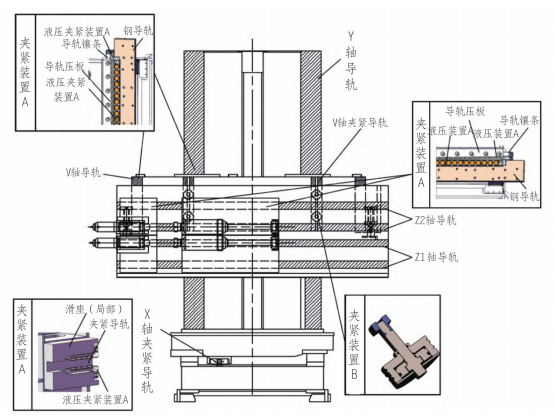
圖 1 機床整體結構示意
3.1 液壓夾緊裝置各軸運行過程
3.1.1 X 軸運行過程
當機床加工時,X 軸采用夾緊裝置 A 夾緊 X軸床身上的夾緊導軌進行夾緊,夾緊油路中選用的控制元件是 D 型電磁換向閥,這種電磁閥具有活塞位置保持功能暨電磁閥斷電時活塞保持位置不變。應用這種 D 型電磁換向閥可以保證液壓夾緊裝置 A 在機床意外斷電的時候依舊可以保持液壓夾緊狀態。通常機床工作時,液壓夾緊油路為以下 2 種狀態。
(1)壓力油經閥塊→減壓閥→電磁換向閥(電磁換向閥在常態位置為油缸進油夾緊狀態)→雙單向節流閥→雙液控向閥(液壓鎖)→壓力開關→管路→立柱下方夾緊裝置 A 進油口,推動活塞伸出實現對 X 軸夾緊導軌的夾緊功能。
(2)液壓油經夾緊裝置油口→管路→壓力開關→雙單向節流閥→電磁換向閥(電磁換向閥在工作位置為油缸排油松開狀態)→閥板排入油箱實現 X 軸松開功能。
3.1.2 Y 軸運行過程
機床 Y 軸方向同樣使用液壓夾緊裝置 A,其分別安裝在 Y 軸鋼導軌的正向和側向。由于機床 Y 軸方向為垂直于水平面,為了防止意外斷電時機床 Y 軸方向的部件砸向地面,發生安全事故,Y 軸夾緊油路應該選用帶有保壓功能的控制元件。在此夾緊油路選用的控制元件是 J 型功能電磁換向閥,這種電磁閥斷電時油路均回到中位狀態,實現保壓功能,通常機床工作時,液壓夾緊油路分以下 3 種狀態。
(1)電磁換向閥在常態位置時為油缸保壓狀態,此時油路通路為雙液控單項閥截止,油缸油液不能排出。
(2)電磁換向閥在工作位置 1 時為油缸進油夾緊狀態,壓力油經由閥塊→減壓閥→電磁換向閥→雙單向節流閥→雙液控單向閥(液壓鎖)→壓力開關→管路→ Y 軸夾緊裝置 A 油口進油夾緊 Y 軸鋼導軌,實現 Y 軸夾緊功能。
(3)電磁換向閥在工作位置 2 時為油缸排油松開狀態,液壓油經夾緊裝置油口→管路→壓力開關→雙單向節流閥→電磁換向閥→閥板排入油箱油實現 Y 軸松開功能。
保壓油路選用二位二通電磁球閥在電磁閥斷電時回到常態位,分為以下 2 種通路狀態。
(1)當夾緊油缸處于保壓位置時此時電磁球閥應在常態位置,蓄能器的油液與夾緊油缸聯通。
(2)當夾緊油缸處于工作位置 1 或者工作位置 2 是電磁球閥應在工作位置,蓄能器的油液與夾緊油缸斷開。
3.1.3 Z 軸運行過程
Z 軸采用夾緊裝置 A,對水平安裝在 Z1、Z2 軸小拖板上的鋼導軌進行夾緊,夾緊油路中的選用的控制元件是 D 型電磁換向閥。通常機床工作時,液壓夾緊油路為以下 2 種狀態。
(1)壓力油經閥塊→減壓閥→電磁換向閥(電磁換向閥在常態位置為油缸進油夾緊狀態)→雙單向節流閥→雙液控單向閥(液壓鎖)→壓力開關→管路→ Z 軸鑲條、壓板中的夾緊裝置 A 進油口,推動活塞伸出實現對 Z 軸夾緊導軌的夾緊功能。
(2)液壓油經夾緊裝置油口→管路→壓力開關→雙單向節流閥→電磁換向閥(電磁換向閥在工作位置為油缸排油松開狀態)→閥板排入油箱實現 Z 軸松開功能。
3.1.4 V1 軸運行過程
V1 軸夾緊采用的是液壓夾緊裝置 A 和液壓夾緊裝置 B 的混合夾緊裝置。夾緊油路中的選用的控制元件是 D 型電磁換向閥。機床工作時夾緊油路分為以下 2 種通路狀態。
(1)電磁換向閥在常態位置為油缸進油夾緊狀態,壓力油經閥塊→減壓閥→電磁換向閥→雙單向節流閥→壓力開關→管路→夾緊裝置油口進入夾緊油缸實現 V1 軸夾緊功能。
(2)電磁換向閥在工作位置為油缸排油松開狀態,液壓油經由夾緊裝置油口→管路→壓力開關→雙單向節流閥→電磁換向閥→閥板排入油箱實現 V1 軸松開功能。
綜上所述,在機床切削加工時可以對機床的各坐標軸進行鎖緊加固,達到坐標軸剛性增強的效果,大幅提升加工穩定可靠性,保證加工精度和光潔度。
3.2 液壓夾緊裝置結構
落地式側掛箱結構下的液壓夾緊裝置 A、B是兩種不同結構的液壓油缸(圖 1),是根據機床結構特點和功能需要特設計的專用油缸,通過靈活的擴展應用這幾種結構的液壓夾緊裝置,坐標軸剛性輔助增強技術可應用到臥式、橋式等更多結構機床中。
(1)液壓夾緊裝置 A(圖 2a),是一種直線運動快速夾緊裝置,其主要原理是通過機床直線運動液壓夾緊裝置對各移動軸進行液壓鎖緊,增加移動軸在鉆削時的剛性。這種液壓夾緊裝置直接安裝在移動部件的鑲條和壓板內,結構緊湊簡單。在結構設計上不受過多限制,具有節省空間、夾緊力大、夾緊可靠、松開方便、使用壽命長等特點。總夾緊力大小可以通過設置液壓系統壓力或增減夾緊活塞數量設定。液壓夾緊裝置 A中的夾緊活塞與活塞腔設計在運動部件導軌壓板內,液壓油通過進油口進入活塞腔,推動夾緊活塞產生微量位移,與導軌之間產生摩擦力,實現運動部件的夾緊。夾緊活塞結構是由壓塊和橡膠活塞圈組成,其中壓塊的材質選用銅合金,并采用熱處理工藝提升金屬性能,保證壓塊既耐磨又具有足夠的剛度,活塞橡膠圈的材質選用丁晴橡膠,可保證活塞腔的密封性,沒有泄漏。
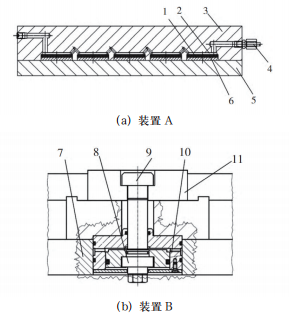
1.夾緊活塞;2. 活塞腔;3.導軌壓板;4. 進、出油口;
5. 壓塊;6. 橡膠活塞圈;7.拖板;8. 活塞;9. 壓塊;
10. 進油口;11.夾緊導軌
圖 2 夾緊裝置示意
(2)夾緊裝置 B(圖 2b)是一種單作用夾緊油缸,其主要原理是通過液壓油推動活塞,隨后活塞受力收縮,活塞帶動壓塊作用在夾緊導軌上,從而實現對 V 軸的鎖緊動作,增加 V 軸在鉆削時的剛性。當需要移動軸進行位移動作時,油缸泄壓,活塞帶動壓塊從夾緊導軌上松開。
4. 壓力計算

式中,F2 為活塞桿縮回時的理論推力,N;A2圖 3 活塞桿伸縮示意為液壓缸有桿側有效面積,m2;d 為活塞有效面積,m2。
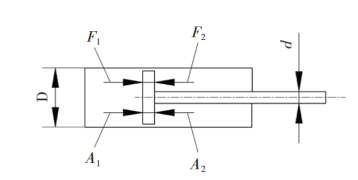
圖 3 活塞桿伸縮示意
5. 結束語
經過實驗驗證,坐標軸剛性輔助增強技術的應用,能夠分散傳動機構在加工時的受力,將力直接傳遞給機床主體,使驅動系統和傳動機構得到釋放,從而保證各軸具有較高的傳動剛性,可大幅提高機床剛性,使加工時更穩定,安全可靠,并提升切削精度,解決某些零件由于材料復雜、硬度高導致的鉆削振動問題,此技術同樣可拓展應用在類似結構機床上,也是提升類似結構機床精度和穩定性的一種重要方法,具有重要的意義。
投稿箱:
如果您有機床行業、企業相關新聞稿件發表,或進行資訊合作,歡迎聯系本網編輯部, 郵箱:skjcsc@vip.sina.com
如果您有機床行業、企業相關新聞稿件發表,或進行資訊合作,歡迎聯系本網編輯部, 郵箱:skjcsc@vip.sina.com
更多相關信息