基于全微分模型的打磨機械臂靜態(tài)誤差分析
2017-1-3 來源: 東北大學機械工程及自動化學院 作者:張秀珩 柳洪義 巴鵬
摘要: 針對打磨機械臂系統(tǒng)的精度設計問題的解決, 基于DH 模型建立了機械臂的運動學參數(shù)模型, 并基于全微分法建立了運動學參數(shù)誤差與末端誤差的數(shù)學關系。對機械臂可能出現(xiàn)的誤差源進行分析, 歸納誤差源的類型, 代入誤差模型分別進行仿真, 并對結構誤差與傳動誤差對機械臂末端位置的影響進行比較。結果表明: 傳動誤差對X、Y 向的位置影響較大, 而結構誤差對Z 軸的影響較大, 這些信息可用于對實際機械臂參數(shù)誤差的回歸分析, 為在機械臂設計及制造階段、機械臂的制造及裝配誤差預計及優(yōu)化提供數(shù)據(jù)參考。
關鍵詞: 打磨機械臂; 全微分; 靜態(tài)誤差; 誤差分析
0.前言
大多數(shù)的工業(yè)用機械臂, 其末端執(zhí)行器的位姿精度是衡量其工作性能的重要指標。對機械臂進行運動學標定是目前提高機械臂靜態(tài)精度最有效的方法, 最普遍的做法是首先建立機械臂的正運動學模型, 既而建立相關的位姿誤差模型, 通過識別機械臂末端位姿與各運動學參數(shù)之間的關系來實現(xiàn)誤差優(yōu)化, 從而達到提高位姿精度的目的。在實際應用中, 該方法可大幅提高機械臂的靜態(tài)精度, 但由于各種機械臂在結構和功能上的差別, 其各單項原始輸入誤差對末端位姿誤差的影響必然不同[1] , 所以對影響位姿誤差的誤差源的分析及在設計階段對機械結構的改進也尤為重要。
影響機械臂靜態(tài)誤差的因素主要有幾何誤差(靜態(tài)誤差)、因動態(tài)載荷及機體振動引起的動態(tài)誤差、因溫度影響引起的誤差及環(huán)境、控制系統(tǒng)和算法誤差[2] 。IMOTO J 等[3] 研究了幾何誤差、溫度變化等因素對機械臂定位精度的影響。SANTOLARIA J 等[4]為優(yōu)化機械臂運動學標定條件, 基于輸出姿勢誤差和測量誤差的線性關系, 給出一種在標定后用于估計輸出姿態(tài)誤差和誤差評價指標的方法。ZHUANG H等[5] 基于Monte Carlo 方法, 提出在機械臂標定過程中采用圓點分析法評估標定標定結果的不確定性。在機械臂標定方法的研究發(fā)展了多種測量方法, 如HOLLERBACH J M 等[6] 通過在機械臂末端執(zhí)行器上加運動約束, 使機械臂末端保持固定的閉環(huán)標定方法。IKITS M 等[7] 通過確定機械臂的各關節(jié)軸線位置, 解析各旋轉軸之間的代數(shù)關系并確定運動學參數(shù)。KHALIL W 等[8] 采用極坐標法研究多約束激光跟蹤系統(tǒng)運動目標標定。
本文作者根據(jù)實際工程項目需求, 對課題組研制開發(fā)的發(fā)動機絕熱層機械打磨機械臂的靜態(tài)精度進行研究, 為保證打磨精度, 首先對機械臂的靜態(tài)精度有重要影響的因素進行分析, 確定靜態(tài)誤差的靈敏度, 再針對機械臂的末端位置及姿態(tài)精度進行標定。
1.打磨機械臂運動學建模
為獲得打磨機械臂運動學模型, 采用D-H 方法建模。根據(jù)機械臂的機械構型, 對機械臂主體部分進行簡化, 選取本體質心處, 建立基坐標系SB , 大臂底座中心建立坐標系S1 , 并依次建立各關節(jié)坐標系和末端坐標系S e 。關節(jié)1、2、3對應的變量分別記為d , θ2, θ3,桿件1 、 2、 3 的長度分別記為 l、1 l 2、 l3。用D-H (Denavt-Hartenberg) 法建立各坐標系模型。根據(jù)文中所研究的打磨機械臂幾何結構及運動參數(shù)分別如圖1 和表1 所示。
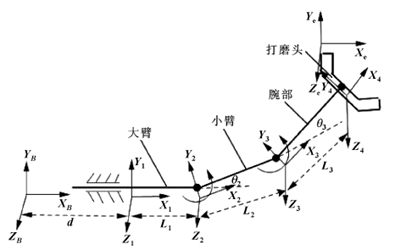
圖1 機械臂各關節(jié)的運動學參數(shù)及坐標系
表1 D-H 參數(shù)表
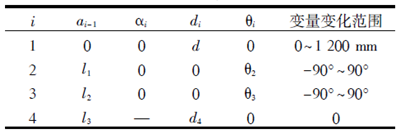
根據(jù)表1 所示機械臂參數(shù)可確定運動學模型如下:
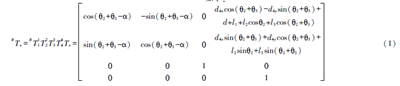
2.打磨機械臂誤差建模
采用全微分的方法對式(1) 進行微分, 即可得到
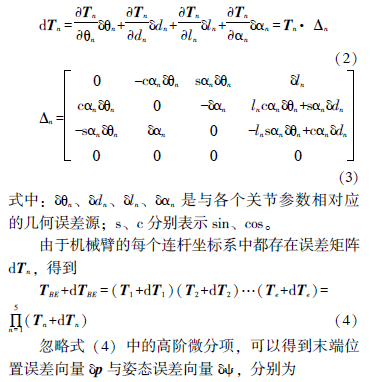
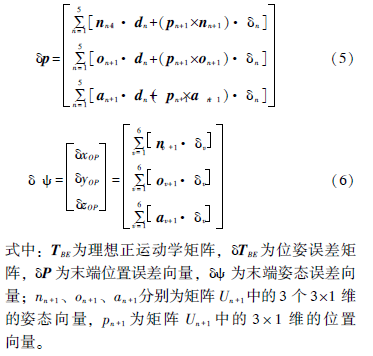
為了描述末端位姿誤差與各幾何誤差源之間的關系, 采用矩陣的形式建立串聯(lián)機構的幾何誤差模型為:


3.打磨機械臂靜態(tài)誤差分析
為完成機械臂標定并正確評價機械臂的性能, 誤差模型的建立首先應從了解其誤差源入手。當忽略控制算法誤差的影響后, 根據(jù)誤差的性質和來源來看,主要包括靜態(tài)誤差和動態(tài)誤差。其中靜態(tài)誤差包括由于機械臂本體的制造和裝配過程中產生的幾何參數(shù)誤差, 還有因環(huán)境(如溫度)、傳動誤差及因重力等引起的變形誤差, 與幾何參數(shù)誤差相比, 這部分誤差所占比重較小。動態(tài)誤差主要指機械臂在工作過程中因力矩、摩擦力、振動等原因隨時間變化的誤差。在這諸多的影響因素中, 幾何參數(shù)誤差是影響機械臂精度的最重要的因素, 因此主要針對這一誤差加以分析。
在影響機器人末端執(zhí)行器精度的主要因素中, 重點考慮結構誤差、傳動誤差、關節(jié)間隙與連桿機構的撓性。對于旋轉關節(jié), 隨著旋轉角的增大, 關節(jié)的旋轉誤差將累積增大, 而對本機器人來說由于其移動關節(jié)的采用直線導軌結構且運動量程較長, 所以其直線度誤差不容忽視。因此在選擇誤差項時根據(jù)機器人的本體結構, 確定各連桿的長度誤差、直線度誤差、旋轉關節(jié)的垂直度誤差及各關節(jié)的運動參數(shù)誤差作為主要誤差源, 其誤差項的取值及極限范圍如下:
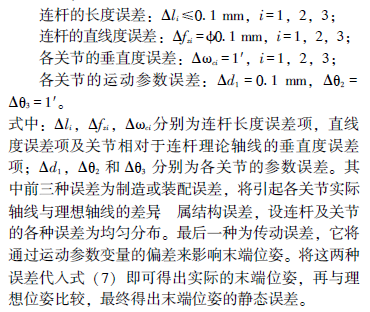
對本機械臂來說, 其末端的位置精度是影響其工作性能的主要因素, 所以這里僅對機器人的末端位置誤差進行分析, 機械臂在實際工況中執(zhí)行兩個動作,一個是僅大臂直線的移動動作; 一個是3 個關節(jié)都運動的曲線動作, 針對各單項誤差分別對兩種動作時的誤差進行仿真, 可得到關節(jié)誤差、結構誤差與末端位置誤差的關系曲線如圖2—7 所示。(1) 當僅考慮連桿長度誤差時, 軌跡1 和軌跡2的末端誤差與連桿長度誤差之間的關系如圖2 和3所示。
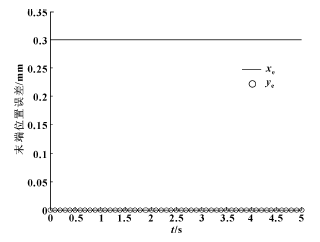
圖2 沿軌跡1 運動時末端的位置誤差分布
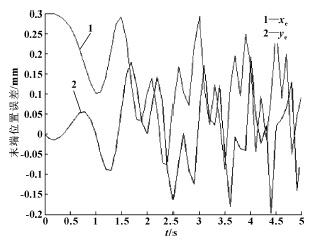
圖3 沿軌跡2 運動時末端的位置誤差分布
由圖可以看出, 對軌跡1, 當僅移動關節(jié)運動時, 連桿誤差僅對末端X 軸方向位置精度有影響,且xe =0.3 mm; 對軌跡2 來說, 因3 個關節(jié)的共同運動產生的末端位置在X 和Y 2 個方向的位置精度都有影響, 從變化規(guī)律上看2 個方向的誤差變化相似,但在X 軸正向的影響明顯較大, 均值約為0.25 mm。
(2) 當僅考慮因結構參數(shù)誤差因素時, 軌跡1與軌跡2 的末端位置誤差表現(xiàn)如圖4 和5 所示。
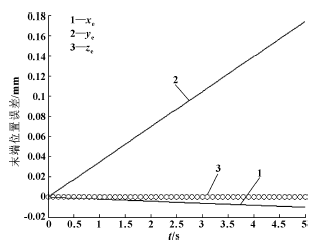
圖4 沿軌跡1 運動時末端的位置誤差分布
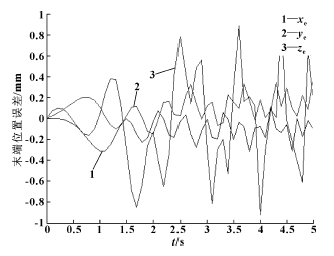
圖5 沿軌跡2 運動時末端的位置誤差分布
由圖可以看出, 當僅考慮幾何誤差(形狀與位置誤差) 時, 對軌跡1, 末端位置在Y 軸方向位置誤差隨移動關節(jié)的運動而逐漸變大, X、Z 軸誤差則較??; 對第二段軌跡來說, 末端位置在3 個方向的誤差都較大, 其中在Z 向的誤差均值為0.6 mm, 且誤差呈周期性變化, X 和Y 向的誤差較小, 誤差均值為0.3 mm 左右。
(3) 僅考慮關節(jié)傳動誤差時, 末端位置精度與關節(jié)角誤差之間的關系如圖6 和7 所示。
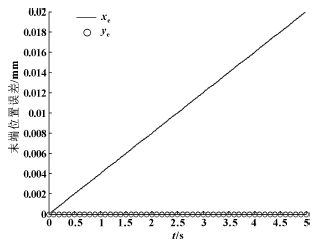
圖6 末端位置誤差與移動關節(jié)誤差的分布關系
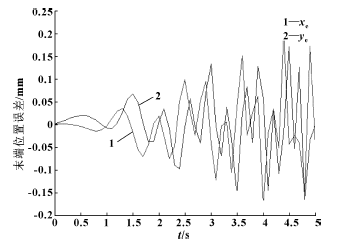
圖7 末端位置誤差與轉動關節(jié)誤差的分布關系
由圖6 可知, 僅考慮移動關節(jié)的傳動誤差時, 末端僅在X 向有誤差, 由于傳動誤差被定義為均勻分布, 所以該誤差大小與關節(jié)位移呈正比例, 在規(guī)定時間內的位置誤差最大為0.02 mm; 由7 圖可知, 當僅考慮關節(jié)角誤差時, 在X 和Y 向的末端位置均有誤差,且隨關節(jié)角的增加, 誤差呈周期性變化, 均值在0.2mm 左右。
為了分析結構誤差和傳動誤差對機械臂末端的綜合影響, 分別令傳動誤差不變, 分析結構誤差對機械臂末端的位置誤差的影響, 再令結構誤差不變, 分析傳動誤差對機械臂末端的位置影響。由上圖可知, 機械臂的關節(jié)傳動誤差在X、Y 方向對末端位置的影響較大, 且呈周期性變化, 而因幾何誤差造成的結構誤差則對Z 向的位置造成影響, 隨著誤差的變大, 末端位置誤差也增大, 成正比例關系, 這是由于末考慮誤差分布的影響。綜合來看, 轉角誤差引起的傳動誤差對末端的影響要小于結構誤差的影響, 因此在誤差補償時應多考慮Z 軸的誤差, 這是由機械臂的結構所決定的。同時根據(jù)以上結果, 在機械臂的精度設計時也應重要關注Z 向尺寸鏈的誤差控制。
4.結論
(1) 采用DH 模型法建立打磨機械臂的運動學參數(shù)模型, 并基于全微分法建立了運動學參數(shù)誤差與末端誤差的數(shù)學關系, 為后面進行誤差分析打好基礎。
(2) 對機械臂可能出現(xiàn)的誤差源進行分析, 歸納誤差源的類型, 代入誤差模型進行仿真, 得出結構誤差與傳動誤差對機械臂末端位置的影響, 并根據(jù)仿真結果對誤差變化對末端位置的影響進行分析, 這些信息可用于對實際機械臂參數(shù)誤差的回歸分析, 為在機械臂設計及制造階段, 機械臂的制造及裝配誤差預計及優(yōu)化提供數(shù)據(jù)參考。
投稿箱:
如果您有機床行業(yè)、企業(yè)相關新聞稿件發(fā)表,或進行資訊合作,歡迎聯(lián)系本網(wǎng)編輯部, 郵箱:skjcsc@vip.sina.com
如果您有機床行業(yè)、企業(yè)相關新聞稿件發(fā)表,或進行資訊合作,歡迎聯(lián)系本網(wǎng)編輯部, 郵箱:skjcsc@vip.sina.com
更多相關信息
業(yè)界視點
| 更多
行業(yè)數(shù)據(jù)
| 更多
- 2025年5月 新能源汽車銷量情況
- 2025年5月 新能源汽車產量數(shù)據(jù)
- 2025年5月 基本型乘用車(轎車)產量數(shù)據(jù)
- 2025年5月 軸承出口情況
- 2025年5月 分地區(qū)金屬切削機床產量數(shù)據(jù)
- 2025年5月 金屬切削機床產量數(shù)據(jù)
- 2025年4月 新能源汽車銷量情況
- 2025年4月 新能源汽車產量數(shù)據(jù)
- 2025年4月 基本型乘用車(轎車)產量數(shù)據(jù)
- 2025年4月 軸承出口情況
- 2025年4月 分地區(qū)金屬切削機床產量數(shù)據(jù)
- 2025年4月 金屬切削機床產量數(shù)據(jù)
- 2025年1月 新能源汽車銷量情況