SL50 型數控車床主軸回轉精度的可靠度研究
2017-4-1 來源:南通職業大學 機械工程學院 作者:張麗萍,李業農,周開俊
摘要:通過以 SL50 型數控車床的主軸組件為例,深入分析了產生主軸回轉誤差運動的原因,提出該數控車床主軸軸承的預緊力界定范圍。對該數控車床主軸軸承磨損情況做了可靠性統計分析,建立了主軸回轉精度壽命的可靠度模型,主軸軸承磨損量與其工作小時數幾乎成線性關系。在該數控車床工作 15000 小時和 20000 小時后,分別檢測了主軸徑向跳動的誤差、主軸軸向竄動誤差和卡盤端面跳動誤差,對主軸回轉精度的下降情況做了統計分析,并進行了回轉精度可靠度計算。
關鍵詞:數控機床;主軸;軸承;磨損;回轉精度;統計分析;可靠度
1.引言
要提高數控機床的加工精度,除了要提高機床的剛度、抗振性和熱穩定性外,首要的是提高主軸組件的幾何精度和回轉精度,在制造過程中可通過先裝配后精加工提高主軸的回轉精度[1] 。從統計分析結果看,軸承的主要失效形式是接觸疲勞磨損、磨粒磨損、粘著磨損和微動磨損[2-3],鑒于此,筆者以 SL50 型數控車床的主軸組件為例,就影響主軸組件的回轉精度的因素,尤其是主軸軸承磨損對主軸回轉精度壽命影響的程度做了深入的探討。
2.產生主軸回轉誤差運動的主要原因分析
SL50 型數控車床的主軸部件,前支承為三個角接觸球軸承,前面兩個軸承大口朝向主軸前端,以承受軸向和徑向切削力;后面軸承大口朝向主軸后端,三個軸承的內外圈軸向由軸肩和箱體孔的臺階定位承受軸向負荷。后支承由一對背靠背的推力角接觸球軸承組成,只承受徑向載荷,并由后壓套進行預緊,結構如圖 1所示。
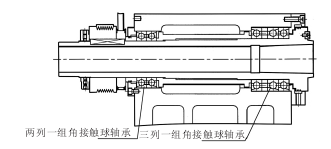
圖 1 SL50 型數控車床的主軸部件結構
一般數控車床而言,主軸的瞬時回轉軸線是經常變動的。根據相對運動的原理,在任何瞬時,一方面主軸繞自己的瞬時回轉軸線旋轉,另一方面,該瞬時回轉軸線還相對理想回轉軸線作軸向的、徑向的和傾角的運動[4-5]。SL50 型數控車床的主軸部件也不可避免存在上述誤差運動。其主要原因有:
(1)主軸支承軸頸的圓度誤差,如橢圓、棱圓及較大的波紋,會造成主軸周期性徑向跳動誤差運動。主軸前后支撐的不同軸及它們徑向跳動的大小和方向的不一致性,會造成主軸的擺角誤差運動。
(2)主軸軸承,特別是前軸承的缺陷,如軸承套滾道的圓度誤差和波紋,滾動體直徑的不一致性及圓度誤差等,會造成主軸的徑向誤差運動。軸承的支撐端面對主軸回轉中心線的不垂直,軸承的滾道及滾動體的誤差,會造成主軸周期性的和非周期性的軸向誤差運動。滾動軸承的摩擦和磨損,使主軸部件的各部分產生不同的熱變形,會造成主軸的徑向誤差運動和軸向誤差運動。
SL50 型數控車床是精密級機床,除了主軸支承軸頸、主軸前后支撐的不同軸等先天性誤差外,主軸軸承的自身誤差和安裝誤差也是引起主軸回轉誤差運動的主要因素之一。只有經過嚴格的生產工藝過程控制,使上述的 2 項誤差降到最小值。
3.主軸軸承的預緊及磨損情況分析
由于滾動軸承內部存在游隙,適當預緊使各個滾動體都承受一定的預負荷,參加工作的滾動體數量增加,直徑略大的滾動體變形較大,使直徑較小的滾動體也承受載荷,從各個方向支承內圈,故可以提高軸承的回轉精度、壽命和剛度[5-6]。SL50 型數控車床在主軸剛起動時,箱體和軸承座還處于常溫狀態,直接受摩擦熱作用的滾動體和內外圈的溫升最快,內部元件和外部元件的溫差最大,當軸承各部分與箱體溫度相對穩定后,預緊力達到最大值并趨于穩定,實測表明,預緊力的工況最大值以達到裝配預緊力的 2 倍左右為宜。預緊力過大,會導致軸承發熱劇烈,加速軸承的磨損。
SL50 型數控車床的主軸部件前支承為三個角接觸球軸承,前兩個軸承串聯,與第三個背靠背組配。通過計算這種組配其軸承預緊力應不小于額定軸向載荷的四分之一,其次,這種高精密主軸前軸承允許溫升為 10℃,軸承生產廠商建議其應預緊力可控制在(1100~1300)N,這樣可有效提升軸承的回轉精度。預緊力再增大,軸承溫升會增大,反而會降低回轉精度。SL50 型數控車床的主軸軸承為高精密角接觸球軸承,滾動體與座圈采用高質量的滾動軸承鋼制造,具有很高的硬度 HRC(60~65),很高的加工精度和很低的表面粗糙度。該主軸軸承的接觸疲勞強度是足夠的,不會產生接觸疲勞磨損。軸承主要是由于磨粒磨損、粘著磨損和微動磨損而導致軸承的回轉精度下降,直至精度失效,故這種軸承的壽命主要為精度壽命。
這種角接觸球軸承由于離心力和陀螺力矩的作用,滾動體鋼球的自轉會產生微滑動。當轉速越高或接觸角越大,微滑動會越大。再者滾動體鋼球與保持架是純滑動接觸,二表面之間的相對滑動摩擦,提高了軸承溫度,加大了軸承磨損。造成軸承磨損的因素是多方面的,多種因素作用下的軸承磨損更加難以預測的防止,軸承磨損使軸承的徑向游隙和軸向游隙增大,從而使主軸回轉精度降低。在跟綜了 SL50 型數控車床主軸的工作情況,主軸在工作10000 小時后,主軸回轉精度有一些下降,由于機床具有一定的精度儲備,故機床沒有超出允許的回轉誤差范圍;工作 15000 小時后,回轉精度繼續下降,比出廠時的誤差加大了 20%,少量用戶提出更換主軸軸承的要求;工作 20000 小時后,回轉精度有較大下降,比出廠時的誤差加大了 35%,部分用戶委托廠方或自行更換主軸軸承。究其原因,85%是由于主軸軸承磨損所致,軸承磨損量與主軸工作小時數幾乎成線性關系。
4.主軸回轉精度壽命的可靠度模型
主軸回轉精度可靠度 R(t)指主軸回轉運動誤差落在最大允許范圍內的概率。
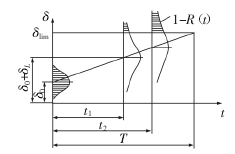
圖 2 主軸軸承的回轉精度壽命可靠度
由于主軸回轉運動誤差隨著時間 t 的增大而增大,使主軸回轉運動誤差的中心發生漂移,散度增大,可靠度下降。當主軸工作了時間 t 后,主軸軸承的精度失效概率 F(t)=1-R(t)明顯比初始時間增大了,如圖 2 所示。且平均誤差與主軸工作時間成線性關系[9]。當規定主軸軸承精度壽命可靠度的大小后,便可由式(1)反推出主軸軸承的精度壽命。
5.主軸回轉精度可靠度計算
以 SL50 型數控車床為例,主軸的誤差運動的 3 種基本形式:即純徑向誤差運動、軸向誤差運動和擺角誤差運動。這些基本形式很少獨立存在,往往是同時并存的。純徑向誤差運動和軸向誤差運動并存時的誤差運動稱為徑向誤差運動,它是指主軸回轉中心線 O1-O1在某一指定位置垂直于其理想中心線 O-O 線方向上的誤差運動。主軸徑向跳動的測量位置,如圖 3 所示 SL50 型數控車床初始工作期間,主軸 a 點徑向跳動均值為 0.006,均方差為0.0010;b 點:主軸徑向跳動均值為 0.011,均方差為 0.0021。主軸工作 15 000 小時后,a 點:主軸徑向跳動均值為 0.007,均方差為 0.0018;b 點:主軸徑向跳動均值為 0.014,均方差為0.0035。主軸工作 20000 小時后,a 點:主軸徑向跳動均值為0.008,均方差為 0.0021;b 點:主軸徑向跳動均值為 0.016,均方差為 0.0043。a 點:主軸徑向跳動允差為 0.010,b 點:主軸徑向跳動允差為 0.020。
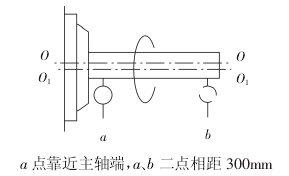
圖 3 主軸徑向跳動的測量位置
軸向誤差運動和擺角誤差運動并存時的誤差運動稱為端面誤差運動,它是指回轉主軸的端面在規定的徑向位置上平行于理想回轉中心線的方向上誤差運動。SL50 型數控車床初始工作期間,主軸中心軸向竄動誤差均值為 0.006,均方差為 0.0010;d 點(距主軸回轉中心 125mm 處):主軸卡盤端面跳動誤差均值為0.011,均方差為 0.0020,如圖 4 所示。圖中:c 為回轉中心,卡盤上d 點的回轉半徑為 125mm主軸工作 15000 小時后,主軸中心 c 點:軸向竄動誤差均值為 0.007,均方差為 0.0016;d 點:主軸卡盤端面跳動誤差均值為0.014,均方差為 0.0036。主軸工作 20000 小時后,主軸中心 c 點:軸向竄動誤差均值為 0.008,均方差為 0.0019;d 點:主軸卡盤端面跳動誤差均值為 0.016,均方差為 0.0042。
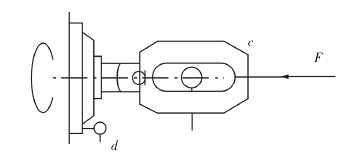
圖 4 主軸軸向竄動誤差和卡盤端面跳動誤差的測量位置
主軸軸向竄動誤差允差為 0.010,d 點:卡盤端面跳動誤差允差為 0.020。主軸初始工作期間,由式(1)計算,a、b、c、d 四點的精度可靠度:Ra(0)=Rb(0)=RC(0)=Rd(0)≈1運用可靠度的計算方法[10-11],主軸工作 15000 小時后各點的精度可靠度:
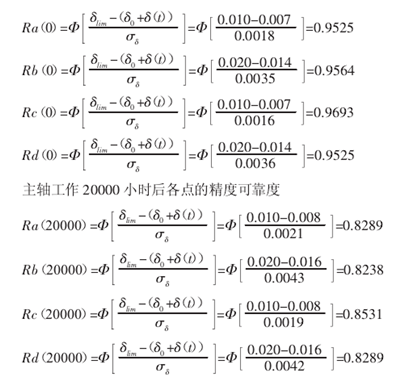
通過上述計算分析,主軸工作 15000 小時后,各項誤差的均值和均方差均加大,離散度增大,說明主軸軸承有一定的磨損,導致精度可靠度下降,但仍保持在 95%以上,該機床已不適宜加工一些重要的精密的零件。主軸工作 20000 小時后,主軸軸承磨損進一步加劇,精度可靠度下降很多,該機床只能用于精度要求不高的加工,若想恢復精度,可考慮送回機床生產廠進行大修,更換主軸軸承。
6.結論
主軸組件是數控機床的重要組成部件之一,它的精度壽命可靠度是數控機床的工作能力的一項重要指標。
(1)主軸軸承誤差是引起主軸回轉誤差運動的主要因素之一。
(2)通過控制這種高精密主軸軸承的預緊力,可有效提升軸承的回轉精度,降低軸承溫升。
(3)當規定主軸軸承精度壽命可靠度的大小后,可反推出主軸軸承的精度壽命。
(4)主軸工作 15000 小時后,各項誤差的均值和均方差均加大,離散度增大,精度可靠度仍保持在 95%以上。
(5)主軸工作 20000 小時后,主軸軸承磨損導致精度可靠度下降到 82%,建議進行更換主軸軸承的機床大修。
投稿箱:
如果您有機床行業、企業相關新聞稿件發表,或進行資訊合作,歡迎聯系本網編輯部, 郵箱:skjcsc@vip.sina.com
如果您有機床行業、企業相關新聞稿件發表,或進行資訊合作,歡迎聯系本網編輯部, 郵箱:skjcsc@vip.sina.com