基于六維力傳感器的工業(yè)機(jī)器人末端負(fù)載受力感知研究
2018-8-24 來源:轉(zhuǎn)載 作者: 張立建 胡瑞欽 易旺民
摘 要: 針對工業(yè)機(jī)器人末端負(fù)載與外界環(huán)境接觸力的感知需求, 在機(jī)器人法蘭與負(fù)載之間設(shè)置六維力傳感器, 并研究一套標(biāo)定與計算方法, 綜合考慮負(fù)載重力作用、傳感器零點、機(jī)器人安裝傾角等因素, 利用不少于 3 個機(jī)器人姿態(tài)下的力傳感器數(shù)據(jù), 可求得傳感器零點、機(jī)器人安裝傾角、負(fù)載重力大小、負(fù)載重心坐標(biāo)等參數(shù), 進(jìn)一步可消除傳感器零點及負(fù)載重力對受力感知的影響, 精確得到機(jī)器人末端負(fù)載所受的外部作用力與力矩. 實驗得到對于重量從 320 N 到 1 917 N 的負(fù)載, 在靜態(tài)條件下, 感知外力的誤差在負(fù)載重力的 0.28 % 以內(nèi), 感知外力矩的誤差在負(fù)載對傳感器力矩的 0.59 % 以內(nèi).
關(guān)鍵詞 : 受力感知, 重力補(bǔ)償, 零點標(biāo)定, 六維力傳感器, 工業(yè)機(jī)器人
引用格式 張立建, 胡瑞欽, 易旺民. 基于六維力傳感器的工業(yè)機(jī)器人末端負(fù)載受力感知研究. 自動化學(xué)報, 2017, 43(3):439−447
在加工、裝配等工業(yè)機(jī)器人的應(yīng)用中, 機(jī)器人末端工具或工件與外界環(huán)境的接觸力需要被精確地感知, 控制系統(tǒng)據(jù)此修正機(jī)器人的運(yùn)動, 才能保證作業(yè)的柔順性. 在醫(yī)用手術(shù)機(jī)器人的操作中, 也需要實時精確反饋手術(shù)工具與外界的接觸力, 保證手術(shù)過程的安全. 對機(jī)器人末端負(fù)載受力的精確感知是進(jìn)行機(jī)器人柔順控制與安全保障的基礎(chǔ).在現(xiàn)有應(yīng)用中, 通常在工業(yè)機(jī)器人腕部與末端負(fù)載之間安裝六維力傳感器, 用于機(jī)器人的力反饋控制[2−5]. 六維力傳感器能夠測量空間任意力系中的三維正交力 (Fx, Fy, Fz) 和三維正交力矩 (Mx,My, Mz)[6]. 在靜態(tài)條件下, 機(jī)器人腕部六維力傳感器測得的力與力矩數(shù)據(jù)由三部分組成, 即: 1) 傳感器自身系統(tǒng)誤差; 2) 負(fù)載重力作用; 3) 負(fù)載所受外部接觸力. 若要得到負(fù)載所受外部接觸力, 需要消除傳感器系統(tǒng)誤差、負(fù)載重力作用兩方面的影響. 對于機(jī)器人運(yùn)動帶來的慣性力, 本文暫不考慮, 實際在機(jī)器人慢速運(yùn)動中, 慣性力的影響可忽略.
傳感器自身系統(tǒng)誤差方面, 六維力傳感器在空載狀態(tài)下的讀數(shù)并不為零, 本文假定傳感器自身的系統(tǒng)誤差為常數(shù), 并稱之作 “零點”. 六維力傳感器在安裝負(fù)載后, 負(fù)載與傳感器間的緊固安裝方式及緊固程度也會對傳感器零點造成影響, 因此傳感器零點無法在傳感器空載時準(zhǔn)確得到, 對于零點的測定必須在負(fù)載安裝的條件下進(jìn)行.負(fù)載重力影響方面, 在機(jī)器人運(yùn)動過程中, 負(fù)載姿態(tài)隨之改變, 而重力方向始終豎直向下, 因此負(fù)載重力對六維力傳感器數(shù)據(jù)的影響隨機(jī)器人的運(yùn)動不斷變化, 對于負(fù)載重力影響的消除需要根據(jù)當(dāng)前機(jī)器人姿態(tài)實時進(jìn)行.
在傳感器零點的補(bǔ)償方面, 文獻(xiàn) [8 – 10] 調(diào)整機(jī)器人至一系列特定姿態(tài), 部分姿態(tài)中重力對傳感器某一測量分量的作用可相互抵消, 進(jìn)而綜合對應(yīng)姿態(tài)的傳感器數(shù)據(jù)可消除重力影響, 求得傳感器零點.在負(fù)載重力補(bǔ)償方面, 文獻(xiàn) [2, 4, 11 – 14] 采用已知重量與重心位置的負(fù)載, 根據(jù)機(jī)器人姿態(tài)實時計算重力的影響, 消除了重力對六維力傳感器力與力矩值的影響. 一般情況下負(fù)載的重量、重心位置并不已知, 需要在線測定. 文獻(xiàn) [15 – 19] 默認(rèn)機(jī)器人基座標(biāo)系 Z 軸與重力方向相同, 進(jìn)而調(diào)整機(jī)器人使力傳感器到達(dá)特定姿態(tài), 直接得到負(fù)載重力大小,并通過變化機(jī)器人姿態(tài)標(biāo)定傳感器的安裝角度, 文獻(xiàn) [19] 進(jìn)一步按照力與力矩關(guān)系解得負(fù)載重心位置, 以此換算消除負(fù)載重力對傳感器力矩測量的影響. 文獻(xiàn) [8] 利用傳感器數(shù)據(jù)及力與力矩的關(guān)系, 采用最小二乘法求解負(fù)載重力大小及重心位置. 上述文獻(xiàn) [2, 4, 8, 11 – 19] 均默認(rèn)機(jī)器人基座標(biāo)系 Z 軸與重力方向相同, 但實際中工業(yè)機(jī)器人的安裝并不針對重力方向進(jìn)行特殊設(shè)置, 機(jī)器人基座標(biāo)系 Z 軸與重力方向往往存在偏角, 上述文獻(xiàn)中的重力補(bǔ)償算法未考慮此方面的誤差. 文獻(xiàn) [5] 在重力補(bǔ)償中考慮了機(jī)器人的安裝姿態(tài), 采用最小二乘法求得了機(jī)器人安裝傾角、負(fù)載重力大小及重心坐標(biāo), 對于重量為24.5 N 的負(fù)載, 消除負(fù)載重力作用后, 感知外力的最大誤差小于 1 N, 但文獻(xiàn) [5] 沒有考慮傳感器的零點問題.
綜上所述, 已有對工業(yè)機(jī)器人腕部力傳感器負(fù)載受力感知的研究中, 傳感器安裝角度通過標(biāo)定計算得到, 傳感器零點通過調(diào)整機(jī)器人至一系列特殊姿態(tài)進(jìn)行測定, 而機(jī)器人安裝傾角、負(fù)載重力大小及重心坐標(biāo)則利用不同姿態(tài)下的傳感器數(shù)據(jù)通過最小二乘法求得.
本文研究一種工業(yè)機(jī)器人腕部力傳感器負(fù)載受力感知方法, 與已有方法不同, 本文方法在通過機(jī)械定位保證傳感器安裝角度的基礎(chǔ)上, 利用不少于 3個機(jī)器人一般姿態(tài)下的傳感器數(shù)據(jù), 采用最小二乘法一次求得傳感器零點、機(jī)器人安裝傾角、負(fù)載重力大小、負(fù)載重心坐標(biāo)等參數(shù), 進(jìn)而消除傳感器零點及負(fù)載重力對受力感知的影響, 精確得到機(jī)器人末端負(fù)載所受的外部力與力矩數(shù)據(jù).
1 、計算模型建立
1.1 六維力傳感器力與力矩的關(guān)系
將六維力傳感器三個力分量的零點值記為
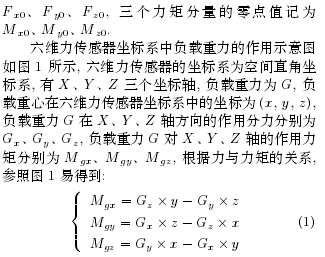
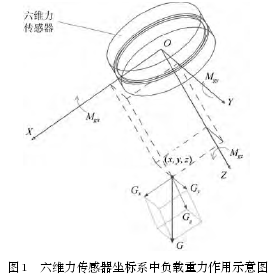
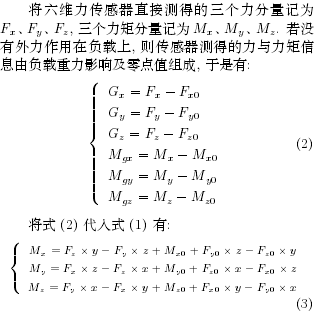
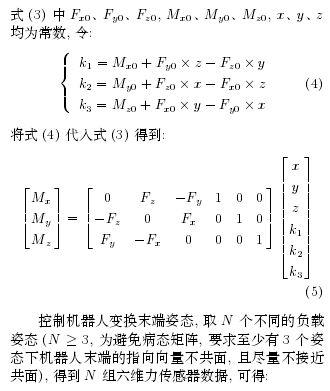
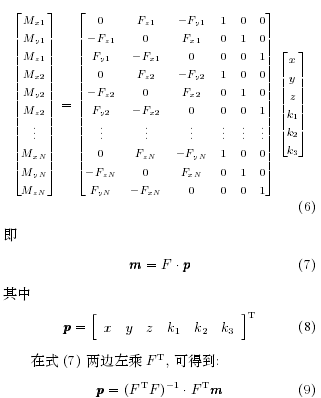
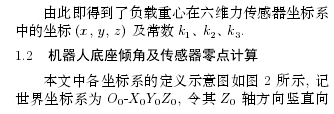
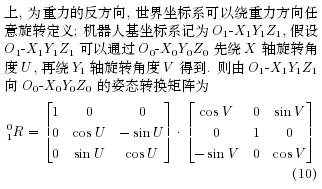
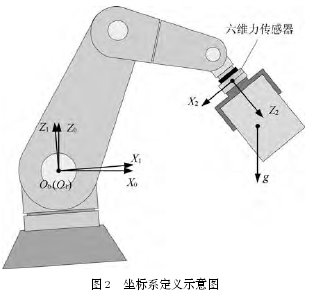
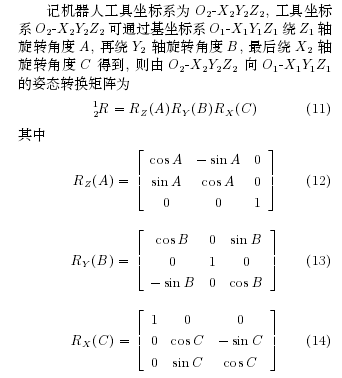
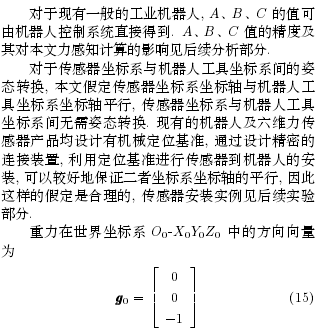
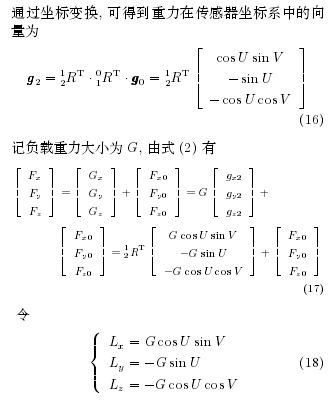
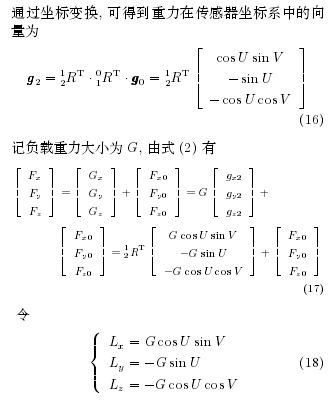
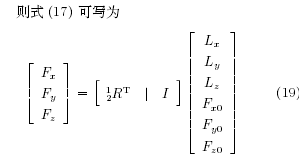
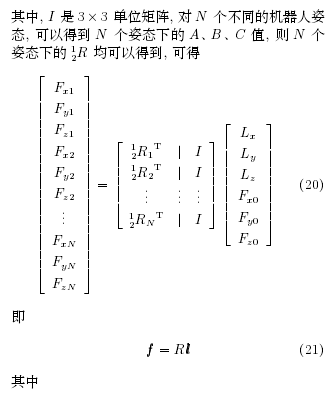
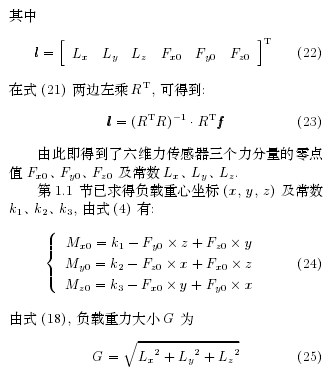
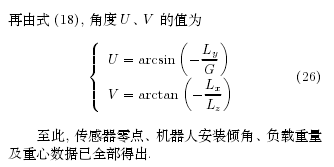
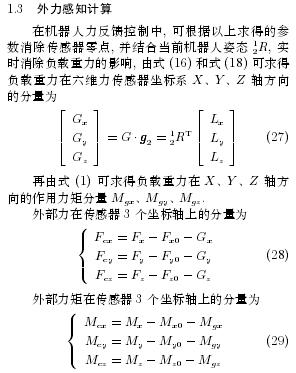
式 (28) 和式 (29) 即完成了對傳感器零點及負(fù)載重力影響的補(bǔ)償, 得到了負(fù)載所受的外部力與力矩.2 外力感知實驗2.1 實驗條件實驗采用 KUKA 公司的 KR210 機(jī)器人, 其主要參數(shù)見表 1. 六維力傳感器采用 ATI 公司的Omega190 型傳感器, 其測量范圍及精度參數(shù)見表2.

表 1 KR210 機(jī)器人性能參數(shù)
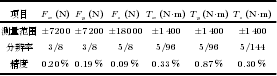
表 2 Omega190 技術(shù)參數(shù)
六維力傳感器在機(jī)器人末端法蘭的安裝方式如圖 3 所示, 傳感器自身的 2 個定位銷孔通過兩個定位銷與連接盤 2 實現(xiàn)定位, 連接盤 2 的中心圓孔通過連接盤 1 兩側(cè)中心的圓形凸臺與機(jī)器人法蘭中心的圓形凹腔實現(xiàn)中心定位, 連接盤 2 又通過穿過連接盤 1 的定位銷與機(jī)器人法蘭銷孔實現(xiàn)方向定位.這樣, 連接盤 1、2 兩側(cè)安裝面的平行度保證了傳感器安裝面與機(jī)器人法蘭安裝面的平行, 確保傳感器Z 軸與機(jī)器人工具坐標(biāo)系 Z 軸的平行, 連接盤 1、2的中心定位及 3 個定位銷的輔助定位, 確保了傳感器 X/Y 軸與機(jī)器人工具坐標(biāo)系 X/Y 軸的平行.
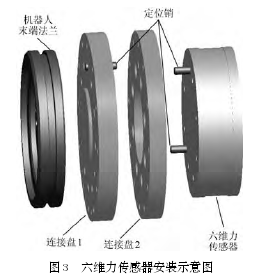
試驗中六維力傳感器負(fù)載采用如圖 4 所示的配重塊, 共采用 7 個配重塊, 每塊重約 27 kg, 首個配重塊通過連接法蘭與傳感器連接, 后續(xù)配重塊之間可通過連接孔逐個累加或拆下, 在試驗中實現(xiàn)負(fù)載重量的調(diào)整. 實驗用系統(tǒng)的實物照片如圖 5 所示.
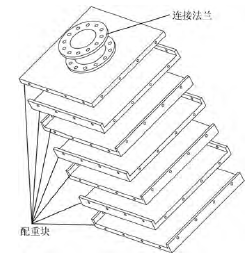
圖 4 試驗用配重塊示意圖
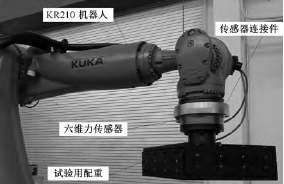
圖 5 系統(tǒng)實物照片
2.2 實驗過程及結(jié)果
為充分驗證所研究的算法, 分別對 7 種負(fù)載重量 (安裝 1 ∼ 7 個配重塊) 下的重力補(bǔ)償精度進(jìn)行實驗驗證.對每種負(fù)載, 調(diào)整機(jī)器人到表 3 所列的 8個姿態(tài)采集傳感器數(shù)據(jù). 試驗中傳感器采樣頻率為7 000 Hz, 連續(xù)采集 500 個求平均作為計算參考數(shù)據(jù). 給出安裝 7 個配重塊時采集的傳感器數(shù)據(jù)見表4.計算得到 7 種負(fù)載情況下的負(fù)載重力、機(jī)器人安裝傾角參數(shù)如表 5, 7 種負(fù)載情況下得到的傳感器零點如表 6, 而后調(diào)整機(jī)器人至 (A: 0?, B: 90?, C:0?) 的姿態(tài), 進(jìn)行外力感知計算, 在負(fù)載不受外力的條件下, 記錄消除傳感器零點及負(fù)載重力影響后的數(shù)據(jù)作為補(bǔ)償誤差, 誤差統(tǒng)計結(jié)果見表 7, 其中, Fe為重力補(bǔ)償后傳感器 3 個力分量的合力大小, Me為重力補(bǔ)償后傳感器 3 個力矩分量的合力矩大小, G為測得的負(fù)載重力大小, Mg為機(jī)器人姿態(tài) (A: 0?,B: 90?, C: 0?) 時負(fù)載對傳感器的力矩大小, 此時傳感器 Z 軸近似與水平面平行, 負(fù)載對傳感器的力矩可由 Mg= G × z 估算得到. δF表示 Fe相對于G 的百分比, δM表示 Me相對于 Mg的百分比.由表 7 可見, 消除傳感器零點及負(fù)載重力作用后, 感知外力誤差在負(fù)載重力的 0.28 % 以內(nèi), 感知外力矩的誤差在負(fù)載對傳感器力矩的 0.59 % 以內(nèi)
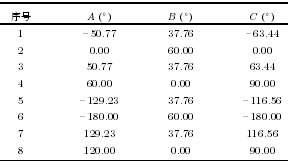
表 3 機(jī)器人姿態(tài)列表
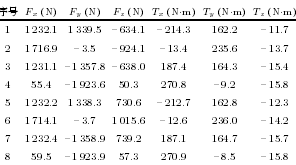
表 4 加載 7 個配重塊時的傳感器數(shù)據(jù)
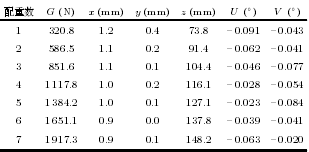
表 5 負(fù)載重力及機(jī)器人安裝傾角計算結(jié)果
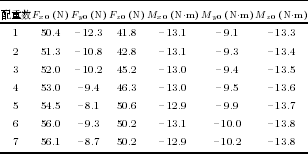
表 6 六維力傳感器零點計算結(jié)果

表 7 受力感知誤差統(tǒng)計
為驗證采用所述方法測量負(fù)載重力的精度, 通過其他測量方式實測所安裝負(fù)載的重量進(jìn)行對比.表 5 中得到的負(fù)載重力包含了安裝至六維力傳感器上所有零部件的重量, 同時也包含了六維力傳感器敏感端自身的重量. 而傳感器敏感端無法拆下單獨(dú)稱重, 因此, 在六維力傳感器空載情況下 (即不安裝任何零部件至傳感器), 進(jìn)行與上述完全相同的實驗過程, 計算得到傳感器敏感端自重為 35.5 N.表 5 中 負(fù) 載 重 力 G 減 去 傳 感 器 敏 感 端 重量, 即可得到安裝至傳感器上零部件的重量, 如表 8 “安裝重量計算值” 所示. 另一方面, 實測安裝至傳感器上零部件的重量. 使用 S 型拉力傳感器, 采用懸掛方式測量, 選用中諾傳感器公司 ZNLBS-200 型傳感器, 量程 200 kg, 測量精度0.05 %, 即 200 × 0.05 % = 0.1 kg, 傳感器示數(shù)乘重力常數(shù) g = 9.8 m/s2, 得到表 8 中 “安裝重量實測值”. 表 8 顯示, 負(fù)載重力測量的最大誤差為 1.2 N,接近于拉力傳感器的測量誤差.
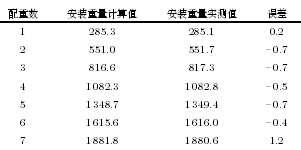
表 8 負(fù)載重力測量誤差統(tǒng)計 (N)
3、 感知誤差分析
3.1 傳感器測量精度的影響
表 2 給出了所用六維力傳感器的測量精度, 數(shù)據(jù)來自原廠給出的精度測試報告, 列出的精度指標(biāo)為測試中出現(xiàn)的全量程最大精度偏差. 其中, 力最大偏差為 18 000 × 0.09 % = 16.2 N, 力矩最大偏差為 1 400 × 0.87 % = 12.18 N·m. 實驗中對連續(xù)采集的 500 組傳感器求平均作為參考數(shù)據(jù), 因此, 傳感器誤差的影響達(dá)不到上述最大偏差數(shù)值. 對采集的傳感器數(shù)據(jù)求平均一定程度減小了數(shù)據(jù)的隨機(jī)波動,但不能完全消除, 波動的程度會造成最終的感知誤差. 為評估求平均后數(shù)據(jù)的波動程度, 在靜止?fàn)顟B(tài)下, 連續(xù)采集傳感器數(shù)據(jù)序列 65 000 組, 每 500 組求平均后得到 130 組數(shù)據(jù). 對于求平均得到的數(shù)據(jù)序列, 對 6 個測量分量, 求出每個分量數(shù)據(jù)序列中最大值與最小值的差 D 及標(biāo)準(zhǔn)差 σ, 以評價數(shù)據(jù)的波動程度, 見表 9.
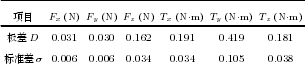
表 9 參考數(shù)據(jù)隨機(jī)誤差
對于力的感知誤差, 表 9 中的波動值遠(yuǎn)小于表 7中的誤差值 Fe. 對于力矩, 表 9 中的波動值則與表7 中的誤差值 Me相當(dāng). 因此, 對于表 7 中的感知誤差, 力矩感知誤差可以通過數(shù)據(jù)隨機(jī)誤差解釋, 而力感知誤差則存在其他原因.
3.2 機(jī)器人姿態(tài)角度誤差的影響
本文在計算中直接使用了機(jī)器人控制系統(tǒng)提供的 A、B、C 值, 即機(jī)器人工具坐標(biāo)系相對于基座標(biāo)系的角度值. 控制系統(tǒng)給出的角度值與真實值間的誤差將對最終的受力感知帶來誤差.按照所述算法, 仿真計算所述角度誤差對最終受力感知的影響, 仿真所采用的機(jī)器人姿態(tài)讀數(shù)與表 3 實驗數(shù)據(jù)完全相同, 所用負(fù)載質(zhì)量特性及機(jī)器人底座傾角數(shù)據(jù)采用表 5 中第 7 行的數(shù)據(jù). A、B、C值的誤差為人為指定, 得出不同 A、B、C 誤差引起的機(jī)器人在姿態(tài) (A: 0?, B: 90?, C: 0?) 下的受力感知誤差如圖 6 所示.

圖 6 機(jī)器人姿態(tài)誤差對受力感知的影響曲線
圖 6 中的 3 條曲線對應(yīng) A、B、C 值各自誤差對受力感知的影響. 由圖 6 可見, 受力感知誤差與角度誤差近似呈正比例線性關(guān)系, 機(jī)器人在姿態(tài) (A: 0?,B: 90?, C: 0?) 時, B 值誤差的影響遠(yuǎn)大于 A、C,因此, 下面分析 B 值誤差引起受力感知誤差的具體大小.對于工業(yè)機(jī)器人的絕對定位誤差, 機(jī)器人制造商往往不給出相關(guān)數(shù)值, 而需要使用者自行測量標(biāo)定[20−21]. 文獻(xiàn) [22] 對 KUKA公司 KR500 機(jī)器人(額定負(fù)載 500 kg) 進(jìn)行了誤差測量, 機(jī)器人工具坐標(biāo)系姿態(tài)角度誤差平均值為 0.21?[22], 文獻(xiàn) [23] 對ABB 公司的 IRB1 600 機(jī)器人進(jìn)行誤差測量, 最大角度誤差為 0.16?. 參照參考文獻(xiàn)中的測量結(jié)果, 假定 B 值誤差為 0.1?, 仿真計算由此造成的實驗中 7種負(fù)載下的受力感知誤差, 結(jié)果如表 10 所示.
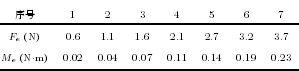
表 10 仿真受力感知誤差統(tǒng)計
對比表 7 與表 10, 對于力的感知誤差 Fe, 仿真結(jié)果與實驗吻合較好, 因此, 實驗中力的感知誤差可以由機(jī)器人角度誤差解釋. 而對于力矩的感知誤差Me, 對比表 10 與表 9, 表 10 中的誤差值被數(shù)據(jù)隨機(jī)誤差“淹沒”.上述的實驗與仿真計算可以表明, 表 7 中力的感知誤差主要由機(jī)器人姿態(tài)角度誤差引起, 力矩感知誤差主要由采樣數(shù)據(jù)的隨機(jī)誤差引起.
4、 結(jié)論
本文面向工業(yè)機(jī)器人在加工、裝配等應(yīng)用中精確測量外力的需求, 在機(jī)器人末端與負(fù)載之間設(shè)置六維力傳感器, 并研究一套標(biāo)定與計算方法, 在通過機(jī)械定位保證六維力傳感器與機(jī)器人安裝精度的條件下, 方法綜合考慮了負(fù)載重力作用、傳感器零點、機(jī)器人安裝傾角等因素, 利用不少于 3 個機(jī)器人姿態(tài)下的力傳感器數(shù)據(jù), 采用最小二乘法求得傳感器零點、機(jī)器人安裝傾角、負(fù)載重力大小、負(fù)載重心坐標(biāo)等參數(shù), 進(jìn)一步消除傳感器零點及負(fù)載重力對受力感知的影響, 精確得到機(jī)器人末端負(fù)載所受的外部作用力與力矩.實驗中對于重量從 320 N 到 1 917 N 的負(fù)載,重力補(bǔ)償后傳感器感知外力的誤差在負(fù)載重力的0.28 % 以內(nèi), 感知外力矩的誤差在負(fù)載對傳感器力矩的 0.59 % 以內(nèi). 實驗與仿真計算表明, 力的感知誤差主要由機(jī)器人姿態(tài)角度誤差引起, 力矩感知誤差主要由采樣數(shù)據(jù)的隨機(jī)誤差引起.相對已有方法, 本文方法的優(yōu)勢在于:
1) 應(yīng)用過程得到簡化: 已有方法需要先調(diào)整機(jī)器人到一系列特定姿態(tài)進(jìn)行傳感器數(shù)據(jù)采集, 首先完成零點標(biāo)定計算, 在消除零點的基礎(chǔ)上, 再調(diào)整機(jī)器人到一系列一般姿態(tài)進(jìn)行傳感器數(shù)據(jù)采集, 計算得到負(fù)載重力影響參數(shù), 前后需要 2 次機(jī)器人姿態(tài)調(diào)整及數(shù)據(jù)采集計算過程, 而本文方法只需 1 次機(jī)器人姿態(tài)調(diào)整過程, 得到不少于 3 個機(jī)器人姿態(tài)下的傳感器數(shù)據(jù), 即可計算得出全部所需參數(shù). 另一方面, 采用特殊姿態(tài)進(jìn)行零點標(biāo)定的過程中, 機(jī)器人運(yùn)動幅度大,操作時間較長, 且在空間有限的情況下難以操作, 而本文方法只需機(jī)器人的一系列一般姿態(tài), 機(jī)器人運(yùn)動幅度小、效率高, 在空間有限的情況下也可實施.
2) 有望提高感知精度: 相對于已有方法利用特定機(jī)器人姿態(tài)下的傳感器數(shù)據(jù), 本文方法中傳感器零點通過一般機(jī)器人姿態(tài)下的傳感器數(shù)據(jù)計算得到,計算結(jié)果更具一般性, 有望提高零點精度. 已有方法中傳感器零點通過獨(dú)立的過程求出, 沒有充分考慮零點與其他參數(shù)的耦合影響, 本文方法中所有參數(shù)聯(lián)立建模求解, 各參數(shù)間的耦合作用被充分考慮, 這也有助于提高結(jié)果精度. 另一方面, 本文方法能夠在機(jī)器人最終的目標(biāo)姿態(tài)附近進(jìn)行姿態(tài)變換完成零點標(biāo)定, 求得的零點更接近傳感器在機(jī)器人目標(biāo)姿態(tài)下的零點數(shù)值. 而已有采用特殊姿態(tài)進(jìn)行零點標(biāo)定的方法則很難有針對性地對特定姿態(tài)下傳感器的零點進(jìn)行標(biāo)定.
投稿箱:
如果您有機(jī)床行業(yè)、企業(yè)相關(guān)新聞稿件發(fā)表,或進(jìn)行資訊合作,歡迎聯(lián)系本網(wǎng)編輯部, 郵箱:skjcsc@vip.sina.com
如果您有機(jī)床行業(yè)、企業(yè)相關(guān)新聞稿件發(fā)表,或進(jìn)行資訊合作,歡迎聯(lián)系本網(wǎng)編輯部, 郵箱:skjcsc@vip.sina.com
更多相關(guān)信息
業(yè)界視點
| 更多
行業(yè)數(shù)據(jù)
| 更多
- 2025年4月 新能源汽車銷量情況
- 2025年4月 新能源汽車產(chǎn)量數(shù)據(jù)
- 2025年4月 基本型乘用車(轎車)產(chǎn)量數(shù)據(jù)
- 2025年4月 軸承出口情況
- 2025年4月 分地區(qū)金屬切削機(jī)床產(chǎn)量數(shù)據(jù)
- 2025年4月 金屬切削機(jī)床產(chǎn)量數(shù)據(jù)
- 2025年1月 新能源汽車銷量情況
- 2024年12月 新能源汽車產(chǎn)量數(shù)據(jù)
- 2024年12月 基本型乘用車(轎車)產(chǎn)量數(shù)據(jù)
- 2024年12月 軸承出口情況
- 2024年12月 分地區(qū)金屬切削機(jī)床產(chǎn)量數(shù)據(jù)
- 2024年12月 金屬切削機(jī)床產(chǎn)量數(shù)據(jù)
- 2024年11月 金屬切削機(jī)床產(chǎn)量數(shù)據(jù)
博文選萃
| 更多
- 機(jī)械加工過程圖示
- 判斷一臺加工中心精度的幾種辦法
- 中走絲線切割機(jī)床的發(fā)展趨勢
- 國產(chǎn)數(shù)控系統(tǒng)和數(shù)控機(jī)床何去何從?
- 中國的技術(shù)工人都去哪里了?
- 機(jī)械老板做了十多年,為何還是小作坊?
- 機(jī)械行業(yè)最新自殺性營銷,害人害己!不倒閉才
- 制造業(yè)大逃亡
- 智能時代,少談點智造,多談點制造
- 現(xiàn)實面前,國人沉默。制造業(yè)的騰飛,要從機(jī)床
- 一文搞懂?dāng)?shù)控車床加工刀具補(bǔ)償功能
- 車床鉆孔攻螺紋加工方法及工裝設(shè)計
- 傳統(tǒng)鉆削與螺旋銑孔加工工藝的區(qū)別