航空發動機主燃機匣智能加工技術有多牛!
2020-2-18 來源:金屬加工 作者:趙華衛等
基于自適應控制的發動機主燃機匣加工技術,通過實時監測機床主軸負載變化,并根據負載變化自動調整,實時適應合適的切削參數,使機床保持恒定負載勻速加工,實現主燃機匣的實時監測加工,解決加工效率低和質量不穩定問題。
航空發動機主燃機匣工作條件苛刻,結構復雜、材料加工難度大。受零件材料組織、加工余量和機床冷卻等的影響,經常出現刀具破損斷裂情況,機床主軸負載劇烈變化,造成零件報廢及損害機床。
發動機主燃機匣采用傳統方法加工時,由NC程序設定恒定進給量加工,當出現特殊情況(刀具損耗破損、材料組織不均勻余量突變、刀具碰撞零件和冷卻系統故障)時,操作人員需手動調整倍率開關調節進給大小,難以準確實時監控,并調整機匣加工過程的進給。傳統加工無法將成熟加工經驗與科學數據分析相結合,無法實現發動機主燃機匣加工過程的監控及加工參數的實時優化。
發動機主燃機匣加工現引進自適應控制技術。通過控制器硬件與機床NC系統之間的接口連接,實現對機床主軸轉速、主軸轉矩、進給速度和進給力等切削參數優化控制。可實時動態監控切削參數,并將這些參數存儲到數據庫中。通過內部智能專家系統監控分析切削過程參數狀況,實現單臺機床實時監控。內部智能專家系統可實現以下功能:①獲取加工中振動、切削力、刀具磨損、材質變化、切削余量突變和冷卻系統故障等實際狀態信息。②綜合分析檢測的主軸負載、刀具切削參數。③實時感知預測加工工況。
內部智能專家系統讀取庫中經驗數據和加工信息,分析判斷加工狀態是否理想,不理想時,動態優化切削參數,優化加工過程。通過調整進給量,將加工過程調節到最優狀態,實現加工優化及實時監測,解決燃燒室機匣加工中困擾技術人員的實時監控主軸負載問題。
1.零件結構特點及加工難點
發動機主燃機匣零件結構相當復雜,外形有安裝邊、加強筋、噴嘴安裝座和型槽等特征。機匣材料為GH4169,Ⅱ類鍛件,硬度≤277HBW,材料屬難加工材料,數控加工難度大,加工中使用整體合金刀具數量非常多。加工過程中出現異常后,需操作人員手動調整、操作人員加工中不能離開設備。當出現刀具磨損斷裂、加工余量突變和機床切削液供給不足時,操作人員無法及時發現問題。零件加工周期長,制造成本高,加工時間無法精確統計。操作人員無法解決機床負載變化導致的零件超差及損害機床等問題。發動機主燃機匣零件如圖1所示。
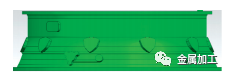
圖1燃燒室機匣零件
2.自適應控制加工技術
(1)刀具磨損監測 發動機主燃機匣傳統加工方法,一般通過判斷刀刃崩裂、零件表面質量、切屑顏色和切削聲音等簡單方式識別刀具磨損,而在全封閉設備上加工時,無法通過目視觀察和聲音變化來發現刀具斷裂、崩齒和磨損等意外情況的發生。刀具磨損及使用壽命不能有效監控。自適應控制系統能夠記錄首件加工過程中主軸功率的即時變化,并將其作為后續零件的切削標準。在后續零件的切削過程中一旦出現因刀具磨損造成主軸功率發生較大變化時,控制系統就會自動發出功率異常報警信息,提醒更換刀具,監測刀具磨損。
運用自適應控制技術,加工中可通過主軸過載報警曲線圖隨時監測刀具磨損狀態,如圖2所示。圖2中縱坐標橙色部分表示刀具磨損時主軸過載隨時間變化。藍色表示刀具切削材料隨時間變化。綠色表示切削載荷控制系統啟動狀態隨時間變化。灰色表示主軸旋轉狀態隨時間變化,紅色線條表示進給倍率曲線隨時間變化,綠色線條表示主軸功率隨時間變化。紅色三角符號表示警報信息。橫坐標表示加工時間。對于任何刀具,當刀具磨損達到“警報”過載極限時,切削載荷控制系統發出警報信息。根據報警信息,系統發出更換刀具、修改切削進給量的指令控制整個切削過程。刀具磨損變化時,無需調整機床倍率及人為干預加工。
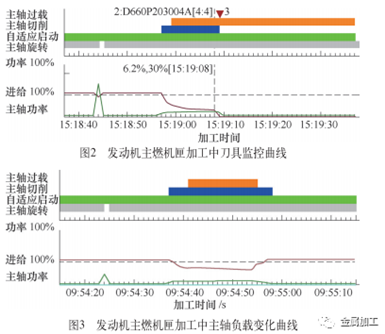
(2)機床主軸負載控制 傳統加工方法無法對主軸負載的變化進行直接監控,一般通過主軸聲音變化來判斷是否正常切削,非正常切削時通過人工調整機床各參數開關控制切削參數,使主軸負載控制在額定范圍之內。
自適應控制系統可精確控制整個加工過程中的主軸負載,能根據主軸負載的變化量即時調整切削參數,保證主軸的切削功率維持在一定的范圍之內,實現恒速度加工向恒負載加工的轉變。加工過程一旦出現刀具破損斷裂、刀具切入切出零件、零件材料組織不均勻、零件加工余量突變和機床切削液供冷故障等異常狀態時,切削載荷控制系統就會自動將進給速率衰減到合理范圍。
圖3所示為某發動機主燃機匣加工中的主軸負載變化曲線圖,圖中縱坐標表示加工時間,橫坐標是對主軸過載狀態、主軸切削狀態、功率及進給隨時間變化的描述曲線。隨著主軸負載增加,系統自動降低切削速度,當切削速度達到設定的下限值時,系統強行停止設備,并發出報警信息(進給速率小于設定下限,停機,主軸過載保護設置為“立即停止”)。切削載荷控制系統判斷主軸負載是否達到主軸承載最大值,當達到最大值時,通過降低進給大小,使切削負荷滿足系統中設置的主軸負載安全值。只要主軸負載允許,切削載荷控制系統將進給提高到最大允負荷水平。在保護機床主軸情況下恒負載加工零件。
(3)切削參數優化 傳統加工在NC程序中給定了固定的切削參數,設備只能按照給定的參數加工,存在空走刀及進退刀速度慢過程。切削過程不能根據余量大小調整切削參數,造成加工效率低、加工質量不穩定的問題。
自適應控制系統能夠將即時切削參數與系統庫中理論參數對比,自動補償NC程序設定的恒定進給,優化切削參數至最合適范圍,使整個加工過程的切削參數更加科學優化。使用切削參數優化技術后,燃燒室機匣加工過程更加優化,不僅起到防止刀具碰撞、保護機床的功能,同時也縮短了零件的加工周期。
以φ16R4mm整體硬質合金銑刀切削為例,在應用切削載荷控制系統前毎把刀具只能加工3處噴嘴座,應用后每把刀具可加工5處噴嘴座。刀具壽命明顯提升。
傳統機匣加工,編程人員根據經驗以設備承受最大負載設定加工進給。而實際處于最大載荷時間段只占生產時間很少部分,絕大多數時間機床是處于非飽和加工狀態。利用切削參數實時優化技術,使機床加工始終處于飽和狀態。在保證設備安全和零件質量前提下,挖據設備利用率。發動機主燃機匣應用切削參數優化前后加工效率提升見表1,表中僅列出部分刀具提升效率。
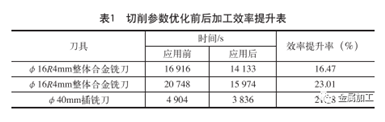
發動機主燃機匣切削參數優化前加工時間為249 727s,優化后所用時間為207 193 s,效率提升率為17.03%。統計時間中不含工件的裝夾、找正、對刀、換刀、程序校對和測量等輔助時間,機匣加工時間精確至秒。
3.結語
通過研究,得出以下結論:
(1)實現對主軸負載實時監測 當加工中刀具損耗或破損、材質不均勻、材料硬點、余量突變、刀具碰撞零件和冷卻系統故障時,通過優化進給避免了切削沖擊主軸,實現了恒速度加工向恒負載加工的轉變。
(2)實現刀具磨損監測,保護刀具 解決困擾技術人員的刀具實時監問題,機床在無人監控情況下,可自動采取科學合理的參數、實時適應主軸負荷和切削工況加工零件。
(3)實現零件加工過程實時監控優化,提高了加工效率17% 單臺設備零件加工時間精確可控,無人為干頂。整體生產進度可以科學精確規劃。并保持最優零件加工狀態。
投稿箱:
如果您有機床行業、企業相關新聞稿件發表,或進行資訊合作,歡迎聯系本網編輯部, 郵箱:skjcsc@vip.sina.com
如果您有機床行業、企業相關新聞稿件發表,或進行資訊合作,歡迎聯系本網編輯部, 郵箱:skjcsc@vip.sina.com
更多相關信息