機床滑座變形問題的分析與研究
2025-4-15 來源: 沈陽機床股份有限公司 作者:王云萍 劉東波
【摘要】: 滑座作為機床結構中的主要部件直接影響整機的幾何精度與運動精度。分析影響機床滑座變形的因素,研究相應的解決方案并進行實驗論證。從而對保證機床的加工精度,提升加工性能有著重大影響。
十字滑臺式結構作為典型的機床結構形式,在立式加工中心、臥式銑鏜床、臥式加工中心等機床型譜中被廣泛采用。滑座是十字滑臺式結構中的重要組成部件。以立式加工中心為例 : 滑座向上連接工作臺,向下連接床身,且負責兩個軸的運動,在整機結構中起到承上啟下及傳動樞紐的作用。所以,滑座的自身精度直接影響機床的幾何精度和運動精度。但是,由于滑座自身結構所限,在實際的生產活動中容易產生變形。本文將嘗試從結構設計、毛坯鑄造、切削加工、裝配工藝等整個生產鏈條分析滑座變形的原因,研究相應的解決方案并通過實驗來印證方案效果。
1. 結構設計因素引起的滑座變形
滑座由于不合理的結構設計導致的變形,主要是由于研發設計過程中未能充分考慮結構剛度問題,包括幾點 : ①兩側導軌懸伸量過長 ; ②設計內部筋格布局未能兼顧重要受力位置 ; ③滑座內部開口結構。
前兩點問題在于研發人員設計經驗不足、考慮不周。滑座兩側導軌懸伸量過長時可以加裝副導軌或牽拉裝置解決工件剛度不足導致變形的問題。另外,當設計內部筋格布局時不必拘泥于對稱原則或是刻意追求質心位置。雖然質心驅動設計的十字滑臺結構具有較好的對稱性,能夠減輕機床在切削時的自激振現象,提高機床整機的固有頻率。但應優先保證諸如導軌面、滑塊面、電機座面、軸承座面等主要受力位置的結構剛度,可以結合有限元分析軟件進行拓補優化合理布局。
然而,許多技術人員往往忽略第三點 : 滑座內部開口結構也是影響工件整體剛度的重要因素。如圖 1、圖 2 所示某型立式加工中心滑座 :軸承座一側設計成閉合結構、相反電機座一側則為開口結構。經 AnsysWorkbench 靜力學分析,當僅施加額定載荷時,電機座一側相較于軸承座一側變形量大0.005mm;當施加極限重載及沖擊載荷時,開口結構的電機座一側變形量成倍放大。因此在設計過程中應盡量避免滑座內部的開口結構。
2.毛坯鑄造環節滑座變形分析
毛坯鑄造環節有以下幾個誤區容易引起滑座變形 : ①毛坯尺寸公差等級過大,特別是需要機械加工面的余量。②一味提高鑄件牌號,錯誤地意圖通過提高工件機械強度來提高剛性。下文將具體分析這兩點如何影響滑座變形。
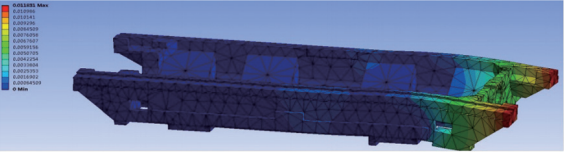
圖 1 軸承座側靜力學模型圖
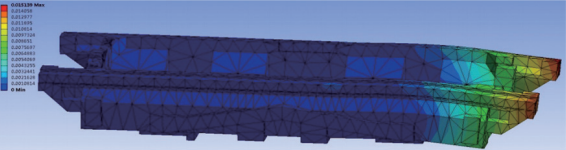
圖 2 電機座側靜力學模型圖
關于毛坯機械加工余量,可根據 GB/T6414-1999《鑄件尺寸公差與機械加工余量》國標查詢確定。然而實際生產活動中,鑄造廠家往往將機械加工余量等級放至 H~K 級別(以 2000mm 內的滑座為例,加工余量可達 6~15mm)。究其原因無外乎以下兩點 : ①鑄件以重量結算價格,廠家追求利潤有意放大加工余量。②鑄造缺陷大多出現在毛坯表層,放大余量,并經過加工后可降低廢品率。
過大的毛坯余量勢必增大后續切削加工環節的金屬去除量,累積更大切削殘余應力,從而加劇滑座變形。與此同時過多無用的毛坯余量也會提高物料成本及機加工費用。因此必須降低毛坯余量。經實際檢驗 : 機械加工余量等級確定至E~G 級別較為合適,即長度在 2000mm 以內的滑座理想的加工余量為 3~5mm。
關于鑄件牌號問題,設計時機床大件通常選用HT200或HT250。然而部分技術人員一味提高鑄件牌號至 HT300~HT350,將機械強度與結構剛度混為一談,單純地認為提高機械強度能夠減小工件變形,殊不知滑座變形主要是工件的整體彈性變形及加工面在切削過程中熱力耦合作用下的微觀變形,很少能到達到整體塑性變形階段。剛度是主要因素,而剛度是結構性質,與材料的彈性模量及工件的結構有關。另外由于鑄件抗拉強度與硬度存在一定的對應關系式 :
當σb≥196MPa時,HB=RH(100+O.438σb )(1)當σb<196MPa時,HB=RH(44+0.724σb )(2)式中相對硬度 (RH) 值主要由原材料、熔化工藝、熱處理工藝及鑄件的冷卻速度所確定。如式中所述 : 提高鑄件強度同時勢必會增加硬度,反而增大鑄造應力及加工環節的切削阻力導致滑座變形,因此如無特殊原因不宜提高鑄件牌號。
3.切削加工過程中變形因素分析
滑座在切削加工過程中產生的變形主要包括 : ①產前準備期間不規范的定位、卡壓產生的變形。②加工過程中熱力耦合作用產生的導致工件微觀相變或變形。③工藝編排不合理造成應力累積變形。
機加工產前準備期間工件不合理的定位、卡壓容易導致滑座變形。首先工件定位位置與卡壓位置應盡量保持在一條線上。簡單舉例 : 如圖 3所示某型滑座底面加工示意圖,其定位位置與卡壓位置不在一條線且該卡壓方式沒有在四周加側頂裝置,夾緊時僅靠摩擦力限制自由度,故需較大的壓緊力。經有限元分析軟件計算,螺栓夾緊力為45000N,在壓緊時受彎曲應力導致變形量為0.09mm。圖 4 所示定位位置與卡壓位置在一條線,并加裝側頂裝置限制自由度,其螺栓夾緊力為 10000N,而且滑座幾乎不受彎曲應力,變形量
幾乎為 0。
3
圖 3 (定位位置與卡壓位置不在一條線)
4
圖 4 (定位位置與卡壓位置在一條線上)
實際生產活動中,操作者往往錯誤地認為粗加工時采用圖3裝夾方式不會影響后續加工精度,工件會快速恢復形狀。然而經長期實踐證明,工件經此方式長時間裝夾后 7~24 小時自然時效才能基本恢復,對精加工有著深遠影響。
金屬在切削加工過程中刀具對工件產生強大的擠壓力,使切削層在高應力,高應變,高切削溫度的情況下與基體產生分離,形成已加工表面。
故此,已加工工件中存在較大的殘余應力,也是滑座變形的重要因素。本文作者作為基層技術人員未在此方向上做深入研究,僅根據實際工作經驗提出應對切削殘余應力的若干措施 :
(1)盡量減少工件總的金屬去除量即毛坯余量。
(2)滿足設計要求條件下較低的毛坯硬度。
(3)切削參數方面宜采用平轉數,小吃刀量、快進給的方式。
(4)加入人工時效處理工藝。
加工工藝是影響滑座變形的另一個因素,不合理的工藝規程編排容易造成應力累積導致變形。滑座作為機床機械結構中重要部件在毛坯出廠前和粗加工后都應進行時效處理,如去應力退火、振動時效等。另外,各工序間應適當進行自然時效以充分釋放應力。
舉例說明某型立式加工中心滑座工藝規程 :毛坯出廠退火→粗底面→粗上面→四周面→人工時效處理→鉗序攻絲→油漆→精底面→精上面→磨底上面→成品檢驗(上訴各工序間時效 7 小時)然而實際生產活動中,機加工車間由于指令計劃更改或其它因素影響經常變更或加速排產,導致工序過度集中或時效時間不充分從而影響工件的應力釋放。
4. 滑座裝配環節變形因素分析
在滑座裝配環節中,部件或整機的裝配剛度是影響滑座變形的主要原因,而裝配剛度取決于部件的結構剛度及裝配工藝的編排,實際生產活動中應注意以下幾點 ;
(1)滑座在機加工后、裝配前應在臺位螺栓松開狀態下靜置 24 小時以充分釋放鑄造及加工環節的內應力。
(2)導軌螺栓與擠塊螺栓擰緊順序為從中央到兩端的把緊方式,保證直線導軌與滑座導軌面充分貼合。
(3)擠塊及壓板壓緊導軌側面的方式壓力較大,容易造成導軌基準面擠壓變形。可酌情改為偏心螺釘方式壓緊。
5. 結語
綜上所述,滑座作為機床結構中的主要部件直接影響機床整機精度。本文從滑座結構設計、毛坯鑄造、切削加工及整機裝配幾個環節闡述和分析了其變形的主要因素及控制措施。對滑座的整個生產鏈條具有一定的借鑒意義,從而有效控制滑座變形問題,能夠快速提升機床產品性能和行業的競爭力。
投稿箱:
如果您有機床行業、企業相關新聞稿件發表,或進行資訊合作,歡迎聯系本網編輯部, 郵箱:skjcsc@vip.sina.com
如果您有機床行業、企業相關新聞稿件發表,或進行資訊合作,歡迎聯系本網編輯部, 郵箱:skjcsc@vip.sina.com
更多相關信息