微銑削中考慮刀具跳動的瞬時切厚解析計算方法
2017-2-20 來源:上海交通大學機器人研究所 作者:聶強 黃凱 畢慶貞 朱利民
摘要:通過研究刀具實際切削過程中的余擺線軌跡及其影響,提出一種新的瞬時切厚解析計算方法,并針對兩齒、四齒的情況給出瞬時切厚的具體計算公式。在兩齒和四齒銑槽工況下,分析刀具跳動量和跳動角度對各齒切削過程的影響。該方法考慮刀具的綜合徑向跳動(包括主軸跳動,刀具制造安裝誤差等綜合形成的徑向跳動值),適用于微銑削中任意齒數刀具瞬時切厚的計算。通過與宏觀銑削中的傳統切厚計算公式、BAO 模型和Newton-Raphson 等數值法對比,量化指出了微細銑削加工與傳統宏觀銑削加工的一些不同,同時驗證了提出的方法具有計算簡潔、精度高和通用性強的優勢。基于該模型進行了微銑削銑槽試驗中切削力的預測,預測結果和試驗結果相符良好,驗證了模型的正確性和實用意義。
關鍵詞:微銑削;加工機理;刀具跳動;刀具軌跡;瞬時切厚
0.前言
隨著產品小型化需求的不斷增長,微細加工機床被廣泛用于醫藥、生物、航空航天、電子、通信等領域微小零件的加工。相比于傳統機床或超精密機床,微細機床具有體積小、能耗低等優點。同時,微細切削加工技術成本低、效率高,可加工復雜的三維形貌特征,精度高,適用于各種材料的工件[1]。然而,微細銑削加工并不只是傳統加工在尺寸上的微縮,它具有很多不同于傳統切削加工的特征[2]。
首先是尺度效應[3]。在宏觀切削加工中,刀具被認為是絕對鋒利的。然而在微細加工領域,切削進給量與刀具切削刃的圓角半徑相當,因而不再能忽略刀具切削刃的鈍圓現象,并由此產生犁切現象和最小切屑厚度現象[1-4]。其次刀具跳動對切削過程影響顯著。刀具跳動是制約微細切削加工質量的主要因素[5]。在微細切削中,由于刀具跳動量與每齒進給量相當,給切削過程帶來嚴重的不穩定性,甚至導致某個齒空切。尤其對于二齒刀具,容易形成單齒切削現象。
因此能否在考慮刀具跳動的情況下,準確計算瞬時切厚,直接關系著切削力建模的準確性和可靠性,進而影響微細切削加工的質量控制。目前,微銑削中計算瞬時切厚的方法大致可以分為三類:不考慮刀具跳動的方法,考慮刀具跳動的數值法和考慮刀具跳動的解析法。不考慮刀具跳動的方法已經比較成熟,各類模型也比較多[6-8]。MARTELLOTTI[9]在20 世紀40 年代通過研究宏觀銑削中刀具的軌跡及切厚,建立了宏觀銑削切厚計算模型。2000 年BAO 等[6]從刀具的實際運動軌跡出發,給出了基于余偏擺線軌跡的切厚計算公式和切入角計算公式。2001 年LI 等[8]通過近似求解超越方程,得到不考慮刀具跳動的瞬時切厚計算公式,但由于公式本身的復雜性,難以在實際建模中使用。2013 年,KANG 等[10]建立用傅里葉多項式逼近的瞬時切厚計算公式,并與BAO和LI 的公式進行了計算結果的比較,比較結果表明其公式在計算上與LI 公式較為一致。
LI 等[11-12]采用Newton-Raphson 數值解法計算跳動下的瞬時切厚,但數值解法不利于建立解析形式的切削力模型。在考慮刀具跳動的解析法[7,13-14]中,BAO 等[7]給出了二齒情況下考慮刀具跳動的瞬時切厚計算公式。然而他們雖對四齒情況有作刀具跳動角度與切削力關系的分析,但沒有給出四齒刀具考慮跳動下的具體的切厚計算公式。WAN 等[14]根據3 個不同刀具跳動模型的比較結果,推薦在切削力建模中使用徑向跳動模型,并給出其切厚為宏觀非跳動狀態下的切厚值加上由跳動導致的相鄰兩齒實際半徑差量值。該方法本質上依舊采用宏觀上近似圓弧切削軌跡的簡化思想。
本文目的在于通過分析銑削過程中刀具的實際切削軌跡,給出一個考慮刀具跳動的,能夠適應于不同齒數的、解析的瞬時切厚計算公式。文章首先在考慮刀具徑向綜合跳動的情況下,建立了通用的切厚計算方法。隨后針對刀具齒數N=2 和N=4等常見的情況,給出了具體的切厚計算公式,然后進一步分析了刀具跳動角度對各刀齒加工過程的影響,同時將新方法分別在對應齒數條件下與現有各方法進行對比,總結出新方法的優勢。最后基于新切厚計算方法進行微銑削過程中切削力的預測試驗,驗證了新方法的實用性。
1.考慮刀具綜合跳動的瞬時切厚建模
1.1 微銑削中刀具的實際軌跡
刀尖點的實際運動軌跡如圖1 所示,呈余擺線狀,灰色部分代表兩條相鄰軌跡所形成的切削厚度。
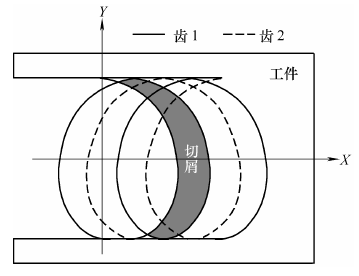
圖1 兩齒刀具切削時刀齒的真實軌跡
刀具切削刃的刃尖點,不考慮刀具跳動的情況下,其在笛卡兒坐標系XOY 中的位置可用如下方程表示[8]
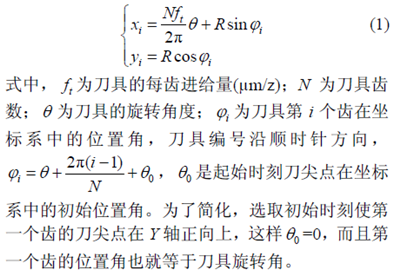
考慮跳動情況下,刀具第i 個齒刀尖點在XOY坐標系中的方程為
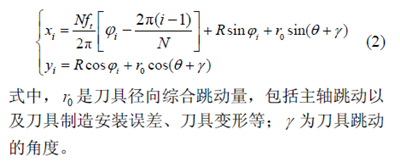
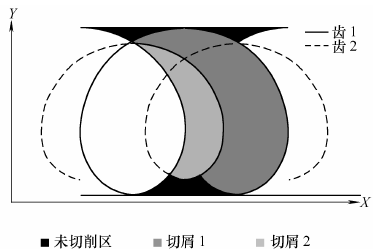
圖2 考慮跳動下的兩刃刀具各齒的切削軌跡及相應切厚示意圖
從圖2 可以看到,刀具徑向跳動導致切屑1、2的厚度不同,刀齒1、2 每次參與切削的時間也不同。槽壁的實際加工輪廓(圖2 中的黑色部分)要比沒有跳動情況下的加工輪廓粗糙。刀具跳動易造成實際微細銑削過程的不穩定,降低加工質量。
1.2 考慮刀具跳動的瞬時切厚通用模型
下面將根據刀具的實際切削軌跡,利用參量間的幾何關系,建立考慮刀具跳動的新切厚計算模型。
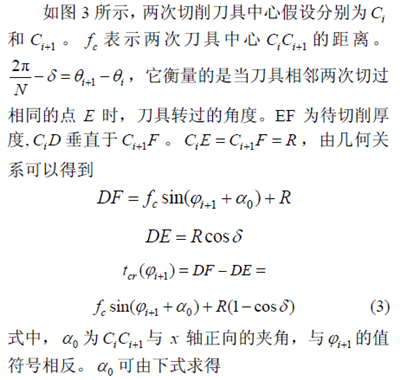
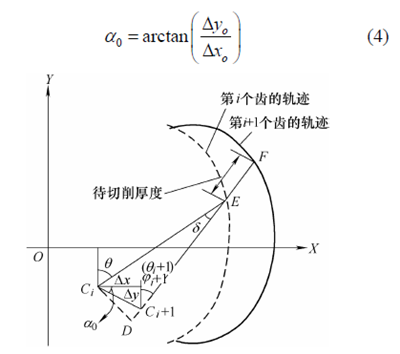
圖3 槽銑中考慮跳動下的刀刃軌跡及瞬時切厚
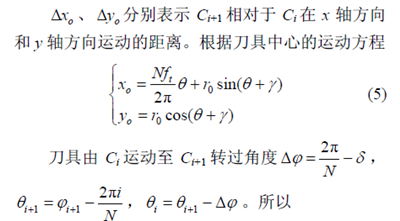
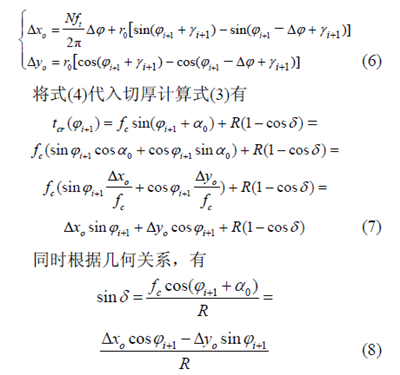
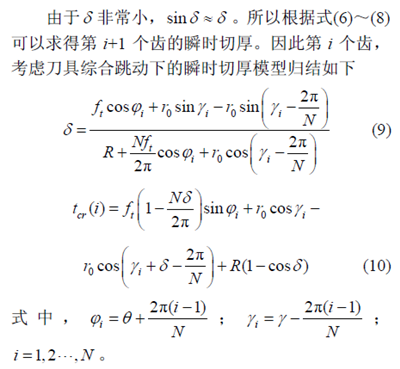
當發生空切時,有的切屑厚度并非由相鄰兩個齒的軌跡形成,如圖4 所示。刀齒2 發生空切,刀齒1 的切厚應由刀齒3 軌跡和刀齒1 軌跡形成。而模型中刀齒1 的切厚根據齒2 軌跡計算,需要進行修正。由于齒2 切厚根據上述模型的計算值為負值,所以齒1 的切厚修正只需要將齒1 的切厚計算值加上齒2 的切厚計算值,即

若修正后,齒1 的最大切厚值也為負,則說明齒1 也發生空切現象,需要對齒1 的下一齒的切厚進行同樣的修正。因此若i 齒發生空切,則需要對i +1齒進行切厚修正,修正方法和空切判定法如前所述。
上述模型適用于任意齒數下的瞬時切厚計算,本文在第2、3 節將討論微銑削中最為常見的刀刃齒數為N=2 和N=4 的情況。
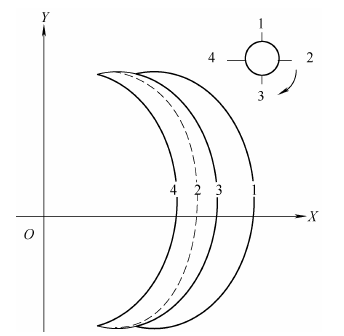
圖4 空切現象示意圖(刀具編號沿順時針方向)
1.3 新方法與傳統方法的比較
傳統銑削過程中,由于 ft / R 的值通常非常微小,可將刀齒的切削軌跡近似為圓周曲線。本文將這種源于傳統宏觀銑削,基于近似圓周切削軌跡的切厚計算方法暫稱為傳統計算方法[8],其切厚計算公式采用

不考慮刀具跳動的情況下,記ε 為新方法計算結果與傳統方法的計算結果的差值,用以衡量傳統方法的計算誤差。N=2 時,傳統方法切厚計算結果相對于新方法的相對誤差如圖5 所示。圖5 表明,隨著 ft / R 逐漸增大,傳統方法計算的待切削厚度誤差將變得越來越大,而且在刀具的切入和切出位置達到最大。假設刀具半徑為 1 mm,ft / R 的值為 0.1時,傳統法計算誤差最大達到6 μm 左右,這對微銑削過程中切削力的計算是影響非常大的。當 ft / R的值小于0.01 時,即傳統的宏觀加工工況下,新方法與傳統簡化法的計算結果則幾乎一致。
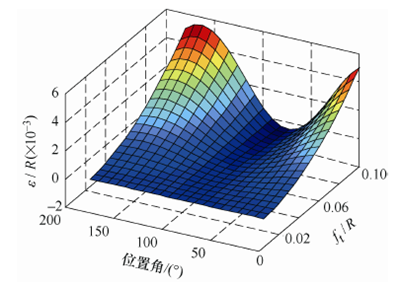
圖5 N=2 的情況下,傳統切厚公式的計算誤差隨 ft / R和θ 的變化規律
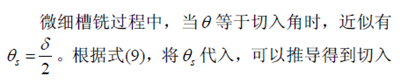
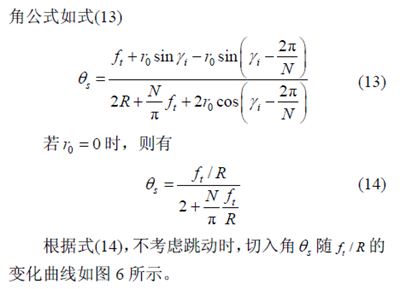
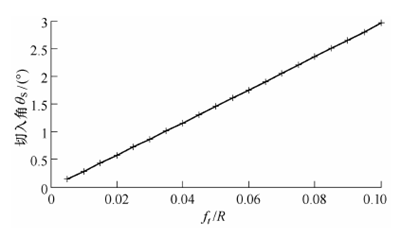
圖6 r0=0 時,切入角隨ft/R 的變化
隨切入切出角的變化,槽壁側表面加工輪廓的最大凸出高度可以通過式(15)進行計算

微銑槽后槽壁的表面輪廓高度正比于 ft / R 的平方。在刀具半徑為 1 mm的條件下,當 ft / R的值為0.1 時,表面輪廓高度約為1.2 μm,僅相當于一般條件下半精加工的粗糙度水平。因此可知新方法比傳統方法能夠更好地描述實際微銑加工狀況。
2.新方法下2 刃銑刀的切厚模型
2.1 N=2 時,具體切厚公式的導出及應用
當N=2 時,代入切厚計算公式(10),同時將
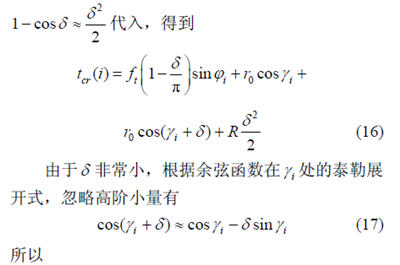
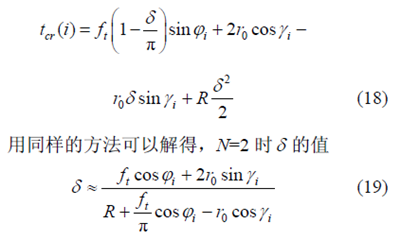
將式(19)代入式(18)便可以求得兩刃刀具切削過程中考慮跳動的瞬時切厚。
根據式(18)、(19),在不同的跳動角度下,兩刃銑刀在銑槽過程中的瞬時切厚變化規律如圖7 所示,其中,N=2,R=500 μm, r0=0.2 μm, ft=1 μm/z。
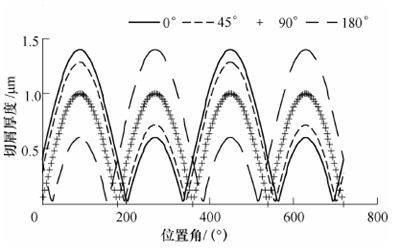
圖7 銑槽過程中不同的跳動角度下的瞬時切厚變化:
考慮刀具跳動時,從圖7 中可以看到,由于刀具跳動的存在,切厚以2π 為周期規律變化。當跳動角度為0°或者180°時,即刀具跳動方向平行于兩齒的連線時,對切厚的變化影響最大,最大切厚將減小2r0。當跳動角度為 90°時,對切厚無影響。根據式(18),若2r0 cosγ i > ft ,便會發生單齒切削的現象。
2.2 N=2 時,新方法與BAO 方法的比較
若不考慮刀具跳動,即r0 = 0,代入式(18)、(19)可得
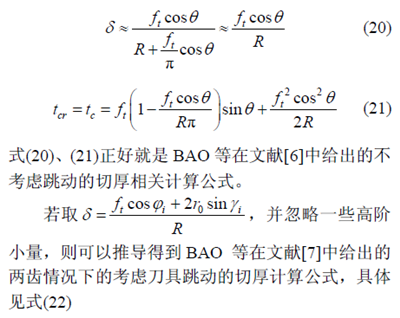
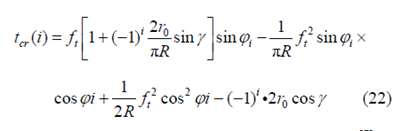
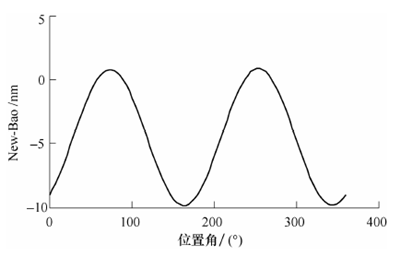
圖8 新方法與BAO 方法計算瞬時切厚的相對誤差
上述討論不僅說明了新模型的正確性,而且可以看到,新方法統一了考慮跳動和不考慮跳動的兩種情況下的切厚計算公式,也囊括了BAO 給出的考慮跳動情況下的切厚計算公式。并且式(18)、(19)在形式上的簡潔為編程計算提供了更佳的選擇。
3.新方法下4 刃銑刀的切厚模型
3.1 N=4 時,具體切厚計算公式的導出
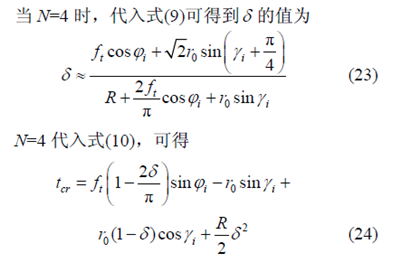
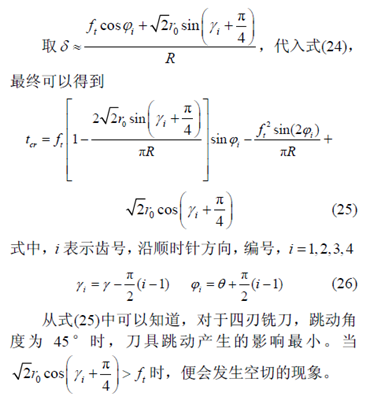
利用新模型,可以看到在不同的刀具跳動角度下,銑槽過程中四刃銑刀各齒的切厚變化如圖9 所示,其中,N=4,R=500 μm,r0=1 μm,ft =3 μm/z。
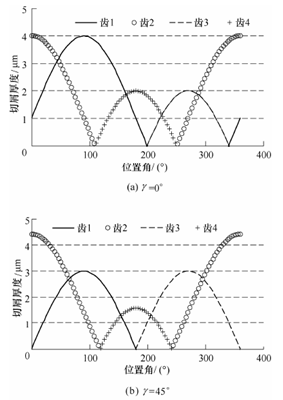
圖9 在不同跳動角度下,各齒的瞬時切厚
從以上各跳動角度下四刃銑刀各齒的切厚變化可以看到,在槽銑過程中較厚和較薄的兩個切屑總是相鄰的,如圖10 所示(在跳動角為0°的情況下,繪制各刀刃的實際軌跡及相應形成的切屑)。在跳動角度為45°的情況下,齒1、3 的切厚不受影響。所以為盡量減小跳動帶來的影響,將跳動方向調整至45°是一個較佳選擇。
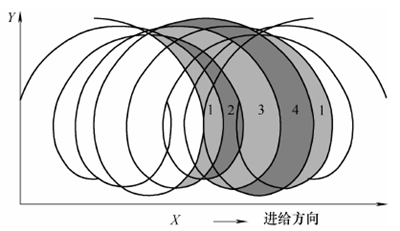
圖10 考慮跳動下四刃銑刀各齒的切厚示意圖
3.2 N=4 時,新方法、傳統修正法與數值法的比較在考慮跳動的情況下,WAN 等在文獻[14]中提到,徑向跳動模型中,刀具的實際切厚應由式(27)進行計算

式(27)是在傳統模型(式(12))的基礎上作了考慮刀具跳動的修正,因此將其稱作傳統修正法。為了體現不同方法間計算結果的區別,以Newton-Raphson數值法的計算結果為標準,將新方法與傳統修正方法分別減去數值法的計算值,所得結果作為解析法計算的相對誤差,在N=4 跳動角度為0°的情況下進行對比。如圖11 所示,其中,R=500 μm,r0=0.8μm,ft =2 μm/z。N-R 表示以New-Raphson 法為基準,新方法的計算精度明顯比傳統修正法要高,除個別位置角處,新方法與Newton-Raphson 法計算結果上幾乎完全一致,相對誤差率幾乎保持為零。傳統修正法由于沒有細致考慮切入切出點的情況,在切厚接近于零的切入切出點附近,其相對誤差率最大達到45%。而且隨著刀具跳動量的增大,這一誤差還會增大。新方法相比于數值法,則更簡單高效,有利于建立封閉的切削力模型。
最后將新方法與其他切厚計算方法比較總結如表1 所示。在非數值法中,新方法是現有考慮刀具跳動下精度最高的方法。
表1 新方法與現有各切厚計算方法的對比總結
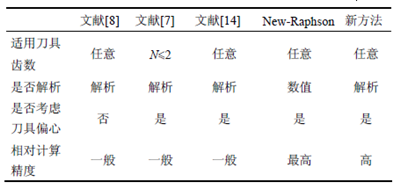
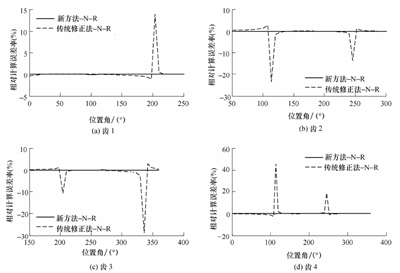
圖11 新方法,傳統修正法相對于數值法的計算誤差對比
4.新切厚模型的試驗驗證
銑削力的建模采用微元法,即沿著刀具軸向,將刀具分割成一層層的小片,每一片上某一特定齒的切削厚度和位置角看成是一致的。如圖12 所示,
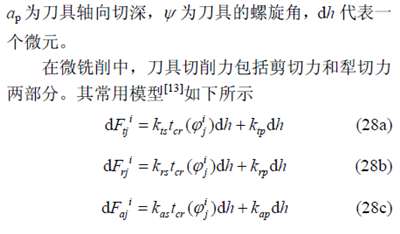
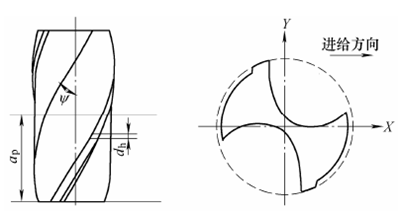

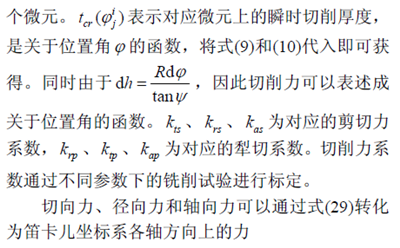
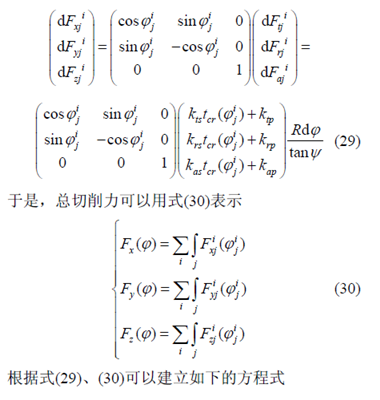
在文獻[13]中,切厚模型采用傳統不帶跳動的計算方法,本文將基于新切削厚度模型,進行切削力的預測。
本文用直徑為1 mm 的四刃硬質合金銑刀(中國臺灣SGO-S550),螺旋角為30°,進行微銑削槽銑試驗。工件材料為恒彈性合金3J53,其維氏硬度HV 為350~420,彈性模量為191~196 GPa。
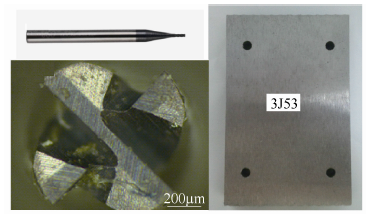
圖13 刀具和切削刃端面顯微照片(左)及工件(右)
測力系統采用Kistler9317B 三向壓電式測力儀以及配套的電荷放大器和數據采集系統。Kistler9317B 測力儀的靈敏度為0.01 N,X 和Y 方向量程600 N,Z 向量程2 000 N。采樣頻率為15 kHz。
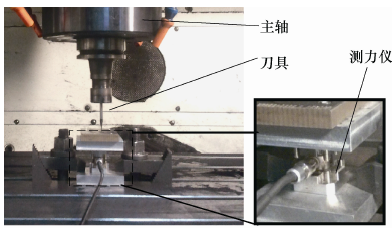
圖14 微銑削槽銑加工試驗
試驗切削條件為:刀具齒數N=4,刀具半徑R=500 μm,主軸轉速12 000 r/min,進給速度f=192mm/min,軸向切深ap=200 μm,X 方向為進給方向。刀具的跳動量在不同的轉速下測量[7],其值在1~2μm 內變化,因此取平均刀具跳動量r0=1.5 μm,刀具跳動角度γ=35°。分別使用傳統切厚模型和新的考慮跳動的切厚模型進行切削力的理論預測,效果如圖15、16 所示。
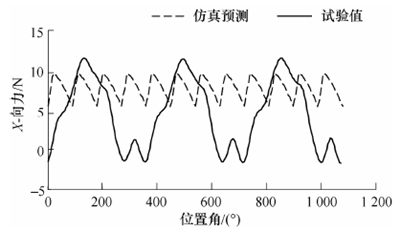
圖15 基于傳統切厚計算方法的切削力預測結果
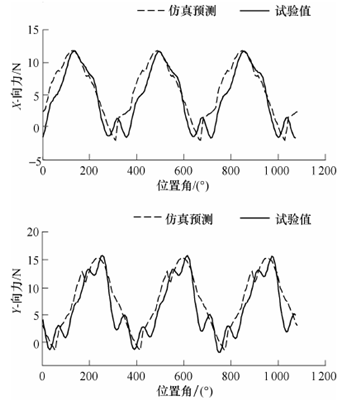
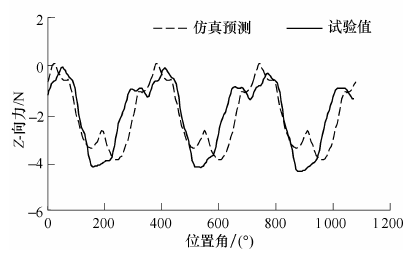
圖16 基于新切厚計算方法的切削力預測結果與試驗結果的對比
在不考慮刀具跳動的情況下, 4 刃銑刀的理論切削力周期應為90°。而且槽銑過程中,一般保持有2 個或者3 個齒同時參與切削,理論切削力不會為零。所以圖15 所示的預測結果是合理的,但與試驗結果不符。試驗中所測切削力的周期為360°,說明試驗中刀具跳動的影響是不可忽略的,傳統不考慮刀具跳動的切厚模型難以運用在實際切削力的預測中。
圖16 中切削力數據進行了低通濾波,濾波截止頻率為850 Hz,略大于主軸轉動頻率的4 倍。因此,試驗中所測切削力依舊保留著各齒切削的頻率成分,加上實際中振動等干擾的存在,體現在波形上就可能出現一些小波峰或者非平滑跳動,圖16中的Y 向力體現的特別明顯。預測曲線由于考慮了多齒同時參與切削的疊加效應,各齒的力相疊加后也可能出現相應的波峰或者非平滑跳動區。考慮刀具跳動的情況下,每個齒的實際切削厚度都不相同,每個齒的切削力變化過程也必然不同,多個齒同時參與切削的過程中,其合力的變化周期應為360°。圖16 中基于新切厚模型的切削力預測值與試驗值的周期均為360°,很好地體現了這一特征。在考慮跳動下,某些刀齒的實際切厚要大于不考慮跳動的情況,其切削力峰值必然要大于無跳動的情況,所以圖15 中出現預測值峰值小于實際試驗峰值的情況。因此,基于新瞬時切厚計算方法的常用切削力模型,其預測切削力能更好地符合試驗測量值。
5.結論
(1) 通過分析銑削過程中刀具的實際切削軌跡,建立了考慮刀具綜合徑向跳動下的適用于任意齒數刀具槽銑工況下的瞬時切厚計算模型,并給出了2 齒和4 齒情況下的具體計算公式。
(2) 分別討論了刀具跳動和跳動角度對微銑削中各齒加工的影響,得出N=2 和4 時,刀具跳動角度分別為90°和45°有利于減小刀具跳動的影響。在與傳統不考慮跳動計算方法的比較中,量化指出了刀具實際切入切出角的變化,以及銑削表面輪廓的改變,體現了微銑與傳統銑削的不同。
(3) 通過與已有各解析法的比較,新方法優勢不僅體現在適用于任意齒數下考慮刀具徑向跳動的切厚計算,而且其精度可以與數值法相比的同時,沒有計算上的穩定性問題,簡潔的形式為編程計算提供了較好的選擇。
(4) 在微銑削槽銑試驗中,將新方法應用于刀具實際銑削加工的切削力預測,預測結果與試驗結果相一致,體現了新方法的可靠性和實用性。目前在考慮跳動情況下的四齒銑削加工中,大多數都采用Newton-Raphson 等數值解法計算瞬時切厚。新方法的建立,有助于建立解析切削力模型,提升切削力模型的預測效果,從而有助于控制和優化微銑削加工工藝,提升產品的加工質量。
投稿箱:
如果您有機床行業、企業相關新聞稿件發表,或進行資訊合作,歡迎聯系本網編輯部, 郵箱:skjcsc@vip.sina.com
如果您有機床行業、企業相關新聞稿件發表,或進行資訊合作,歡迎聯系本網編輯部, 郵箱:skjcsc@vip.sina.com
更多相關信息