凸輪磨床 X - C 廓形誤差推導與仿真
2018-4-12 來源:北京第二機床廠有限公司 北京信息科技大學 作者:張培碩 李偉華 韓秋實 李啟光 等
摘 要: 在數控聯動加工時,由數控系統引入的跟蹤誤差是影響凸輪加工廓形誤差的主因之一,通過研究凸輪磨床跟蹤誤差,分別推導 X 軸、C 軸跟蹤誤差與廓形誤差計算模型,進一步推導出 X - C 軸聯動時跟蹤誤差與廓形誤差的計算模型。借助 MATLAB 工具編寫程序,分別實現數學模型仿真和模擬加工仿真,將實驗采集的跟蹤誤差采用不同的方法引入到仿真中,通過仿真結果對比,驗證了X - C 廓形誤差數學模型的正確性。
關鍵詞: 數控凸輪軸磨床; 跟蹤誤差; 廓形誤差; 仿真
在數控凸輪軸磨床加工過程中,X 軸和 C 軸要求隨加工形狀的不同瞬時啟停或改變速度,控制系統要實時精確地控制坐標軸運動的位置與速度,由于系統的穩態和動態特性影響了各坐標軸的協調運動和位置精度,從而產生了凸輪的廓形誤差。
數控凸輪軸磨床的伺服系統是影響磨削質量最關鍵的部分之一。作為執行部件的伺服驅動系統和電動機,能否準確執行給定的命令,對最終的磨削質量的影響是顯而易見的。凸輪軸磨床多采用砂輪架住復運動和工件旋轉運動的聯動來實現凸輪的磨削加工,在數控聯動加工時,伺服系統引入的跟蹤誤差是產生廓形誤差的一個重要因素。國內學者近幾年涉足了數控系統的跟隨誤差研究領域,其中,浙江大學朱年軍等推導了數控加工中穩態誤差的形成過程,并從直線和圓弧輪廓誤差模型出發探討了數控跟蹤誤差和輪廓誤差之間的關系
; 蘭州理工大學孫建仁等從分析輪廓誤差、跟隨誤差和位置環增益著手,分析兩種基本插補運動的輪廓誤差及其相應的跟隨誤差與輪廓誤差之間的關系; 南京航空航天大學滕福林等針對不同類型的位置給定,仿真分析了動態位置跟蹤誤差的產生機理,并提出采用 S 曲線給定可以大大減小實際系統的動態位置跟蹤誤差的方法。
以上 3種方法研究的對象都是通用的數控系統的簡單插補過程,未涉及到復雜聯動加工,如果將以上研究成果直接應用到加工凸輪的 X - C 聯動是不科學的。此外,華科技大學李勇等從系統傳遞函數入手,完成了數控凸輪軸磨床控制系統的建模,引入粒子群算法,優化了 PID參數,此方法沒有涉及到跟蹤誤差數學模型的推導問題。
本文主要完成工作是,在數控凸輪軸磨床的 X -C 軸聯動系統中,推導跟蹤誤差引起的廓形誤差數學模型,利用加工實驗采集到的跟蹤誤差值,借助 MATLAB工具實現仿真,來驗證數學模型。
1、 X - C 軸跟蹤誤差引起的廓形誤差數學模型推導
廓形誤差是指任意位置處實際廓形軌跡與理論廓形軌跡之間的最短距離。在磨削過程中,凸輪軸磨床通過兩軸聯動合成運動軌跡,完成凸輪廓形加工,由于各個軸都存在跟蹤誤差,運動分別會稍有偏差,因此,最終體現在磨削工件上的跟蹤誤差是二者合成的結果。
1. 1 X 軸跟蹤誤差引起的廓形誤差數學模型推導
對于凸輪軸磨床而言,X 軸跟蹤誤差,是指砂輪在伺服系統要求到達指定位置時,實際位置偏離所要求的理論位置的誤差值。設 X 軸跟蹤誤差為 Δx,如圖 1所示,凸輪輪廓偏差量為 εx。
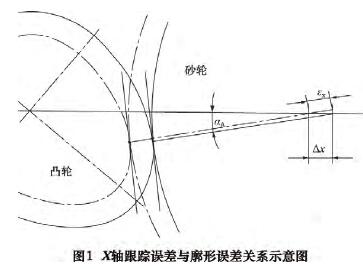
由幾何關系,可以得出:
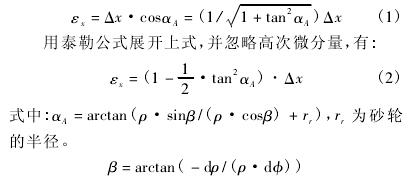
式( 2) 即為 X 軸的跟蹤誤差與廓形誤差的數學模型。
1. 2 C 軸跟蹤誤差引起的廓形誤差數學模型推導
凸輪磨床 C 軸的跟蹤誤差,是由于加工凸輪時實際磨削點在 C 軸上偏離了理論磨削點而引起的凸輪廓形的加工誤差。根據凸輪輪廓解析法,見圖 2,s0為基圓半徑,s 為升程值,δ 為轉角值,e 為偏心距,rr為滾子半徑。有:
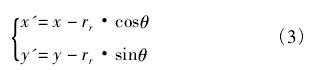
式( 3) 即為凸輪工作過程中廓形的直角坐標。
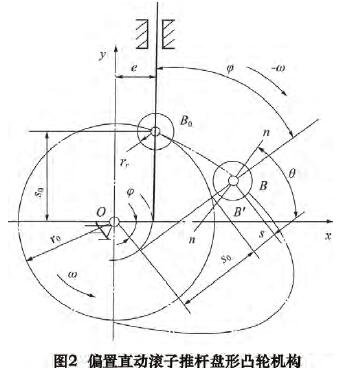
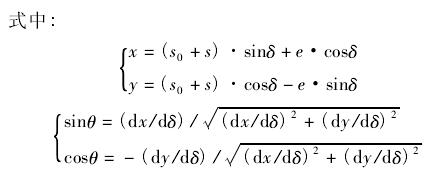
將滾子視為砂輪,該式就轉化為磨削模型,借助 X坐標計算廓形誤差,設極角誤差為 Δδ,容易得出:
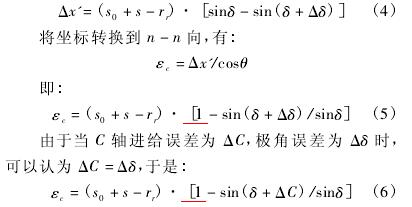
式( 6) 即為 C 軸跟蹤誤差與廓形誤差的數學模型。
1. 3 X - C 跟蹤誤差引起的廓形誤差數學模型在凸輪實際磨削時,C 軸跟蹤誤差與 X 軸跟蹤誤差是同時存在的,由于在式( 2) 與式( 6) 建立起的數學模型中,計算出的廓形誤差都是法向值,因此,綜合考慮 C 軸跟 X 軸,由它們造成的凸輪廓形誤差 ε 為:
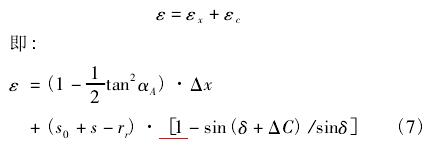
2 、實驗驗證
2. 1 實驗凸輪軸磨床數控系統簡介
數控凸輪軸磨床通常采用 X - C 兩坐標聯動實現凸輪輪廓的磨削,以 PMAC 卡為主要運動控制核心,控制 X 軸砂輪架前后往復移動和 C 軸工件主軸旋轉運動,Z 軸工作臺的左右移動實現凸輪軸的自動磨削加工循環和砂輪的自動修整,C 軸由電主軸驅動,X 軸采用直線電動機驅動,Z 軸由交流伺服電動機驅動。
磨削過程中,X 軸執行磨削進給和退避到安全位置,Z軸移動依次磨削凸輪軸上的各個凸輪。凸輪軸磨床數控工作原理圖如圖 3 所示。
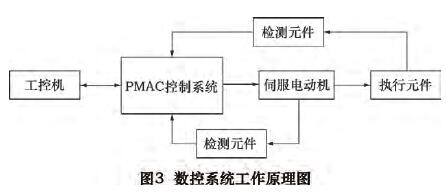
數控凸輪軸磨床數控控制原理圖如圖 4 所示,X軸直線電動機帶動砂輪架水平往復移動,C 軸伺服電主軸帶動工件主軸轉動,X - C 兩軸聯動,實現凸輪廓形加工,Z 軸伺服電動機帶動工作臺移動,完成整根凸輪軸的加工。
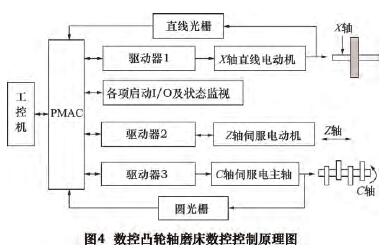
2. 2 跟蹤誤差采集
本文采用雙端口 RAM 數據讀取方式,利用雙端口所帶的函數進行數據采集,這種方式更加的方便,雙端口 RAM 函數封裝了 PMAC 數據讀取過程,用戶調用相應的函數即可從雙端口 RAM 中直接讀取運動參數,不需設置采集源及數據地址,雙端口 RAM 有很多運動參數采集函數,利用這些函數就能采集電動機的狀態、實時位置、速度、跟隨誤差等等。
采集的實現是通過編寫采集軟件來完成,為提高采集時間精度,軟件采用多媒體定時器,設置多媒體定時器采集間隔 20ms,定時器精度 1 ms,采集結果寫入數據文件。實驗共采集 3 組數據,按 C 軸轉速分別為 30 r/min、60 r / min、90 r / min,從低到高依次為數據 1、數據 2、數據 3。
2. 3 仿真驗證
2. 3. 1 仿真實現方法
( 1) 計算模型仿真
在伺服跟蹤誤差與凸輪廓形誤差數學模型建立的基礎上,借助 MATLAB 工具,編寫出仿真程序代碼,將凸輪升程擬合成凸輪廓形,伺服跟蹤誤差值由式 7 的數學模型引入,在法相將疊加到凸輪廓形上,可得到由單一曲線構成的凸輪實際廓形。該仿真方法部分MATLAB 程序如下:
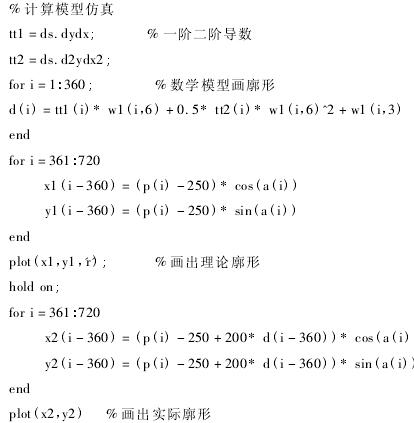
( 2) 模擬加工仿真
非圓曲面零件采用 X - C 聯動磨削時,實質是一種砂輪包絡,為了便于觀察與計算,常采用砂輪反轉法即工件不動、砂輪反向旋轉對非圓曲面零件加工過程進行分析。借助 MATLAB 工具,編寫出反轉法模擬凸輪廓形加工的仿真程序,跟蹤誤差分別由 X 軸跟蹤誤差 Δx 和 C 軸跟蹤誤差 ΔC 分別引入,程序運行時,砂輪反方向旋轉一周,可得到由多重砂輪輪廓逼近出的凸輪實際廓形。
該仿真方法部分 MATLAB 程序如下:
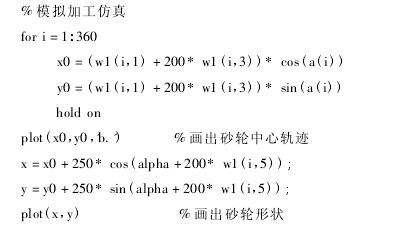
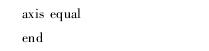
2. 3. 2 仿真結果對比分析
將采集到的 X 軸、C 軸跟蹤誤差的 3 組數據分別導入 MATLAB 程序,仿真出凸輪理論廓形與實際廓為了讓誤差效果明顯,誤差被放大了 200 倍,如圖5 ~ 7 所示。圖 5a、6a、7a 三幅仿真圖,由單一曲線構成,為本文推導出的數學模型仿真結果; 圖 5b、6b、7b三幅仿真圖,由多重曲線輪廓構成,為砂輪反轉法模擬凸輪加工的仿真結果。將圖 5 ~ 7 中上下兩幅圖,分別進行對比,可以得出廓形誤差曲線整體變化趨勢基本一致,桃尖整體位置沿 Y 軸正方向偏移,隨著 C 軸速度的依次增加,偏移量依次增加。
分析不同仿真方法的廓形對比圖,可發現較之于理論廓形,凸輪實際廓形曲線明顯向上偏移,二者仿真結果基本一致,但是計算模型仿真出的實際廓形與反轉法模擬加工仿真相比,誤差有輕微波動,分析原因,在實際加工過程中,除去伺服跟蹤誤差以外還有其他誤差因素影響,有一定程度的波動是合理的。這就證明了推算的伺服跟蹤誤差與廓形誤差的數學模型式( 7) 是正確的。
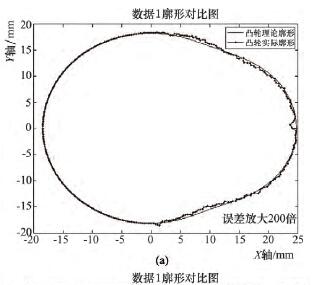
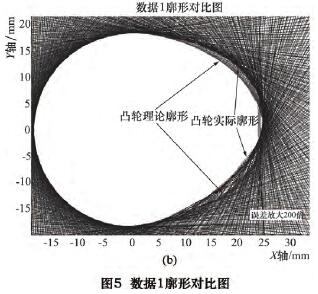
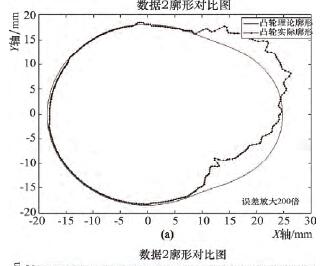
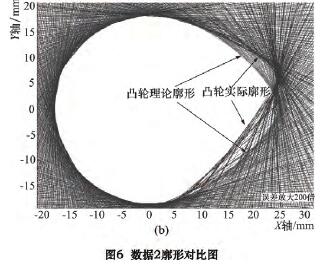
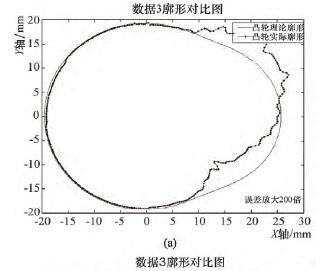
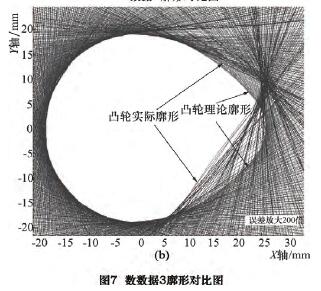
3 、結語
通過對凸輪軸磨床 X 軸、C 軸跟蹤誤差引起的廓形誤差研究,提出了 X - C 聯動時伺服系統的跟蹤誤差與廓形誤差的數學模型。采集跟蹤誤差,借助MATLAB 工具編寫的兩套仿真程序,對模擬加工出的凸輪廓形進行比對分析,最終驗證了數學模型的正確性。
該模型的提出,為數控凸輪軸磨床伺服跟蹤誤差實時反饋系統的研究奠定了基礎,對進一步提高凸輪磨削精度有重要意義。
投稿箱:
如果您有機床行業、企業相關新聞稿件發表,或進行資訊合作,歡迎聯系本網編輯部, 郵箱:skjcsc@vip.sina.com
如果您有機床行業、企業相關新聞稿件發表,或進行資訊合作,歡迎聯系本網編輯部, 郵箱:skjcsc@vip.sina.com