摘要:針對主軸回轉熱誤差包含的多種誤差分量,采用雙向正交法測量了不同轉速溫度場下數控車床主軸熱變形所引起的回轉誤差。以復向量描述主軸回轉精度理論為基礎,利用FFT誤差分離方法,從傳感器測得的信號中分離并除檢棒的安裝偏心及熱變形導致的回轉中心的偏移量,從而得到精確的主軸回轉熱誤差信息,進而評定數控機床主軸熱變形對加工精度的影響。
關鍵詞:主軸熱變形;復向量;誤差分離;回轉精度評定
"機械零件的加工精度與機床熱誤差引起的制造誤差息息相關,文獻[1-2]的研究表明:在精密加工中,熱變形所引起的制造誤差占總制造誤差的50%~70%。主軸系統作為機床的重要組成部件,其熱變形誤差是機床熱誤差的主要來源[3-4]。因此,主軸系統熱特性的研究與分析是保證機床的制造精度關鍵所在。機床工作時,在內外熱源的作用下,主軸系統的組成部分形成各自的溫度場,各組成部分熱膨脹性能不一致會導致空間機械結構發生熱變形,引起零件的加工誤差。受動力學、靜力學、熱變形以及軸承和軸頸的加工誤差等的影響,數控車床主軸瞬時回轉軸線在空間位置是不斷變化的。實驗結果表明:精密車削的圓度誤差約有30%~70%是由主軸的回轉誤差引起的,且機床的精度越高,所占的比例越大[5]。主軸回轉精度反映了車床的動態性能,與車床所能達到的加工精度息息相關。車床加工過程中產生的主軸熱變形也主軸回轉精度有較大影響,對其進行檢測和補償控制可提高加工精度[6]。隨著高速高精機床的廣泛應用,檢測精度和效率逐漸提高,檢測方法從靜態檢測迅速向動態、在線檢測發展。軸系回轉誤差的測量已從單向測量轉向多點測量,測量精度不斷提高[7]。
測量主軸回轉熱誤差時,實際的主軸回轉軸心是不可見的,只能通過對裝卡在主軸上的標準檢棒外部輪廓的測量來間接獲取主軸軸心的運動軌跡。這樣一來,測量結果不可避免地混入了標準檢棒的形狀誤差和安裝誤差。對于具有高回轉精度的精密主軸,混入的形狀誤差或安裝誤差有時甚至會淹沒掉微小的主軸回轉誤差,所以對于高精密車床主軸回轉誤差的測量,混入的形狀誤差和安裝誤差不能忽略,必須采取有效的方法從測量信號中分離并去除由測量系統引入的、影響測量精度的信號分量,從而獲得主軸回轉精度[8-9]。本文以復向量描述的主軸回轉精度理論為基礎,運用FFT方法對信號進行分解處理,通過分析剔除對主軸回轉精度無影響的成分,提取出主軸回轉精度,進而評定機床主軸熱變形的回轉精度并分析其加工精度。
1、主軸熱誤差測量原理
主軸系統的熱變形包括軸向熱竄動和徑向熱變形。測量軸向熱竄動時,只需在主軸懸空端安置一個電渦流傳感器進行測量即可。主軸徑向熱變形是二維變量,應采用雙向正交法進行間接測量。測量結果包含了主軸制造和安裝的誤差、熱變形等誤差,要準確評估主軸熱變形對加工精度的影響,需要從綜合誤差中將熱變形誤差分離出來。機床主軸回轉精度的測量原理是:主軸電機帶動主軸做回轉運動時產生的徑向跳動,使電渦流傳感器與被測件表面間的距離發生變化,通過電渦流傳感器和信號轉換裝置將其轉換成模擬電壓信號,進行定時采集。主軸回轉精度對精加工零件的形狀精度和表面粗糙度有很大的影響,是評價機床加工精度的重要指標,可預測機床在理想加工條件下所能達到的最小形狀誤差和粗糙度,也能用于機床加工補償。
主軸熱變形所引起的徑向跳動量如圖1所示。Oo為理想回轉中心,是由主軸支承部件確定的安裝中心;Or為主軸實際回轉中心;Om為基準球的幾何中心;Rm為基準截面的徑e為檢棒的安裝偏心量;θ為檢棒回轉角。電動機運轉一段時間后,主軸支承軸承的熱變形會導致主軸系統的回轉中心Or在不同的溫度場下產生偏移,加之運動過程中主軸的隨動,使得電渦流位移傳感器與被測圓柱表面間的距離發生實時改變,通過電渦流傳感器和信號轉換器測量得到包含誤差信息的位移變化的電壓值。
如圖1所示,兩個位移傳感器檢測的位移信號dx 和dy 分別為
dx =ecosθ+rx(α)+Sx(θ) (1)
dy=esinθ+ry(α)+Sy(θ) (2)
式中,ecosθ、esinθ分別為偏心e 在X、Y 方向上的投影;rx(α)、ry(α)分別為徑向運動誤差r(α)在X、Y 方向上的投影;Sx(θ)、Sy(θ)分別為檢棒相差90°的兩對應點的形狀誤差。
測量過程中,采用形狀誤差遠小于回轉誤差的高精度檢棒為基準。
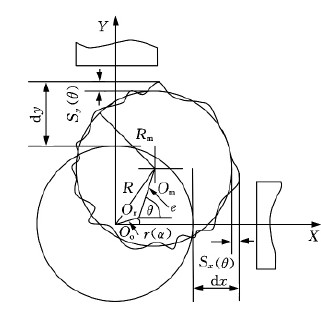
圖1 熱變形誤差信號分析
在高精度檢棒形狀誤差可忽略的情況下,dx 和dy 是圓截面中心的位移在X、Y 方向的分量。換言之,由于安裝偏心的存在,由dx 和dy 所確定的是圓截面幾何中心的軌跡,而不是回轉軸心的軌跡。所以,為了盡量減小偏心對dx、dy 的影響,使測量結果更能真實地反映(α),就必須盡量減小或消除偏心量e。
2、誤差運動的數學模型
徑向運動誤差具有周期性和徑向性的特征:周期性是指圓輪廓信號具有以2π為周期變化的性質;徑向性指圓形橫截面的實際輪廓是一個復雜封閉的曲線輪廓,輪廓上各點的徑向尺寸有差異,大小不同。被測元件徑向回轉運動的傅里葉級數描述為
式中,n為被測圓輪廓諧波分量的最大諧波階數;S0為被測圓輪廓數據的直流分量,與傳感器初始安裝位置有關;Ai、Bi分別為沿X 軸和Y 軸的i階次諧波分量的幅值。式(3)的實際意義是,周期性的徑向誤差運動可分解成許多個做圓周運動的倍頻分量。為了得到真正的徑向運動誤差,應從測量數據中除去被測元件的直流分量和偏心量e。
3、主軸熱誤差測量
如圖2所示,測試對象為FANUC數控車床,分別在主軸電機、前法蘭、主軸箱前壁等處布置磁吸式高精度溫度傳感器,同時采集環境溫度的變化。機床在不同轉速下空運行,其主軸具體運行情況如表1所示,車床主軸各部件溫升曲線如圖3所示。各部件溫升相異,形成不同的溫度場。在室溫變化不大的情況下,電機發熱溫升較快,前法蘭亦有較大溫升。
1.電機Y 軸負方向 2.電機X 軸正方向 3.前法蘭X 軸正方向
4.前法蘭Y 軸負方向 5.主軸前端壁Y 軸負方向
6.主軸前端壁Y 軸正方向 7.室溫
圖3 機床主軸各部件溫升圖
3.2 主軸徑向誤差運動檢測如
圖4所示,采用雙向測量法,即兩傳感器正交分布安裝進行檢測。檢測試驗中,用主軸帶動檢棒的回轉來測試主軸的熱誤差。沿檢棒軸向布置2組非接觸式電渦流位移傳感器(每組2個,共4個)。每組2個位移傳感器沿X、Y 坐標軸方向上呈正交分布安裝,即圖4中的S1、S2、S3、S4。主軸的回轉誤差信號通過這4個位移傳感器采集,MX、MY分別為設置在X、Y 方向的高速數據采集裝置。電渦流位移傳感器分辨力為25nm,數據采集儀的采樣頻率最高為1MHz。
圖4 雙向測量法原理
因測試部位為圓柱孔,不能直接用表檢測,故用一根精密檢棒插入主軸錐孔內,進行動態測量,如圖5所示。
軸向誤差是一維誤差,故只在檢棒端面安裝位移傳感器進行測量即可。車床主軸的軸向竄動主要影響工件端面的幾何形狀精度,會產生端面相對于外圓柱面的垂直度誤差,但對圓柱工件的外圓輪廓的加工沒有影響。主軸的軸向熱伸長量隨溫度場升高而加大,端面跳動量在不同轉速、不同溫度下呈增加趨勢,其相應信號由圖4中所示的S5采集。
4、熱誤差分離及主軸回轉精度評定
測量元件的形狀誤差和安裝偏心對主軸回轉精度測量結果產生比較大的影響,所以,測量數據中不可避免地混入了形狀誤差和安裝誤差,只有有效地分離出形狀誤差和安裝誤差,才能對主軸回轉精度進行準確評定。徑向熱變形誤差可分解為不同階次的信號,非接觸測量時,測量數據主要由測量檢棒的圓度誤差信號、截面粗糙度的誤差信號和波紋度的誤差信號組成,其中,主軸圓度誤差屬宏觀誤差,為低頻信號;粗糙度誤差屬微觀信號,為高頻信號;波紋度誤差是介于圓度誤差和表面粗糙度之間的中頻信號。主軸回轉誤差中以周期性成分為主,并且主要由1階、2階、3階和4階的低階諧波信號組成。因作為基準軸用的試驗檢棒加工精度高,所以對檢棒的圓度誤差可忽略不計,且熱變形誤差分離主要針對徑向方向進行處理。
誤差分離中,首先應從采集信號S(θ)中除去被測元件的直流分量A0,得到徑向運動誤差Sn(θ)。Sn(θ)具有周期性和徑向性。周期性是指圓周工件輪廓信號的變化是以2π/i為時長、多次重復出現;徑向性是指被測件的同一個橫截面上的半徑在不同位置處各不相同,存在差異性。所以主軸回轉時在誤差敏感方向上的誤差運動可以看成是多個不同倍頻的誤差信號的疊加。被測元件敏感方向上的回轉運動Sn(θ)的傅里葉級數展開為
i≥2時,Si為每周圈具有i個波峰的內擺線。主軸熱誤差主要由兩部分組成:① 主軸支承軸承熱變形導致回轉中心發生的偏移,在信號中反映為直流分量的變化;② 從測量結果中除去被測元件的偏心量就可獲得熱變形導致的徑向運動誤差
:S2(θ)=Σni=2(Aicos(iθ)+Bisin(iθ)) (7)
本文誤差信號的頻譜分析借助于FFT方法,將時域采集到的離散誤差信號變為頻域信號,以便分析其誤差組成。所以,數據處理時,用傅里葉級數分離檢棒的安裝偏心量e,也可分離出采樣數據中的檢棒的形狀誤差,從而提取出主軸回轉誤差,流程如圖6所示。
圖6 數據處理流程圖
圖7所示為X、Y 方向上的原始數據,其中微小的噪聲數據為主軸隨機跳動所致。圖8為兩者的頻譜分析圖,其中,具有最大幅值的頻率接近零,對應著傳感器的初始安裝位置,其一階分量為檢棒的安裝偏心量。圖9所示為去除直流分量后X、Y 方向的誤差測量數據,主要由安裝偏心和運動誤差組成。圖10所示為未分離安裝偏心e情況下,在不同時刻(主軸分別以240r/min,480r/min,960r/min速度運行結束時)的徑向回轉誤差的變化情況,盡管有溫升的變化,但是偏心量基本不變,均在21μm左右。圖11所示為直流分量分別在240r/min,480r/min,960r/min結束時的情況,它反映了回轉中心隨溫度的變化而發生了偏移。
(b)主軸Y 向原始數據減去直流分量
圖9 去除直流分量后的誤差數據
表2所示為在不同轉速、不同的溫度場下,基于圓圖像法并采用最小二乘圓方法獲得的徑向熱跳動量變化所產生的主軸系統回轉精度。如表2所示,隨著主軸系統溫度的升高,熱變形所引起的徑向運動誤差相應增大。主軸系統的溫度上升愈大,其熱變形愈嚴重。
5、結論
(1)對測量數據進行FFT諧波分析可知,不同轉速下的主軸回轉偏心量基本保持不變,其一階頻率與主軸回轉頻率一致。
(2)主軸在軸向和徑向均有熱變形,因此,適時地控制機床軸系的溫升,可以減小機床主軸的熱變形,提高其加工精度。
(3)全面分析了機床主軸回轉熱誤差,由研究結果可以看出,車床主軸在熱溫升的影響下,其回轉誤差有加速增大的趨勢。通過對實驗測量數據的分析及回轉誤差評定研究,可以評測機床熱變形對主軸回轉誤差的影響,獲得主軸在不同的溫度穩定場下,其加工精度的變化狀況,為后續機床熱變形補償提供更加可靠的實驗依據。
如果您有機床行業、企業相關新聞稿件發表,或進行資訊合作,歡迎聯系本網編輯部, 郵箱:skjcsc@vip.sina.com