基于指數函數的機床主軸熱誤差補償模型
2017-12-15 來源: 山東大學機械工程學院 山東永華機械 作者:王乾俸 張松 陳舟 張寶雷 江誠
摘 要:在對機床主軸進行熱特性分析的基礎上,建立了基于指數函數的機床主軸軸向熱誤差補償模型。該熱誤差補償模型建模時間短、資金成本低,能夠方便快捷地應用到工廠生產環境中。通過實驗獲得不同轉速下的主軸軸向熱變形數據。使用回歸分析和最小二乘法建立了穩定狀態下主軸軸向變形量和時間常數的估計方程,進而建立了基于指數函數的熱誤差補償模型。該模型可以預測不同轉速下主軸的軸向變形量。通過實驗證明了該熱補償模型在機床主軸恒速運轉和變速運轉兩種工況下均具有較高的精度。
關鍵詞:熱補償模型;熱變形;指數函數;機床熱特性
0、引言
機床熱誤差是指由機床熱變形導致的加工誤差或運動誤差。熱誤差是影響數控機床加工精度的主要誤差源之一[1]。機床內部產生的熱量和環境溫度梯度致使機床溫度場復雜多變。隨著機床幾何定位精度和加工性能的提高,熱變形誤差嚴重影響了機床精度。
通常抵消熱誤差的方法主要包括熱穩定性設計、溫度控制和熱誤差補償三種方法[2]。熱穩定性設計是指通過采用新型材料改進設計方法和制造工藝,提高機床精度和剛度,以降低加工誤差。然而,當機床精度達到一定程度后,提高機床精度的難度較大且成本較高。溫度控制一般是指使用相關技術來控制機床溫度。但是溫度控制總是滯后于溫度升高,即只有溫度變化后才能進行控制。熱誤差補償則是對由于溫度波動引起的零件尺寸變化進行補償。該方法不被限制于機床的設計階段,可以提高已有機床的加工精度,因此越來越受到重視。由于機床主軸在高速運轉下將產生大量的熱量,機床的加工精度在很大程度上依賴于機床主軸的精度[3]。對主軸熱變形影響最大的因素是主軸前后軸承的摩擦熱。當主軸旋轉時主軸前后軸承摩擦生熱,產生的熱量傳遞到主軸和刀柄等,導致主軸系統的熱變形,從而影響機床的加工精度。因此,對主軸系統的熱誤差進行補償至關重要。
在熱誤差補償中熱誤差模型的建立是關鍵環節。最常見的熱誤差建模方法主要有兩種:①統計回歸建模法,即根據統計理論對熱誤差數據和機床溫度值進行相關分析,用最小二乘原理進行擬合建模[4-5],統計回歸法是以系數的形式表現機床的特征信息;②神經網絡建模法[6],從理論上說,神經網絡能以任意精度逼近任意非線性映射,但神經網絡建模法需要大量的數據用于訓練神經網絡,該建模方法需要花費大量的時間用于數據采集和模型訓練[7-8]。由于建模成本高且傳感器安裝困難,這兩種建立熱誤差補償模型的方法通常不會被采納[9]。
本文提出一種基于主軸轉速的熱誤差模型。該模型只需主軸轉速、無需溫度數據,就可以預報機床的熱誤差。主軸轉速能夠通過工件的NC加工程序得到,因此補償工作可以與編制加工程序一并進行,從而無需添加任何硬件設備就可實現機床的熱誤差補償。該模型具有預報精度高、能夠方便快捷地應用于工廠環境的特點。本文首先通過機床熱特性分析實驗測量主軸的軸向熱變形數據,然后根據實驗分析結果建立基于指數函數的熱誤差補償模型,最后使用該模型對機床主軸恒速運轉和變速運轉兩種工況下的機床主軸軸向變形量進行補償。結果表明,該模型在這兩種不同工況下均具有較高的精度。
1、 機床主軸熱誤差測試及分析
為了進行機床主軸熱特性分析,首先通過實驗測量機床在不同轉速下空轉時主軸的軸向熱變形量、主軸軸端溫度和機床環境溫度。實驗裝置如圖1所示,使用東華DH904 電渦流位移傳感器和Pt100鉑電阻溫度傳感器,測量韓國大宇立式加工中心主軸的熱變形數據。電渦流位移傳感器用于測量主軸的軸向熱變形量,鉑電阻溫度傳感器用于測量主軸的軸端溫度和機床環境溫度。表1和表2分別為立式加工中心和電渦流位移傳感器的規格參數。
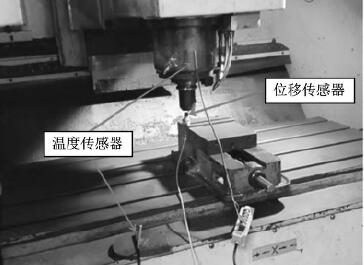
圖1 試驗裝置
表1 立式加工中心規格參數
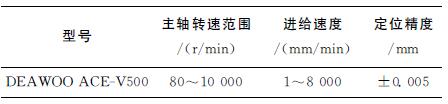
表2 DH904電渦流位移傳感器規格參數
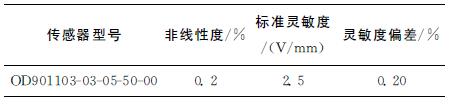
測量不同轉速下主軸的軸向變形量,步驟如下:
(1)主軸在2 000r/min轉速下空轉,直到主軸軸向變形量達到穩定狀態。
(2)主軸停止運轉,直到主軸軸端溫度回到初始值。
(3)使用信號采集系統記錄以上過程中的主軸軸向變形量和主軸軸端溫度以及環境溫度。
(4)在主軸轉速分別為2 500,3 000,3 500,4 000,4 500,5 000,5 500,6 000r/min下,重復以上步驟。
圖2為不同轉速下主軸的軸向變形量隨時間的變化曲線。從圖中可以看出:在機床主軸運轉的初始階段,主軸軸向變形量的增長速度均較快,隨著機床主軸的運轉,主軸軸向變形量的增長速度逐漸變緩,并且在7 200s左右時主軸軸向變形量均基本達到穩定狀態。圖3所示為主軸軸端溫度隨時間的變化曲線。從圖中可以看出:不同轉速n 下主軸軸端的溫度在7 200s左右時也基本達到穩定狀態。圖4所示為主軸軸端溫升變化曲線。從圖中可以看出:主軸轉速n越大,主軸軸端溫升越大。圖5所示為不同轉速下機床主軸熱變形達到穩定狀態后機床主軸的軸向熱變形量。從圖5可以看出,穩定狀態后機床主軸的軸向變形量與主軸轉速呈近似線性關系。基于以上分析,可以發現主軸的軸向變形量Δz隨運轉時間t的變化情況基本符合先快后慢再穩定的自然指數模型增長規律。
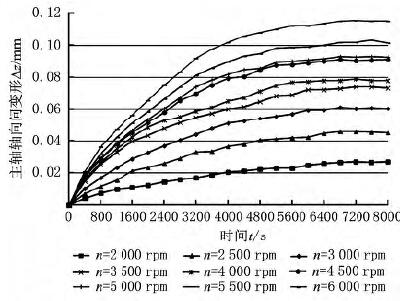
圖2 不同轉速下主軸的軸向變形量
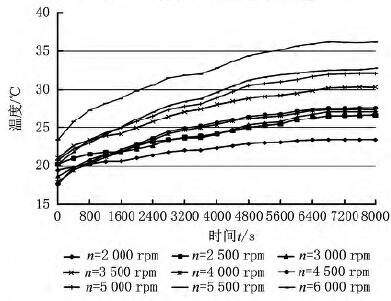
圖3 不同轉速下主軸的軸端溫度
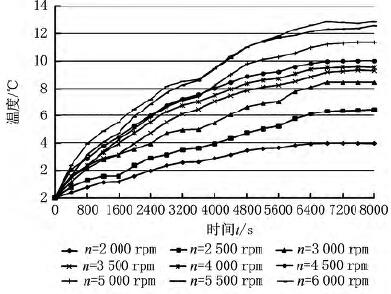
圖4 不同轉速下主軸的軸端溫升
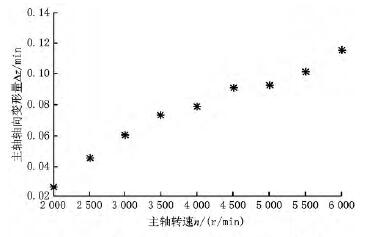
圖5 文檔狀態下不同轉速對應的主軸的軸向變形量
2 、主軸熱誤差補償模型及驗證
2.1 主軸熱誤差補償模型
根據機床主軸熱特性實驗的分析結果,可以建立一種基于指數函數的熱誤差補償模型,以補償主軸軸向熱變形量。熱誤差補償模型的基本形式如下[10]:
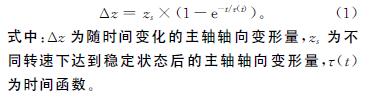
為確定zs的表達式,使用實驗數據建立了zs的估計方程。使用回歸分析和最小二乘法進行直線擬合,以表達穩定狀態下的主軸軸向變形量和主軸轉速n、穩定狀態主軸軸端溫度與初始溫度之差ΔT的線性關系。擬合直線公式如式(2)所示。
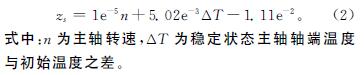
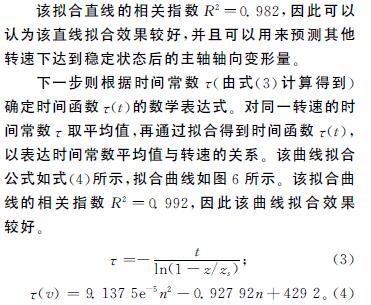
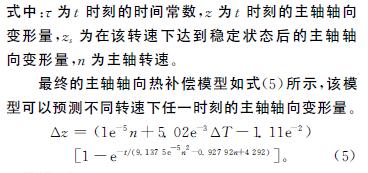
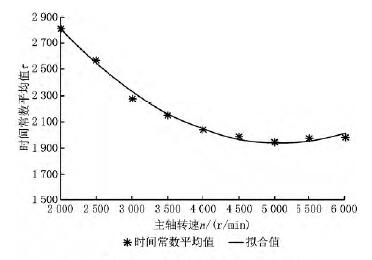
圖6 時間常數均值--主軸轉速擬合曲線
2.2 實驗驗證
為驗證該熱誤差補償模型的精度,對主軸恒速運轉和主軸變速運轉兩種工況下的主軸軸向變形量進行補償。每種工況下分別測量主軸空轉時的主軸軸向變形量和銑削鋁合金工件的加工尺寸。
2.2.1 主軸恒速空運轉
在主軸恒速空轉工況下測量主軸的軸向變形量,即:使機床分別在2 400r/min、4 400r/min轉速下運轉8 000s,記錄該過程中的主軸軸向變形量。圖7為主軸軸向變形量隨時間的變化曲線,以及對主軸軸向變形量的預測曲線。由圖7可知,2400r/min轉速下補償前主軸的軸向最大誤差為0.043 72mm,補償后的最大誤差為0.004mm,精度提高了92%;4 400r/min轉速下補償前主軸的軸向最大誤差為0.087 34mm,補償后的最大誤差為0.007 92mm,精度提高了90.7%。由此證明,在主軸恒速空轉時該模型具有較高的精度。
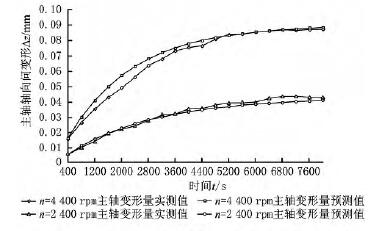
圖7 主軸恒速空轉模型預測結果
2.2.2 主軸恒速切削
使機床恒速運轉切削鋁合金,通過測量工件的加工誤差判定機床主軸熱變形量的大小。本實驗使用300mm×46mm×17.3mm的鋁合金方塊作為實驗樣本,表3為鋁合金材料參數。本實驗中使用帶有循環可轉位刀片的立銑刀,銑刀直徑為20mm。圖8為切削實驗裝置,表4為切削參數。工件加工誤差除了包括熱誤差,還包括機床幾何誤差、定位誤差以及測量誤差等,因此以初始時刻(t=0)加工槽底面作為基準,分別測量后續加工槽底面與基準之間的距離,作為因主軸熱變形而導致的加工誤差。表5和表6分別為2 400、4 400r/min轉速下的機床主軸熱變形量、模型預測熱變形量和預測誤差,根據表5和表6可以證明該模型在主軸恒速切削情況下的補償精度較高。例如:主軸轉速為2 400r/min時補償前的最大熱變形量為0.053mm,補償后的熱變形量為0.012 8 mm,機床精度提高75.8%。主軸轉速為4 400r/min時補償前的熱變形量為0.079mm,補償后的熱變形量為0.013 7mm,機床精度提高82.7%。由于機床切削過程中功率增大、軸承負載增大導致主軸系統產熱增加,并且測量工件尺寸時不能排除測量誤差、定位誤差和機床振動等對測量數據的影響,切削條件下模型精度必然降低。
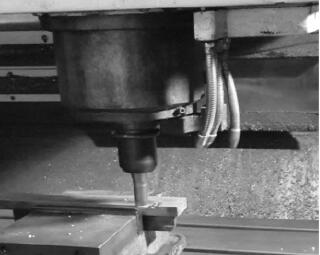
圖8 銑削試驗裝置
表3 鋁合金材料參數

表4 銑削參數
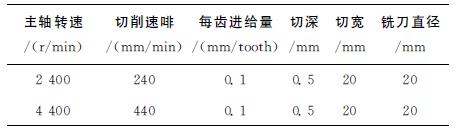
表5 2 400r/min轉速下工件誤差及其預測值
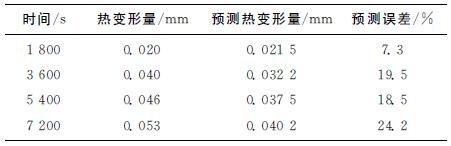
表6 4 400r/min轉速下工件誤差及其預測值
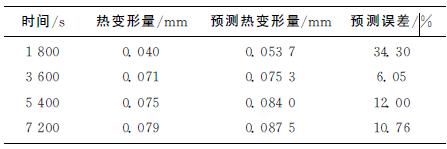
3.2.3 主軸變速空運轉
在主軸變速空轉工況下測量主軸的軸向變形量,即:使機床按照圖9所示的轉速運轉,記錄該過程中的主軸軸向變形量。圖10為主軸軸向變形量的實際值和預測值,誤差補償前最大誤差為0.088 6mm,補償后最大誤差為0.005 2mm,主軸精度提高了約94%。由此證明,該熱誤差補償模型在變速空轉情況下仍具有較高的精度
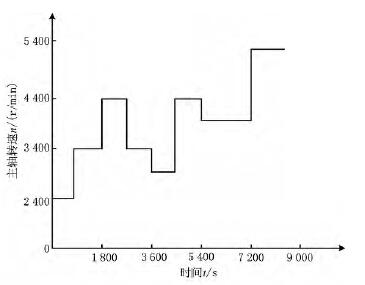
圖9 主軸變色試驗
3.2.4 主軸變速切削
在與主軸恒速切削實驗相同的條件下進行主軸變速切削實驗。主軸轉速變化情況與圖9一致,銑削參數和刀具均與主軸恒速切削工況一致。表7為機床主軸熱變形量、模型預測熱變形量和預測誤差。表7表明,該模型在主軸變速切削情況下也具有較高的精度,補償前機床最大熱變形量為0.082mm,補償后最大熱變形量為0.008 6mm,機床精度提高了89.5%。但是與主軸空轉下進行補償的結果相比,切削情況下的補償精度也有所降低。
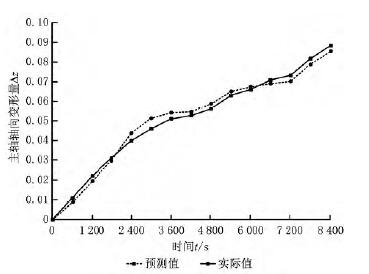
圖10 主軸變色空轉工況模型預測結果
表7 變速切削工況下工件誤差
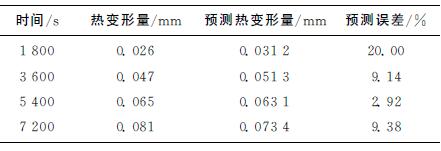
3、 結束語
本文在對機床主軸系統進行熱特性分析的基礎上,建立了基于指數函數的熱補償模型,并進行了實驗驗證。本文的主要工作及相應結論如下:
(1)通過測試數控加工中心主軸的軸向熱變形量和軸端溫度,對機床主軸進行熱特性分析后可知,在不同轉速下,機床主軸在運行7 200s后均基本達到穩定狀態,穩定狀態后的機床主軸軸向變形量與主軸轉速呈近似線性關系。主軸軸向變形量隨時間的變化趨勢符合先快后慢再平穩的自然指數增長形式。
(2)根據數控加工中心主軸的熱特性,建立了基于指數函數的熱補償模型。該模型只需主軸轉速就可以預報機床的熱誤差,因此該模型的建模資金成本低、時間短,能夠快速應用于工廠環境,而且模型形式簡單,易于實施熱誤差補償。
(3)在兩種不同工況下對該模型的精度進行了驗證,結果表明該模型對于預測兩種不同工況下的機床主軸熱變形量均具有較高的精度。
本文通過分析機床主軸系統的熱態特性建立了基于指數函數的熱補償模型。然而除了機床主軸系統外,其他關鍵零部件的熱變形也將對機床的加工精度產生影響。因此,下一步應進行相關實驗和研究,建立能夠補償多個機床零部件熱誤差的補償模型。
投稿箱:
如果您有機床行業、企業相關新聞稿件發表,或進行資訊合作,歡迎聯系本網編輯部, 郵箱:skjcsc@vip.sina.com
如果您有機床行業、企業相關新聞稿件發表,或進行資訊合作,歡迎聯系本網編輯部, 郵箱:skjcsc@vip.sina.com