立式車床的數控系統配置與選型
2017-12-20 來源: 西南林業大學機械與交通學院 作者:易 偉, 楊 潔
摘 要: 以西門子 808D 系統在立式車床的應用為例,從軟硬件兩個方面闡述了立式車床傳動的功能布局及控制系統的作用,并對系統配置選型時所采用的計算方法及相關步驟進行了闡述。
關鍵詞: 立式車床; 數控系統; 配置; 選型
隨著我國汽車、高鐵、電機等行業的發展,汽車輪轂、電機殼等中大型盤類零件的需求越來越多,在傳統加工中一般使用中大型的臥式車床,其缺陷是裝夾工件不便,精度及加工效率低。
因此許多機床生產企業為順應市場的需求,設計制造了多種立式加工設備,極大地減少了裝夾時間,提高了加工精度和生產效率。
數控立式車床在保留原有普通立式車床大部分主體結構的前提下取消了進給系統,將原進給傳動系統改為使用伺服電機直接連接滾珠絲杠帶動車床本體運動; 保持原有的底座變速箱結構不變,將主電機由普通電機改為伺服主軸電機,同時在主軸底部安裝有編碼器,以實現無級變速和螺紋切削功能; 重新設計了滑動本體結構,在本體上安裝多工位電動刀臺,從而可實現根據數控程序自動換刀等功能1]。
本文以 CKS5160 數控立式車床為例對機床電機的選型及數控系統的基本功能進行闡述。該設備通過控制伺服主軸電機來實現工作臺的無級調速,控制 X、Z 軸的交流伺服電機實現刀具的進給,同時針對工藝要求,調用 PLC 子程序實現對電動刀臺、液壓系統的控制,粗、精加工可自動換刀并自動調整夾具的液壓夾緊力。機床外形結構如圖 1 所示。
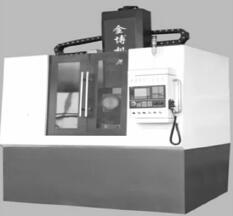
圖 1 機床外形結構
1 、控制系統構成
機床控制系統可控制和保證機械系統的良好運轉,確保設備的精度。因此控制系統、電氣元器件等必須以機械系統結構為依托進行選擇。
1. 1 傳動系統部件選型
機床傳動系統簡圖如圖 2 所示。
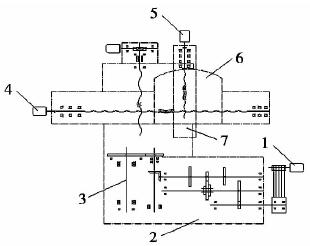
圖 2 機床傳動系統簡圖
1. 主電機; 2. 底座主軸變速箱; 3. 主軸; 4. X 軸電機;5. Z 軸電機; 6. 車床本體; 7. 滑枕
立式車床主要包括底座、橫梁、立柱、滑枕、滑動本體、升降箱體等部件,傳動控制系統分為底座主傳動系統、X 軸進給系統、Z 軸進給系統三部分。
1. 1. 1 主電機類型選擇
數控立式車床主傳動系統由電機通過底座齒輪箱帶動主軸旋轉。為了保證加工過程中工件質量的一致性,需要保證恒線速度切削加工,即必須保證數控系統能夠對電機進行無級調速; 同時為了保證車床有車削螺紋的功能,需要通過系統來協調工作臺轉速與螺紋車刀之間的進給關系,因此在主軸底部安裝有光電式脈沖編碼器,通過編碼器將主軸角位移信號傳遞給數控系統,數控系統對信號進行處理后,再將信號傳送到進給電機,從而實現協調主軸轉速與進給量的目的[2]
。
為實現主軸的無級變速,有以下兩種方案可供選擇:
1) 主電機采用變頻調速電機,通過變頻器控制主軸電機的轉速變化,從而實現主軸的無級變速;
( 2) 主電機采用伺服主軸電機,通過伺服驅動系統來控制主電機的旋轉速度。
變頻調速電機價格低廉,易于安裝,但由于調速電機的結構特性,當電機調頻在基率以下時功率會急劇減小,因此一般只適用于較高轉速的加工情況,而伺服主軸電機則可以保證在較低轉速時依然有較高的輸出扭矩。
本文討論的 CKS5160 立式車床,工作速度一般為 50 ~ 100 r/min,而且切削量較大,變頻調速電機不能保證這種轉速的扭矩需求,因此主傳動系統中電機選用伺服主軸電機,然后通過底座變速箱放大扭矩實現低速高扭矩輸出。
1. 1. 2 主電機參數選擇
功率和扭矩是電機的基本參數。首先根據待加工的零件材料類型、切削深度、切削速度及進給量等相關參數計算切削力,然后根據機床最大的加工直徑計算出切削扭矩,繼而得出機床的主傳動功率。然后根據計算出的扭矩、功率、主軸工作轉速,以及底座變速箱的齒數比來選擇電機[3]。切削力及切削功率的計算公式如下:

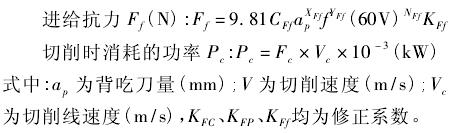
車削時切削力及功率公式中的系數和指數見表1,這些參數是在一定的試驗條件下得出的,若計算的實際條件與試驗條件不符,則還需要分別乘以相應的修正系數[4]。
表 1 車削時切削力及功率公式中的系數和指數
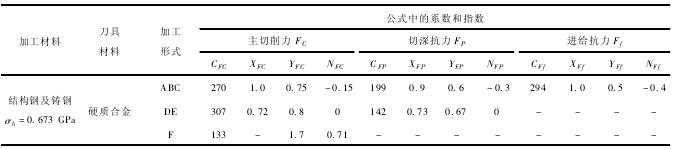
1. 1. 3 主軸脈沖編碼器選擇
采用脈沖編碼器主要是為了實現切削螺紋功能,因此必須按照主軸的最高轉速來選擇。選擇時在滿足功能要求的基礎上還要盡量考慮到經濟實用。本文選擇的是長春博辰光電技術有限公司生產的 BC38S 系列增量式脈沖光電編碼器。
1. 2 橫向進給傳動系統
1. 2. 1 相關參數計算
立式車床橫向進給系統如圖 3 所示。
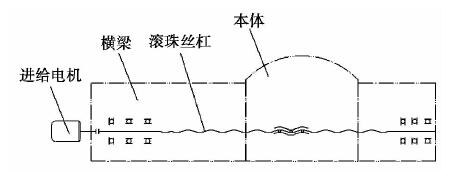
圖 3 立式車床橫向進給系統示意圖
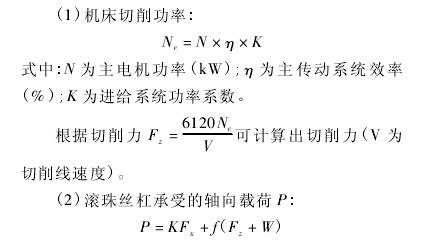

根據具體切削時的切削速度、進給量、工件最大直徑可計算出滾珠絲杠的轉速、絲杠壽命及最大動載荷[5],根據最大動載荷可查閱相關滾珠絲杠的選型樣本進行選擇,然后再根據絲杠副的傳動效率進行剛度及穩定性校核。
1. 2. 2 電機選擇
確定滾珠絲杠后,可根據車床本體、絲杠轉動慣量、切削速度、絲杠尺寸參數來計算電機所需扭矩,從而選擇電機[6]
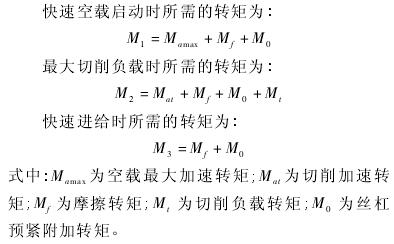
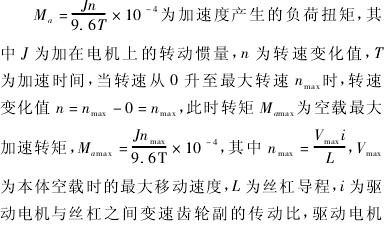
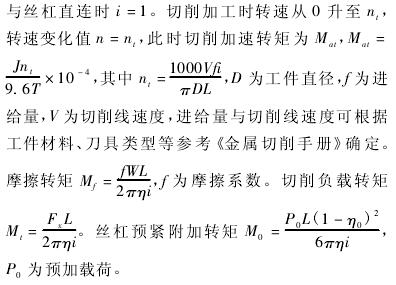
根據以上各式可計算出所需轉矩,計算出相關參數后即可確定電機類型。
1. 3 縱向進給傳動系統
縱向進給傳動系統設計與橫向進給傳動系統相似,電機通過聯軸器帶動滾珠絲桿移動,從而實現刀架在垂直方向上的上下運動。所不同的是由于是在垂直方向上運動,為了防止忽然斷電、掉刀或其他特殊情況發生時出現事故,縱向電機需要帶抱閘功能。
1. 4 數控系統
至此,數控系統基本部件的選擇已經完成。根據工件的材料、切削速度、切削量等因素,確定切削力、最大扭矩,再由切削力確定主電機的功率,并選擇與主電機相關的元器件; 然后根據進給速度、切削力的大小確定滾珠絲杠并進行校驗; 選定滾珠絲桿后,根據整體的轉動慣量、進給速度及使用壽命等進一步確定電機的相關參數,最后確定進給電機的型號。
由于數控立式車床加工的零部件一般精度要求較低,因此控制系統大多選用開環控制。數控系統需要能夠控制三個軸,其中包括兩個進給軸和一個主軸,同時伺服的功率范圍應適合于已經確定的電機,并且系統要運行速度快、安裝方便、性能穩定、價位合理,很多機械設備廠家都選擇西門子 808D 車削系統作為立式車床的數控系統。
2 、控制系統功能
808D 車削控制系統主要控制主軸轉速系統、X軸進給系統、Z 軸進給系統,根據西門子 808D 調試手冊,數控系統配置如圖 4 所示
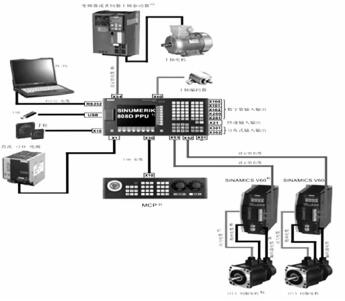
圖 4 數控系統配置
2. 1 主軸控制系統
立式車床主軸帶動工作臺旋轉,工作臺上安裝四爪卡盤或專用夾具固定工件,通過車刀的水平、垂直進給來完成對零件的切削。為了實現車削螺紋功能,需準確傳輸主軸的角位移信號,同時還要保證編碼器的運行平穩,因此將編碼器與主軸通過小型聯軸器同軸安裝。
根據控制主軸旋轉方向的不同方式,可以分為單極性主軸和雙極性主軸兩類,下面以單極性主軸為例,說明其主要連接方式[7]。X54 為主軸模擬量接口,AO 和 AGND 引腳輸出0 ~ 10V 模擬量電壓信號來控制主軸的轉速。快速輸入/輸出接口 X21 的信號用于控制正反轉向,接口X60 用于接收主軸編碼器的信號,從而協調主軸轉速和 X 軸、Z 軸進給量,實現螺紋加工。
主軸編碼器接口先連接主軸伺服驅動器后再連接面板 X60[8],如圖 5 所示,雙極性主軸連接方式在調試手冊中有詳細說明。
2. 2 進給系統
立式車床控制的電機除主軸電機外,還包括另外兩個進給電機。進給系統包括 X 軸進給及 Z 軸進給,在面板控制單元中,X51、X52、X53 接口是脈沖驅動接口,用于連接到進給電機伺服驅動器。其他如X10 為手輪輸入,X54 為模擬量主軸接口,X2 為RS232 接口,X30 用于連接 MCP 的 USB 接口,X1 為電源接口等。面板控制單元接口布局( 后視圖) 如圖6 所示,接口見表 2。
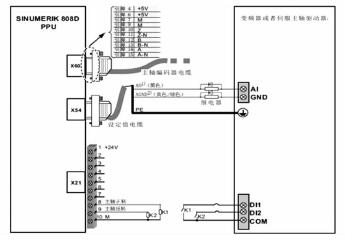
圖 5 單極性主軸連接示意圖
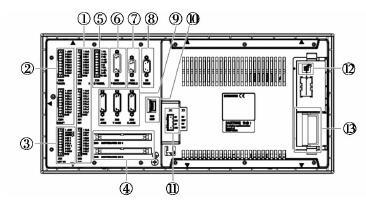
圖 6 面板控制單元接口布局( 后視圖)
表 2 面板控制單元( PPU) 接口
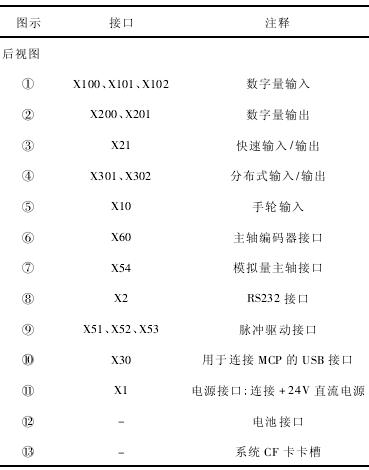
2. 3 其他
其余如冷卻、刀架等相關輔助功能都是標準連接,在調試手冊中有詳細講解。需要注意的是: 西門子數控系統在出廠時都配置有相應的樣例 PLC 程序[9 - 11],相應的 PLC 輸入輸出點已經定義完成,設計控制線路時需要據此連接才能保證軟硬件的配合。其他如電源、變壓器、必要的繼電器連接等,大多在單獨的電器柜中。
3 、結束語
隨著企業對零件加工精度和生產效率要求的日益提高,在汽車輪轂、電機殼、鑄件粗精加工等行業,數控立式車床比臥式的設備更加適合于流水線作業,同時還具有成本低、效率高、裝夾方便等特點,目前許多企業如江西特種電機股份有限公司、湖南天能電機制造有限公司等企業都已逐步采用數控立式車床來替代原有的加工設備,并取得了良好的生產效益。國內外數控系統在基本的功能和運用上沒有太大的區別,由于立式車床多用于粗加工,一般所處生產環境比較惡劣,機床對系統的抗干擾性和穩定性要求比較高。
在同等價位的前提下,西門子系統的穩定性和抗干擾性有明顯優勢,加之模塊化設計及強大的擴展功能,使得西門子系統在許多經濟型數控設備中被廣泛使用。
投稿箱:
如果您有機床行業、企業相關新聞稿件發表,或進行資訊合作,歡迎聯系本網編輯部, 郵箱:skjcsc@vip.sina.com
如果您有機床行業、企業相關新聞稿件發表,或進行資訊合作,歡迎聯系本網編輯部, 郵箱:skjcsc@vip.sina.com
更多相關信息