大型曲軸磨床典型結構與先進的磨削工藝
2014-1-19 來源:常州機電職業技術學院 作者:虞行國 劉江
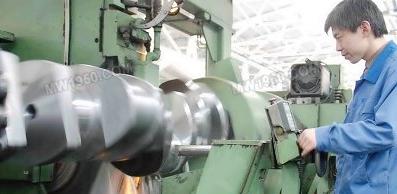
圖一
對于曲軸加工設備來講,磨床是使產品零件達到工藝要求的最終加工機床,固對其精度要求極高、復雜程度極難。對于工件長度超過6m,重量超過5t,工件的主軸頸和連桿頸粗糙度值要達到R a=0.4~0.6μm,主軸頸、連桿頸直徑公差在0.008mm,主軸頸和連桿頸直線度在0.01 / 200 mm,連桿頸圓柱度0.015 mm,連桿頸分度±15′的技術要求并且加工不同角度和不同偏心量的連桿頸磨削的大型曲軸磨床,其要求就更高了。
根據目前現有設備狀況和加工工藝,曲軸在磨床上的加工是分兩步執行的,也就是說加工磨削主軸頸和連桿頸是由兩種機型分開實施的,這主要是受到設備結構的限制和約束。一般磨削主軸頸選擇在大型的普通外圓磨床進行,曲軸依靠外圓磨床的頭架單驅動,在二頂尖和中心架的支撐下逐步對主軸頸進行磨削。在磨削主軸頸的過程中,產品的尺寸精度和技術要求都由人工直接干預。特別是對中心架兩個方向支撐力量的控制,這就要看操作工人的熟練掌握程度,但要長期依靠人為因素來保證質量穩定是難以做到的,也是不科學的。如圖1所示,在加工磨削連桿頸直徑時,是選擇專用的曲軸磨床來進行加工的。這種曲軸磨床的頭尾座卡盤是可以以頭尾座中心軸線為基準,按照曲軸主軸頸和連桿頸的沖程偏心量進行調整,使頭尾座卡盤夾持連桿頸的中心圍繞頭尾座主軸的旋轉中心,對連桿頸直徑進行磨削加工。如圖2所示。
因為曲軸技術設計的原因,它在長度質量分配上存在著比較大的偏心,如果不采取措施,曲軸在加工旋轉中會出現運轉不均勻的現象并產生有離心力狀況,這樣磨削加工的表面粗糙度肯定會受到影響。所以在機床的頭尾座后側都配制了配重裝置,通過觀察頭尾座的驅動電動機電流的情況進行調整,從而可以改善和均衡頭尾座的旋轉穩定性。因為曲軸本身結構的原因,在頭尾座同時夾緊曲軸兩頭時,頭尾座在旋轉時不同步就會造成曲軸的扭曲而影響加工精度。目前為了保證頭尾座的同步,曲軸磨床頭尾座的傳動方式有兩種,一是通過同步軸傳遞,即頭座作為主傳動經過一系列的傳動鏈傳遞到尾座,使它們實現曲軸磨床的頭尾座卡盤同步,保證曲軸在運轉過程中不造成扭曲的現象。這種傳遞的方式制造成本低,但不可避免地存在機械傳動鏈過長有間隙和磨損的現象,給調整帶來諸多的不便。另一種是利用頭尾座旋轉作為兩軸,采用數控同步技術,使頭尾座在旋轉的過程中旋轉誤差達到最小。有的在采用了頭尾座旋轉作為兩軸的數控同步技術的制造廠家,為了防止因設備故障和突然停電造成頭尾座失步,使設備損壞以及造成產品的報廢,把砂輪電動機作為突然停電后的大直徑砂輪的慣性當作發電機使用,把發出的電提供給頭尾座電動機作為臨時電源,臨時保證頭尾座能夠在短時間內有旋轉的空間防止故障的擴大。同時為防止頭尾座電器系統本身的故障而引起失步,在頭尾座機械部分設計有超越離機構作為保護裝置,在實際運行中因頭座調速系統模板故障造成頭尾座失步3°,正因為在該裝置的作用下防止故障進一步擴大和保全近30萬元的工件報廢。
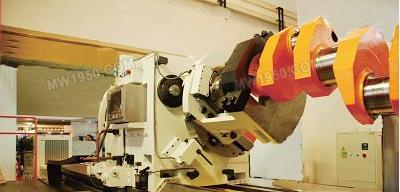
圖二
曲軸屬于細長軸零件,在加工時會形成中間下垂的情況,有的廠家為了克服這種狀態在機床設計中加有機械、電氣、液壓測量等系統組成的曲軸防下垂吊系統。圖3、圖4所示就是該裝置的外形,這個裝置在機床數控系統中設置為第三軸,它的防曲軸下垂吊力由液壓比例閥控制,保持和頭尾座旋轉角度的同步。
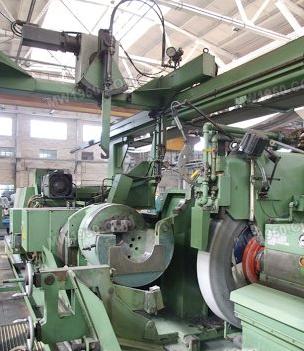
圖三
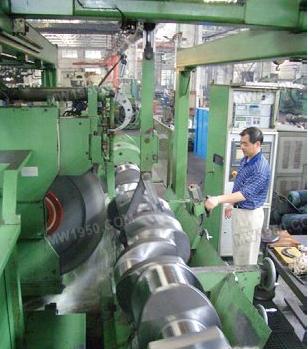
圖四
隨著數控技術的發展,機床功能部件水平的提高,目前國外已經發展出一種隨動磨削曲軸的新設備新工藝,它只要在同一臺機床上通過一次夾裝就可以同時磨削加工曲軸主軸頸和連桿頸,而不需要再用兩臺設備依次分別對曲軸主軸頸和連桿頸進行磨削。
圖5是該設備基本結構和加工工藝布置的示意圖。該設備在電氣系統上設計成全數控控制、全閉環反饋測量的控制模式,在機械設計上打破傳統磨床的結構分布,把原來頭尾座和工件Z 軸移動更改為砂輪架移動而頭尾座及工件固定不動,因而床身長度就可以設計較短。由于采用了X 軸橫向滑臺原理,這樣就可以克服和消除因工件移動而造成的機床變形等諸多因素,并且還增強了機床的剛性。固定工件的工作臺臺面設計成向砂輪架方向傾斜 20°,以便于冷卻液方便排泄帶走大量的磨削顆粒,保證了機床的熱穩定性和工件因工作臺傾斜 20°的設計而使頭尾座能在固定工件的工作臺臺面上安全夾緊。因設計結構的不同,從而磨削方法也不同于一般的傳統曲軸磨床,它的主軸頸磨削采用切入式磨削法,連桿頸的磨削是采用切入式隨動磨削法。圖6、圖7是隨動磨削法的曲軸與砂輪運動的軌跡示意圖。
隨動磨削法的公式:
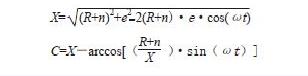
式中 X --砂輪架橫向滑臺移動軸;C--頭尾座工件夾持旋轉軸。
采用隨動磨削法是比較先進的加工方法,但是它對設備有更高的要求,特別是對硬件和軟件相互之間的關系更為密切配合。隨動磨削法實際上是涉及到曲軸旋轉位置與砂輪架直線運動二者之間的相互關系,它的關鍵在于:
(1)C 1、C 2和X 1必須保持同步。就是頭座C 1和尾座C 2夾持曲軸二端頭,偏心于主軸頸的連桿頸中心線,圍繞C 1、C 2旋轉軸線的運動軌跡,與X 1軸砂輪架橫向滑臺直線移動的前后運動的距離關系,始終要使連桿頸的外徑在360°的任何角度上要與砂輪的外圓保持相切位置。
(2)機械傳動鏈的精度、光柵反饋系統的精度、在線測量系統的精度。
(3)開發的隨動磨削應用軟件合理和實用性等。
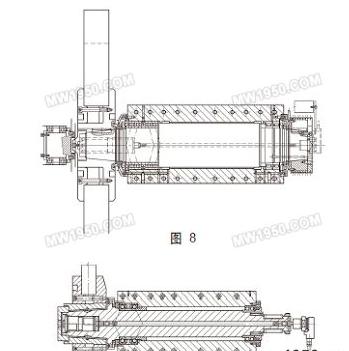
以上問題將直接影響到磨削加工的精度,為此,機床廠家在X 砂輪架橫向滑臺移動軸上,設計成剛性好、吸振性好、精度高的靜壓閉式導軌系統。X 軸驅動采用定位重復性好和傳動間隙小的非機械傳動的直線電動機消除間隙方法。X 軸定位用直線光柵尺進行精確。
頭座C 1和尾座C 2采用水冷扭矩電動機直接驅動工件,高分辨率圓光柵消除機械傳動的間隙,防止在磨削時的頭尾座在旋轉時有上下死點的出現,并保持同步和恒線速度磨削。采取這些措施從而在理論上可以保證磨削連桿頸的圓度達到0.005mm和表面粗糙度的要求。同時為了提高砂輪主軸轉速來提升砂輪線速度,普通砂輪磨削圓周(線)速度可達45m/s,電動機主軸驅動功率達到78kW,對砂輪主軸箱的結構也進行了優化,如圖8、圖9所示。把原先的圓桶形軸瓦支撐更改為高精度的無需保養的陶瓷球軸承結構。為了提高砂輪主軸的精度還配制了帶砂輪自動平衡系統(意大利MARPOSS制造),與砂輪主軸為一體,并帶有超聲波間隙控制系統(噪聲控制)作為防止砂輪碰撞工件的保護裝置。為了使工件在機床上加工找正方便,還設計有曲軸防下垂補償功能,曲軸的下垂可通過一個安裝在砂輪頭架上預先設定中心的測量頭系統,來檢測曲軸的實際位置,與原設定中心進行比較后,通過數控系統對數控中心架進行控制補償。如圖10所示。
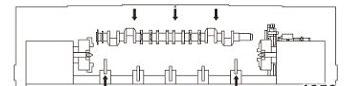
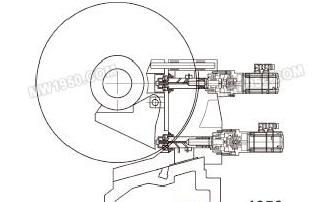
為了提高砂輪主軸的精度還配制了帶砂輪自動平衡按每個操作命令實現往復運動,以測量垂直面中心高。對每個加工后的曲軸頸外圓進行多次測量,直至采用了足夠數量的中心架,如圖11所示。在全自動磨削時保證曲軸頸直徑的一致,還配制在線直徑測量頭,裝在砂輪頭座上,可自動擺入和擺出。測量頭始終跟隨連桿軸頸作回轉運動并具備自動圓度檢測,該裝置能夠識別和顯示采用切入式方法的圓度偏差,將橢圓度與圓度測量機床的測量結果進行比較,并直接對機床控制進行數據修正,并以人機友好的方式運行,能快速給出與圓度有關的機床參數的最佳值。在生產過程中可以對圓度進行常規檢測,可以節省測量的時間。全部功能和顯示都集成在機床的控制系統中。
在目前國內的磨床制造廠家中,還沒能真正生產出大型的采用隨動磨削結構的設備,以及大型曲軸進行隨動磨削的工藝技術。這有待于我們工作在設備系統的全體科研人員共同努力,不斷地對數控系統軟件的開發、機床功能配套部件的研發升級。只有整體制造水平的提高,設備制造理念的更新,才能與國外僅有的幾家生產隨動磨削設備的廠家競爭叫板。
投稿箱:
如果您有機床行業、企業相關新聞稿件發表,或進行資訊合作,歡迎聯系本網編輯部, 郵箱:skjcsc@vip.sina.com
如果您有機床行業、企業相關新聞稿件發表,或進行資訊合作,歡迎聯系本網編輯部, 郵箱:skjcsc@vip.sina.com