罩類零件的車削工藝研究
2018-11-16 來源:西安現代控制技術研究所 作者:劉強,孫韶渝,李威宇,郭志偉,康朝旭
摘 要:罩類零件是彈體結構的重要組成零件之一,生產工藝在罩類零件的質量保證方面具有決定性作用。各種工藝方法都有自己的優缺點和適用場合,其中適應性最強、使用頻率最高的便是罩類零件的車削工藝。針對罩類零件的車削工藝,通過大量工藝試驗積累的數據參數和技術經驗,在闡述了罩類零件薄壁的結構特點及各項嚴格的技術要求的基礎上,提出了包括沖壓模具設計、工裝設計、測量方法選用、刀具及切削參數選擇、工藝路線確定等在內的罩類零件的具體工藝方案,對指導相關產品生產具有一定的參考價值。
關鍵詞:罩類零件;刀具:模具
罩類零件在加工生產中具有精度要求高、易變形和工藝性差等特點,采用不同的加工方法對零件的質量、生產效率和成本具有明顯的影響。旋壓成型的方法,其設備造價頗高;鍛造成型法僅局限于零件的毛坯生產。
這些加工方法的后續工序仍需要進行車削加工。車削加工設備普遍應用于機械加工領域,其生產方便、成本低、加工適應性強,尤其在罩類零件的加工中,越來越體現出它的優勢。本文針對罩類零件特點進行車削工藝研究,所得到的技術成果可供同類零件加工參考。
1 、概述
1.1 罩類零件的結構特點
罩類零件是彈體結構的重要零件之一,其常見種類如圖1所示。
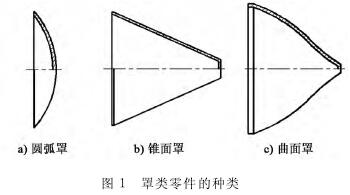
從罩類零件的結構特征來看,它們基本都屬于薄壁件,其加工部位主要是內外圓弧面、內外圓錐面、內外曲線面及大小端面等。
1.2 罩類零件的技術要求
罩類零件的內外型面與特殊部位接觸,通常對其尺寸精度要求較高(為IT5~IT8)。罩類零件的形狀精度主要是指圓度、圓柱度,一般應將其限制在尺寸公差范圍內。對精度要求高的零件,應在圖樣上標注其形狀公差。常見的位置精度是指對內外型面的壁厚差要求,即同軸度一般規定為 0.01~0.03 mm。另外,大小端面相對于軸線的垂直度一般規定為 0.01~0.05mm。根據不同的零件材料,相應的表面粗糙度為Ra0.8~Ra1.6μm。
1.3 、罩類零件的材料、毛坯及熱處理
此類零件根據不同工作條件和使用要求選用不同的材料和熱處理方式,以獲 得 相應的力學性能。常見的材料有銅、鉭、及鈦合金等。罩類零件最常用的毛坯是圓棒料、
鍛件、沖壓件和旋壓件。毛坯經過加熱鍛造后,能使金屬內部纖維組織沿表面均勻分布,可獲得較高的抗拉、抗彎及抗扭強度,同時能節約材料,減少機械加工余量。沖壓件一般有冷沖壓和熱沖壓,對于體積較大的罩體零件,采用熱沖壓時容易形成毛坯表面超硬層,如果鈦合金材料沖壓后的硬度>60 HRC,這將給加工帶來難度。
冷沖壓一般用于中小型圓弧罩體零件,通過專用模具將板材沖壓成待加工狀態,同樣節省材料,適用于大批量生產。將一定形狀的板材在旋壓機上加工形成的罩類旋壓件可以獲得很高的尺寸和幾何精度,后續只需進行工件長度方向上的加工即可。單件小批量的產品采用圓棒料加工比較經濟,留工藝臺后加工成形,可以節省模具費用。罩類零件有再結晶軟化退火、晶粒細化和低溫時效等熱處理要求,大多在毛坯鍛造和熱沖壓出廠時已經完成,本文不再討論和安排熱處理工序。
2 、罩類零件的工藝方案設計
2.1 冷沖壓模具的設計
采取冷沖壓的銅、鉭板類材 料,依 據 罩 體 零 件尺寸設計沖壓模具。本文介紹一種相對簡單實用的沖壓模具(見圖2)
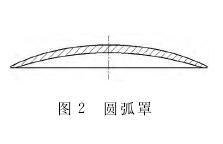
根據該零件的尺寸,選取板料厚度、毛坯尺寸, 形成毛坯加工圖(見圖3)

先確定 毛 坯 外 弧 面,一 般是外弧 面 對 應 外 弧 面,如果零件是變壁厚的就以小圓弧為基準往外留出加工余量,然后按板料厚度往下平移形成內弧面,內、外弧面應能包絡零件外形尺寸。過渡圓弧選R3~R5mm,圓環臺外徑則保證單邊至少5mm 余量。根據毛坯加工圖,設計沖壓模具如圖4所示。
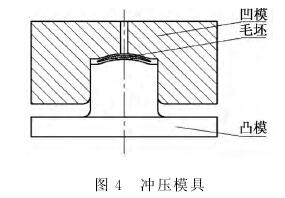
凹、凸模通過中心的導向柱進行沖壓。使用時,先將凹模平放涂油,放入板料,壓上凸模,逐漸增加壓力至工藝要求。脫模時,采用細銅棒插入凹模中心的通孔內輕敲毛坯。
2.2 定位基準的選擇與轉換
罩類零件的定位基準一般都在工藝臺上,根據加工需要,工藝臺可以設計成圓柱、圓環和錐臺等。圓棒料加工的罩體類零件主要采用圓柱和圓環工藝臺定位;鍛造件和沖壓件主要采取圓柱和錐臺定位,其中沖壓的圓弧類罩體零件主要以圓環定位,有時可采用中心孔作為輔助基準。
2.3 專用工裝的設計
沖壓完后的毛坯進行切邊處理,需要使用的工裝如圖5所示。加工時先與待加工半成品的外弧面配車堵頭2端面上的內弧面,然后將堵頭1裝夾固定在主軸上,與待加工半成品的內弧面配車端面上的圓弧凸臺。工件放在兩堵頭的內、外圓弧面之間,用百分表找正后進行加工。
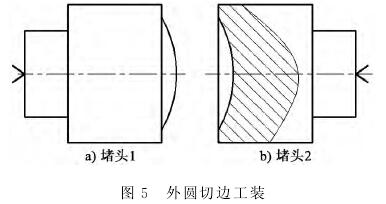
經過切邊、車制形成的裝夾基準需要采取定位胎具進行夾持,常見的定位工裝有如下2種。
1)以圓環類工藝臺定位的工裝。將工件上的圓 環臺放入定心軸(見圖 6)口部的臺階孔內,用背帽壓緊。定心軸上的臺階定位孔與工件上圓環定位臺的配合間隙直接決定零加工的同軸度,間隙越小,同軸度越 高。該種 工 裝 的優點是符合定位基準統一原則,工件的內、外型加工的定位基準 不變可以獲得較高的加工精度;缺點是定心軸上的臺階定位孔與工件上圓環定位臺的配合間隙不易控制,還需要控制圓環臺的長度以便于拆卸工件。
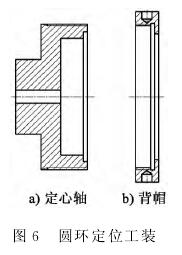
2)以工藝錐臺定位的工裝。該種工裝容易獲得很高的幾何精度,定位基準是工件的內錐面和外錐面。當外錐面定位時,背帽壓緊工件端面;當內錐面定位時,錐套背帽壓緊工件的外錐面。該種工裝需要在工件大端方向留出5~10mm軸向余量的工藝錐臺。外錐面定位工裝(見圖7)的定位錐面可以根據需要決定錐面長度,大小端處錐面定位,
錐面中間空出的情況更有利于裝夾使用。錐面精度應與工件保持一致,必要時適當研磨。
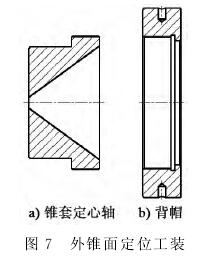
內錐面定位工裝(見圖8)使用方法同上,唯一不同的是在錐套背帽壓緊工件后留出的工件長度應大于零件的總長。
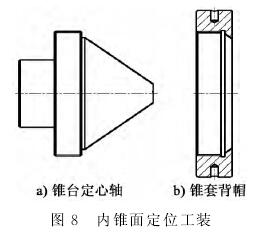
以錐面罩的內、外錐定位的三維示意圖如圖 9所示。
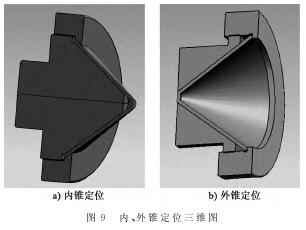
對于曲面罩的定位工裝,可以根據罩體的深淺決定使用上述的哪種工裝,僅改變工裝定位面的形狀就可以滿足加工需要。當罩體的內、外型加工完成后,再次配車圖5所示的外圓切邊工裝,并使用該工裝進行總長和外圓尺寸的后續加工。
2.4 刀具和車削參數
針對不同的加工材料,經過生產實踐,總結出使用的刀具種類和相應的切削參數,對產品的車削加工具有一定的指導意義。罩類零件常見的3種材料對應的刀具及切削參數見表1。
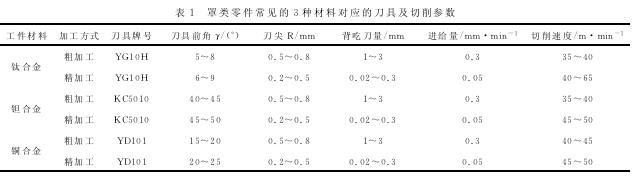
2.5 測量方法
在工件的檢測方面,粗加工和半精加工中使用通用的量具,如游標卡尺、萬能角度尺和百分表等。在精加工中,選用特制的壁厚檢測量具結合三坐標測量機進行檢測。有的零件對同一剖切面壁厚差有嚴格要求,這就需要對零件壁厚差進行精確測量。當現有的壁厚檢測量具無法對零件進行全形面壁厚檢測時,可以設計專用量具來測量。這里推薦一種手握式壁厚檢測量具,該量具采用千分表和量塊輔助工具對零件進行測量,具有測量精度高、速度快、尺寸和長度范圍大等優點。
手握式壁厚檢測量具示意圖如圖10所示。
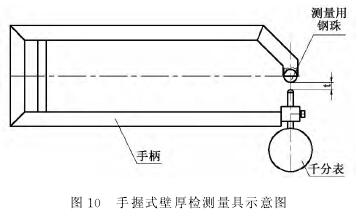
2.6 工藝路線的確定
根據罩類零件的回轉體結構、零件的高精度和表面質量,車削加工工藝路線為:粗車→半精車→精車。具體工藝路線如圖11所示。
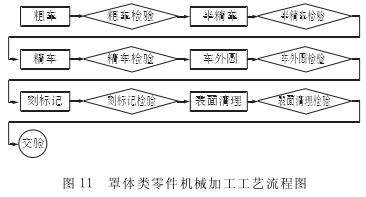
3 、關于車削工藝的說明
3.1 工序的安排
3個加工階段的劃分可以有效消除金屬殘余應力,從而獲得較高的加工精度。比如,零件為內、外錐結構,使用內、外錐面互為基準,通過3個階段的反復加工來滿足產品的壁厚和同軸度等要求。對于罩類零件有外圓和總長度尺寸要求的,一般都放在最后一道車外圓工序。這時采用圓弧定心胎或者內錐定心胎固定工件,并用百分表找正,使跳動小于產品同軸度要求后車制成形。
3.2 工序設備與工件表面質量
罩類零件的表面質量要求高,在數控車床選擇方面,應選擇具有恒線速的數控車床,保證加工錐面時切削速度恒定,從而滿足表面質量要求。
3.3 程序的編制
由于某些零件的尺寸較大,在精加工過程中一次走刀時間較長,這樣會造成刀具的微量磨損,從而影響整個形面的壁厚差要求。此時可利用程序微量調整法,用以消除因刀具磨損而產生的壁厚差問題。具體操作方法是先把內形面精加工完成后,在精加工外形面時,把相應各坐標點按半精加工外形面所測壁厚實際尺寸,按比例補償調整。
4 、結語
經過實際生產的檢驗,罩類零件的沖壓模具方便實用,工裝定位精度較高,刀具及切削參數切合實際,量具測量準確,工藝方案設計合理,已經產生了一定的經濟效益。罩類零件的車削工藝能夠彌補其他加工工藝的不足,在實際生產中具有加工適應性強、快速可靠、成本低和質量穩定的優點。本文所提到的工藝方案設計、專用工裝、測量器具、刀具及切削用量可操作性強,在指導產品生產方面具有參考價值。
投稿箱:
如果您有機床行業、企業相關新聞稿件發表,或進行資訊合作,歡迎聯系本網編輯部, 郵箱:skjcsc@vip.sina.com
如果您有機床行業、企業相關新聞稿件發表,或進行資訊合作,歡迎聯系本網編輯部, 郵箱:skjcsc@vip.sina.com
更多相關信息