淺談加工中心的刀具選擇與應用
2017-1-11 來源:中冶陜壓重工設備有限公司 作者:王省平
摘 要:推廣加工中心是提高制造業精密加工水平的前提,刀具的正確選擇與應用是提升加工中心加工精度的保證。具體而言,刀具的正確選用,進刀速度的準確掌握、吃刀量的精確把控等問題,都是需要注意的。
關鍵詞:加工中心;刀具;選擇;應用
一、引言
實現智能制造、推廣加工中心,強化精密加工,滿足社會各個部門對產品加工精度和表面質量日益提高的要求,是制造業實現奔跑跨越的技術基礎。在實際生產中,加工中心刀具的選擇與應用,是實現上述目標的根基。
加工中心的特點主要是銑削加工,利用銑刀的多刃齒數,通過階梯銑削或高速銑削方式,在持續切削的過程中實現對材料的加工。在切削過程中,不可避免地會產生沖擊、振動,同時伴生大量熱能。當切削振動與機床固有頻率一致時,會引發共振現象,容易造成刀具崩刃、機床零件損壞等不良后果。如果選擇刀具齒數不合適,周期性熱變形會令刀具的切削刃出現熱疲勞裂紋,容易誘發刀齒剝落或崩刃,產生廢品。
按照國家制造業刀具標準,加工中心的刀具尺寸具備通用化、標準化、系列化的特點,切削參數滿足規范化、匹配化、典型化的特點。
按照刀具結構,可分為:整體式、減振式、鑲嵌式、內冷式、特殊形式等。
按加工工藝,可分為:車削、鉆削、鏜削、銑削等刀具。
按刀具材料,可分為:金剛石、硬質合金、陶瓷、氮化硼、高速鋼等刀具。
二、刀具的選擇
1、選擇刀具的原則
加工中心編程與操作人員在選擇刀具的時候,應該綜合考慮工件材料、外觀形狀、表面光潔度要求、熱處理要求、加工工藝、切削量大小、加工余量等因素,選擇剛性好、與加工材料匹配、耐用度高的刀具,根據加工工藝要求,選擇機夾或可轉位式刀具。
2、選用刀具的種類
在遵循以上原則的前提下,刀具的選用主要是要根據加工材料的外觀形狀而定。例如:①加工曲面材料時,采用球頭刀,在第一遍粗加工的時候,使用兩刃刀具,快速切削;在后期的半精加工、精加工的時候,使用四刃刀具,以提高表面光潔度。②在加工較大面積平面時,可以使用鑲嵌式盤形銑刀,以提高生產效率。③在加工小平面或臺階面時,使用通用立式銑刀。④加工鍵槽時,使用兩刃鍵槽銑刀,可以有效保證鍵槽成品精度。⑤加工圓孔的時候,對于精度不高的可以使用鉆頭,對于精度較高的,先使用鉆頭成孔,預留足夠的加工余量,再換用鏜刀做精密加工。
3、選用刀具的材料
不同材料的刀具都有各自的適用范圍,并不是選擇材料貴的就是對的。只有按照加工材料和加工環境的要求配比合適的刀具,才能達到“工欲善其事必先利其器”的效果。金剛石刀具不耐高溫,切削溫度一旦超過800℃,其硬度幾乎完全喪失。在幾百度的溫度下,金剛石的碳原子極易與鋼鐵材料發生化學反應,導致刀具損傷。因此,金剛石刀具只適合在低溫環境下加工非金屬材料、有色金屬及其合金。PCBN 刀具專門適用于硬度達到45HRC 的耐磨鑄鐵與淬硬鋼、35HRC 以上的耐熱合金、30HRC 以下的珠光體灰口鑄鐵。硬質合金刀具的適用面比較大,多用于各種鑄鐵或鋼材、有色金屬、非金屬材料、耐熱合金等材料的切削。陶瓷刀具的工作狀態是干切削,適用于高速切削鑄鐵、硬質合金刀具難以加工的鋼材等難加工材料。
高速鋼刀具在韌性與強度方面的綜合性能比較好,高速鋼刀具在刃形復雜的刀具多采用高速鋼,目前,孔加工刀、螺紋刀、拉刀、切齒刀幾乎全部是高速鋼材料。高速鋼一般分作:通用型高速鋼(W18Cr4V、W6Mo5Cr4V2)、高碳高速鋼(95W18Cr4v)、高釩高速鋼(W12Cr4V4Mo)、鈷高速鋼(W2Mo9Cr4VCo8M42)、鋁高速鋼(W6Mo5Cr4V2AL501)。
三、刀具的應用
1、切削量的應用原則
切削用量的應用原則:保證加工精度和表面光潔度的達標,發揮刀具正常的切削性能,保證刀具的合理耐用度,充分發揮加工中心的性能,最大限度地提高勞動效能,提升勞動生產率,降低勞動成本。為了實現這一原則,就要把握好刀具的切削速度、背吃刀量(側吃刀量)等因素。
2、切削速度的掌握
切削速度與與刀具直徑d 成正比,與刀具的每齒進給量(fz)、背吃刀量(ap)、銑刀齒數(Z)、耐用度T 成反比。隨著刀具工作齒數的增加,刀刃負荷必然增加,切削產生的熱量隨之增大,刀具的磨損程度必然也會增加。因此,改善刀具散熱條件可以有效提高切削速度。在生產中,在其它條件相同的情況下,為了提高切削速度,多采用更換大直徑刀具的方法來改善散熱條件。下面以高速鋼刀具和硬質合金刀具為例,說明刀具的切削速度參考值。
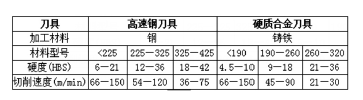
3、背吃刀量的掌握
在保證加工質量的前提下,根據加工中心、刀具、加工工件等條件共同決定背吃刀量(ap)。為了減少走刀次數,避免操作失誤數量,原則上盡可能地讓背吃刀量等于或鄰近加工工件額定的加工余量。舉例說明:假設加工工件的表面光潔度要求為Ra3.2—12.5μm。可以按照先粗銑、后半精銑的步驟進行,在粗銑后預留半精銑余量0.5—1.0mm 即可。假設加工工件的表面光潔度要求為Ra0.8—3.2μm。可按照粗銑、半精銑、精銑三個步驟進行加工,在半精銑時,端銑背吃刀量取1.5—2mm,在精銑時,端銑背吃刀量取0.5—1mm。
四、結論
綜上所述,加工中心刀具的選擇與應用,必須結合機床性能、工件材料、加工形狀、刀具特性等因素綜合考慮,同時在應用中務必注意切削速度和吃刀量,才能保有效提高加工精度。
投稿箱:
如果您有機床行業、企業相關新聞稿件發表,或進行資訊合作,歡迎聯系本網編輯部, 郵箱:skjcsc@vip.sina.com
如果您有機床行業、企業相關新聞稿件發表,或進行資訊合作,歡迎聯系本網編輯部, 郵箱:skjcsc@vip.sina.com
更多相關信息