鈦合金螺旋銑孔的切削力和切削溫度試驗研究
2017-2-21 來源:大連理工大學(xué)精密與特種加工教育部重點實驗 作者:王歡,董志剛,康仁科,楊國林,謝海龍
摘要:螺旋銑孔技術(shù)是航空裝備制造領(lǐng)域新出現(xiàn)的制孔技術(shù),因具有加工質(zhì)量好、效率高等優(yōu)點被用于加工鈦合金、復(fù)合材料等難加工材料。采用包括切削速度、切向每齒進給量、軸向每齒進給量和螺旋導(dǎo)程4個基本加工參數(shù)描述螺旋銑孔過程,分析了基本參數(shù)和螺旋銑孔輸入加工參數(shù)(自轉(zhuǎn)、公轉(zhuǎn)、進給)之間的關(guān)系。在自行研制的螺旋銑孔試驗平臺上開展了鈦合金材料的加工試驗,研究了鈦合金螺旋銑孔加工中切削溫度及切削力的特征,以及基本加工參數(shù)對切削溫度和切削力的影響規(guī)律。試驗結(jié)果表明,在螺旋導(dǎo)程一定時,切削溫度主要由切削速度決定,而與軸向每齒進給量及切向每齒進給量無明顯關(guān)系;而切削力的影響規(guī)律與切削溫度相反。切削溫度是影響螺旋銑孔過程中刀具磨損及加工孔質(zhì)量的主要因素。在需同時保證加工效率及加工質(zhì)量的前提下,應(yīng)盡量選擇大的切向每齒進給量、大的軸向每齒進給量和較低的切削速度。
關(guān)鍵詞:鈦合金;螺旋銑孔;切削溫度;切削力
鈦合金具有比強度高、熱強度好、耐腐蝕、良好的低溫性能,與纖維增強復(fù)合材料相容性好及儲藏資源豐富等優(yōu)點,廣泛應(yīng)用于航空航天、國防軍工等領(lǐng)域,如飛機的機翼、蒙皮、艙段等。連接孔的加工是鈦合金構(gòu)件上最典型和重要的加工之一卜21。由于鈦合金材料的難加工特性,采用傳統(tǒng)的麻花鉆工藝制孔時,容易形成孔壁熱損傷,并存在鉆削質(zhì)量低、孔壁表面質(zhì)量差等問題。螺旋銑孔技術(shù)是航空裝備制造領(lǐng)域新興的高效、高質(zhì)量制孔技術(shù)。螺旋銑孔采用立銑刀,以螺旋軌跡方式進給加工出比刀具直徑大的孔。與傳統(tǒng)的鉆孔技術(shù)相比,螺旋銑孔技術(shù)具有很多優(yōu)點:軸向力小;可以實現(xiàn)一種刀具加工不同直徑孔,減少刀具種類;切屑不連續(xù),排屑空間大,切屑能更好排出,減少切屑與已加工表面的摩擦,從而提高加工表面質(zhì)量;斷續(xù)的加工過程有利于刀具散熱,能夠降低刀具磨損,延長刀具使用壽命等卜81。國內(nèi)外在螺旋銑孔末端執(zhí)行器開發(fā)一一01、螺旋銑孔工藝研究。131和專用刀具研制等方面開展了大量工作。
切削力和切削溫度是切削加工中重要的過程參數(shù),對鈦合金材料制孔精度和加工質(zhì)量有重要影響,國內(nèi)外學(xué)者對鈦合金切削加工的切削力和切削溫度進行了大量研究。作為一種重要的制孔方式,螺旋銑孔加工自出現(xiàn)以來也受到了國內(nèi)外研究人員的關(guān)注。從加工幾何學(xué)角度分析,螺旋銑孔加工過程中銑刀同時做公轉(zhuǎn)、自轉(zhuǎn)和進給運動,加工時同時存在底刃的連續(xù)切削及側(cè)刃的斷續(xù)切削,其未變形切屑的幾何形狀和尺寸與切削參數(shù)之間存在定量的關(guān)系。通過研究銑刀側(cè)刃切削與底刃切削去除量之間的關(guān)系發(fā)現(xiàn),在銑刀形狀固定的條件下,銑刀側(cè)刃切削去除材料和底刃切削去除材料間的比例僅與刀具直徑和加工孔徑有關(guān),該比例對軸向切削力、加工溫度和質(zhì)量有直接影響。螺旋銑孔加工過程中工件上任一點的溫升是銑刀端刃切削生熱與側(cè)刃切削生熱同時作用的結(jié)果,結(jié)合螺旋銑動力學(xué)分析和傳熱學(xué)理論可建立螺旋銑孑L三維溫度預(yù)測模型并分析螺旋銑孔切削溫度特征。利用上述模型分析螺旋銑孔溫度發(fā)現(xiàn),主軸轉(zhuǎn)速與螺旋導(dǎo)程增加時切削溫度升高,且熱源與測溫點越接近時,測量溫度越高心。
上述模型為理解螺旋銑孔加工機理提供了有益參考,但由于建模過程中對熱源的簡化以及求解過程的簡化,在描述螺旋銑孔切削溫度數(shù)值及分布規(guī)律準確性方面還需系統(tǒng)的試驗驗證。在試驗研究方面,采用螺旋銑孔及傳統(tǒng)鉆孔兩種方法在鋁合金、鈦合金、纖維增強復(fù)合材料上進行制孔加工,從切削力、孑L壁質(zhì)量、熱損傷和機械損傷等方面進行對比發(fā)現(xiàn),與傳統(tǒng)的鉆孑L工藝相比,螺旋銑孑L方法在減小切削力、控制切削溫度、保證制孔質(zhì)量等方面均具有明顯優(yōu)勢。
目前國內(nèi)外對鈦合金螺旋銑孑L技術(shù)的試驗研究多集中于一種加工參數(shù)下與傳統(tǒng)鉆孔的對比研究,而對于螺旋銑孑L的重要切削參數(shù)如切削速度、軸向及切向每齒進給量等對于切削溫度及切削力的影響規(guī)律尚不明確。鑒于切削力和切削溫度對螺旋銑孔工藝過程和制孔質(zhì)量的重要影響,尤其是對于易形成熱損傷的鈦合金材料來說,系統(tǒng)研究螺旋銑削過程的力和溫度特征,分析基本切削參數(shù)對其影響的規(guī)律十分必要。
本文分析螺旋銑孑L加工中銑刀端刃和側(cè)刃切削形成切屑的形狀參數(shù)及其與加工參數(shù)之間的關(guān)系,在此基礎(chǔ)上設(shè)計螺旋銑孔切削力和切削溫度在線檢測方案,開展鈦合金材料螺旋銑孑L加工試驗,檢測加工過程中的切削力和切削溫度,對比研究不同參數(shù)下刀具磨損狀態(tài)及加工孔出口形貌,以期明確影響鈦合金螺旋銑孑L加工質(zhì)量的主要因素和規(guī)律,這對理解螺旋銑孔加工機理,確定合理的加工參數(shù)具有指導(dǎo)意義。
1.試驗設(shè)計
1.1加工參數(shù)的選擇
螺旋銑孔原理如圖l所示,刀具中心的軌跡是螺旋線,加工運動由刀具高速自轉(zhuǎn)、刀具繞加工孔中心公轉(zhuǎn)及刀具沿軸向方向直線進給3個運動組合而成喁l。螺旋銑孔的未變形切屑如圖2所示,包括底刃切削形成的連續(xù)切屑及側(cè)刃切削形成的斷續(xù)切屑兩部分。當(dāng)?shù)毒叽_定后,螺旋銑孔未變形切屑的形狀及尺寸由切向每
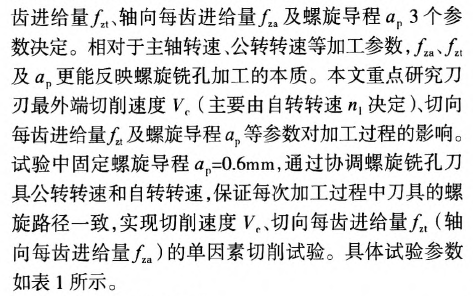
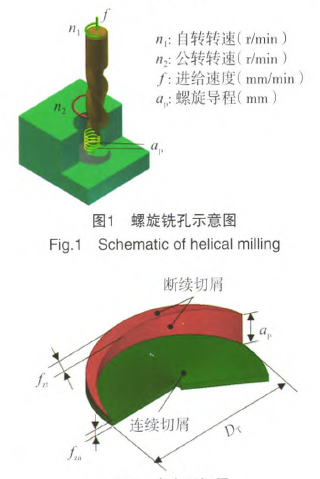
圖2未變形切屑
表1 試驗參數(shù)及切削條件

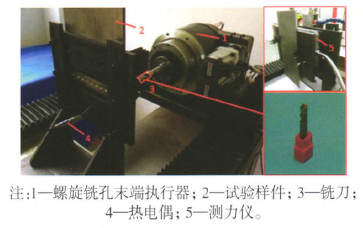
圖3螺旋銑子L裝置
心量為6mm。螺旋銑孔單元安裝于二維工作臺上,二維工作臺可提供軸向和徑向兩個方向的最高進給速度均為500mm/min。所用試驗材料為厚度7mm的Tc4鈦合金板。采用氮化硅納米涂層的鎢鋼立銑刀進行螺旋銑孔試驗,銑刀參數(shù)如表2所示。由于測力儀及熱電偶安裝方式的限制,測溫及測力試驗在加工參數(shù)、刀具及工件材料相同的情況下分別進行。
表2刀具參數(shù)

采用YDCB—III三向測力儀檢測切削力,測得的信號經(jīng)過電荷放大器LN586lA處理后,利用數(shù)據(jù)采集卡PCI9118DG進行數(shù)據(jù)采集。采用標(biāo)準K型鎧裝熱電偶檢測切削溫度,熱電偶直徑0.5mm,熱響應(yīng)時間0.2s,允差等級0.4。熱電偶檢測的信號通過NI uSB一9213測溫模塊放大后,由cDAQ一9174 UsB機箱通過usB數(shù)據(jù)線傳輸給計算機,該測溫模塊具有內(nèi)置冷端溫度補償功能及標(biāo)準熱電偶的電勢一溫度標(biāo)定程序。熱電偶安裝在螺旋銑孔的出口側(cè)直徑0.6mm、深2mm的小孔中,小孔中心與待加工孔中心距6mm,如圖4所示。熱電偶及小孔孔壁的空隙填充導(dǎo)熱膠以提高導(dǎo)熱性。采用如圖5所示的方法標(biāo)定測量點與加工孔孔壁之間溫度差。首先在鈦合金板上加工一個直徑lomm的通孔,在孑L內(nèi)通過過盈配合插入一個紫銅棒,距紫銅棒外緣0.1mm處加工一個直徑0.6mm、深度2mm的小孔。在如圖5(a)所示與之相對的鈦合金孑L壁邊緣位置同樣加工一個直徑0.6mm、深度2mm的小孔。將熱電偶I、熱電偶Ⅱ分別插入紫銅棒及鈦合金的小孑L中,而非絕對值,因此標(biāo)定誤差可以忽略。
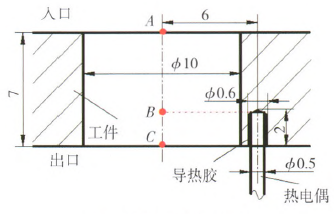
圖4熱電偶安裝示意圖
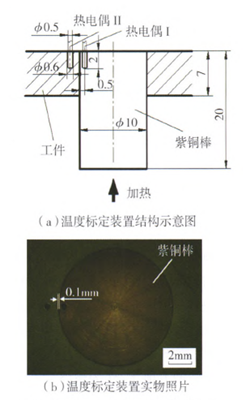
圖5螺旋銑孔切削溫度標(biāo)定裝置
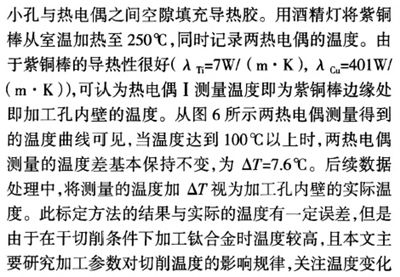
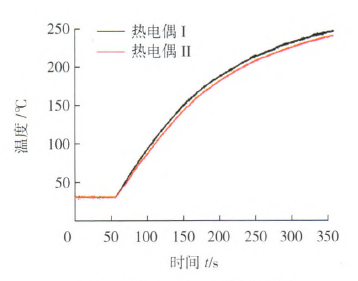
圖6熱電偶I和II測量溫度對比
2.試驗結(jié)果
2.1 典型切削溫度曲線
圖7所示為一條典型的切削溫度隨時間變化的曲線,螺旋銑孔參數(shù)Vc=40lTl/min,.fzt=40μm,ap=o.6mm。在4點以前,切削尚未開始,采集室溫。A曰段曲線對應(yīng)刀具開始切人工件直至切到與熱電偶距離最近的過程。在這一階段,刀具在軸線方向上逐漸接近熱電偶的測溫點,傳人測溫點的熱量不斷增加,使測量溫度逐漸升高直至達到溫度最高值。BC段曲線對應(yīng)刀具切過測溫點直至切出工件的階段,隨著刀具與測溫點在軸向方向的遠離,由于材料不斷被去除,散熱面積增加,散出的熱量大于傳人測溫點的熱量,測量點溫度下降。c點以后的曲線對應(yīng)刀具切出工件后的階段,切削加工停止,工件在空氣中快速冷卻,直至接近室溫。4c段溫度曲線呈現(xiàn)波浪式變化,起伏的幅度隨著切削溫度的增加而增加,波動周期保持恒定為f,。在后續(xù)的數(shù)據(jù)處理中,選取每次采集到的最大值咒作為最終切削溫度。
2.2典型切削力曲線
圖8所示為加工參數(shù)Vc=40m/min,fzt=40μm,
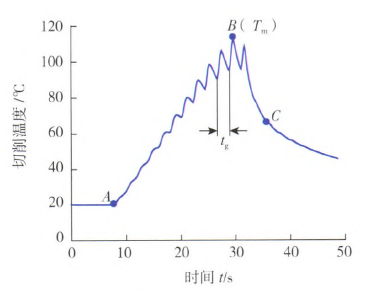
圖7典型切削溫度曲線
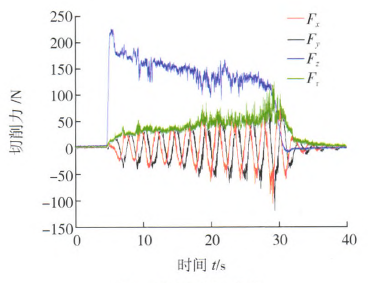
圖8典型切削力曲線
ap=0.6mm時采集到的3向切削力曲線。定義z向為刀具軸線方向,工件表面為xoy平面。由圖8可見,軸向力F:大于徑向力F。及F。。在切削開始時,由于刀具和工件突然接觸,軸向切削力疋由零跳躍至226N,并在接下來的2s左右的時間內(nèi)下降至185N。隨后的穩(wěn)定切削段內(nèi),,,逐漸下降,下降速度約為2.94N,s,直至切出工件。在切削刃切透工件的最后約2s時間內(nèi),軸向切削力快速降低直至為零。在后續(xù)討論中,將圖8中從切削力穩(wěn)定至切削結(jié)束的階段作為有效切削力段,并去除開始2s及結(jié)束前2s中的不穩(wěn)定數(shù)據(jù),分別取該階段的平均值、最大值和最小值作為軸向切削力凡的均值及上下誤差范圍進行對比討論。切向力只、F。在切削開始前為零,在切削周期內(nèi)出現(xiàn)周期性波動,其波動幅值逐漸增加,波動周期為定值,與切削溫度波動周期相同。在整個切削階段,以及每個波動周期內(nèi),B、R大小及變化趨勢一致,但存在0.56s的時間差。測力儀采集到的x方向及y方向切削力在x緲平面內(nèi)互呈90。,將其按式(1)合成得到合力F,,由圖8可見,徑向合力f隨著時間逐漸增加。

在后續(xù)討論中,同樣將切削階段去除不穩(wěn)定階段數(shù)據(jù)作為有效數(shù)據(jù),取該段內(nèi)F的平均值、最大值和最小值作為切向力的均值及上下誤差范圍進行對比討論。
2.3切削參數(shù)對切削溫度及切削力的影響
圖9所示為切削速度及切削溫度對切削力的影響,
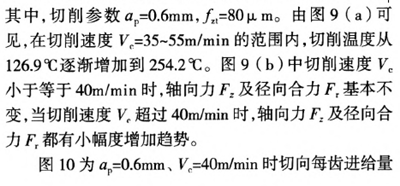
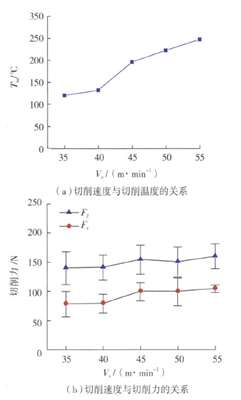
圖9切削速度對切削溫度和切削力的影晌
與切削溫度及切削力的關(guān)系。隨著切向每齒進給量fzt從40μm增加到120μm,切削溫度雖有小的波動,但是基本穩(wěn)定在(125±3)℃,無明顯變化。而軸向力fz及徑向合力f都隨著切向每齒進給量厶的增加而增加,軸向力E變化范圍為128.3~214.9N,徑向合力fr變化范圍52.5~106.2N。
2.4加工孔出口質(zhì)量
切削力及切削溫度直接影響加工孔的質(zhì)量,為探究切削溫度及切削力對加工孔顯微形貌的影響,分別選取最大切削溫度咒兩組參數(shù)及最大軸向力t兩組參數(shù)加工孔出口形貌進行檢測。圖ll為不同加工參數(shù)下孔出口形貌,圖11(a)及圖11(b)加工孔的出口較平整,無明顯缺陷,兩組參數(shù)下的切削溫度丁。分別為120.9cC及131.7℃,軸向力疋分別為164.8N及214.9N;而圖11(c)及圖11(d)出口的表面形貌較差,有明顯的飛邊、毛刺現(xiàn)象,切削溫度r。分別為229.2cc及254.2℃,軸向力F:分別為150.8N及160.5N。對比可知,加工孔的出口質(zhì)量對切削溫度比較敏感,而切削力對其影響較小,切削溫度越高,加工孔的出口質(zhì)量越差。
2.5刀具形貌
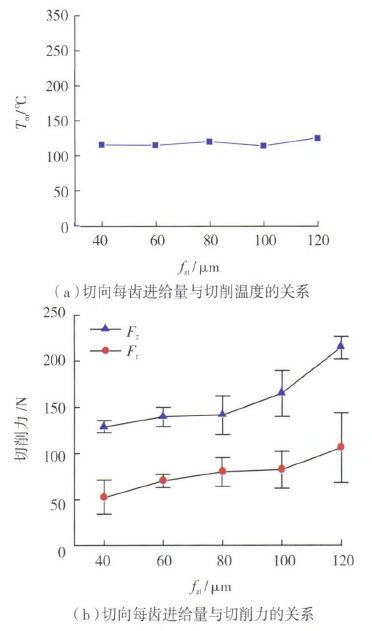
圖10切向每齒進給量對切削溫度和切削力的影響
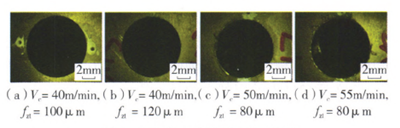
圖1 1 不同加工參數(shù)下孔出口形貌
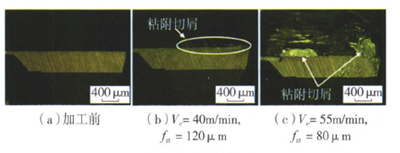
圖12刀具形貌
不同參數(shù)下切削后的刀具形貌如圖12所示。圖12(a)為加工前刀具形貌圖,切削刃完好無破損。采用Vc=40μm,fzt=120μm加工后的刀具形貌如圖12(b)所示,此時的切削溫度為131.7℃,軸向力為214.9N。
刀刃最外側(cè)粘附有微量切屑,切削刃沒有大的破損及堵塞現(xiàn)象,仍有很好的切削能力,孔出口處的材料很容易被切斷,出口質(zhì)量較好。圖12(c)為加工參數(shù)為y,=55m/min,正。=80斗m時刀具形貌圖,此時的切削溫度為254.2℃,可以看出整個刀刃粘附有大量切屑.此時刀具已失去切削能力。
3.討論
從圖7和圖8所示的切削溫度和切削力可見,兩者都存在波動,且波動周期一致,與螺旋銑孔加工中公轉(zhuǎn)周期相同。螺旋銑孔加工中測溫點溫度變化取決于從切削點傳來的熱量,以及向外散出的熱量。刀具的螺旋公轉(zhuǎn)運動使得切削點距離測溫點的位置周期性變化,使得切削溫度出現(xiàn)波動。這也證明螺旋銑孔相對于傳統(tǒng)鉆孔的優(yōu)勢,螺旋銑孑L的偏心加工方式可以使工件在每個公轉(zhuǎn)周期內(nèi)散熱,降低工件溫度,這在加工導(dǎo)熱性差的鈦合金及導(dǎo)熱情況復(fù)雜的復(fù)合材料時避免了熱損傷,具有很大的優(yōu)勢。
由圖8可見,隨著螺旋銑削加工的進行,徑向切削力Fx、Fy的峰值逐漸變大,這是因為所用銑刀側(cè)刃部分高度為10mm,大于工件厚度,因此在整個螺旋銑孑L加工過程中,隨著刀具的軸向進給,與孑L壁直接作用的側(cè)刃長度一直在增加,側(cè)刃與孔壁之間的切削力和摩擦力逐漸增加。在此階段內(nèi),只、F.大小及變化趨勢一致,存在0.56s的時間差,與公轉(zhuǎn)轉(zhuǎn)速對比可知,上述時間內(nèi)刀具相對孔中心轉(zhuǎn)過90。角,即兩徑向力只、F。之間存在90。的相位差。在切削過程中銑刀端刃的切削厚度和速度均保持相同,但可見軸向切削力由最大值逐漸降低,與文獻[21]中的切削力信號一致。結(jié)合切削溫度檢測結(jié)果分析,隨著切削的進行,切削區(qū)域溫度逐漸升高,這可能導(dǎo)致鈦合金材料軟化,使銑刀底端橫刃的切削變得輕快,導(dǎo)致軸向切削力降低。
從圖9可知,切削速度l,,對切削溫度丁。的影響較大而對切削力的影響較小。由文獻[4】知,當(dāng)切削速度y,增加時螺旋導(dǎo)程口。、軸向每齒進給量.正。、切向每齒進給量.丘。不變,整個未變形切屑的形狀及尺寸都保持不變,但是單位時間內(nèi)刀具與切屑及已加工表面的摩擦次數(shù)增加,做功增加,摩擦產(chǎn)熱大幅度增加,熱量來不及擴散,流人工件內(nèi)的熱量增加,使得測量溫度丁。升高。同時,增加切削速度y。.時,切削溫度n增加,材料軟化,切削阻力減小,切削力減小。但是在干切削條件下,加工條件比較惡劣,當(dāng)切削溫度增加到一定值時,切屑流動性變差,造成排屑槽堵塞,如圖12(c)所示刀刃的切削能力降低,部分材料靠刀具擠壓去除,使得軸向力t及徑向合力f都增加。
從圖10(a)及圖lo(b)可知,切向每齒進給量fz1對于切削力的影響較大而對切削溫度幾乎沒有影響。這是因為切削速度y,不變時,單位時間內(nèi)摩擦產(chǎn)熱基本不變。當(dāng)切向每齒進給量.厶及軸向每齒進給量.正。增加,底刃及側(cè)刃的切削厚度增加,未變形切屑變厚,切屑變形脫離工件所做的功增加,導(dǎo)致總切削產(chǎn)熱增加;但另一方面,由L0ewen和MC Shaw于1954年提出切削溫度解析方法口21可知,當(dāng)切削厚度增加時,切屑剪切變形產(chǎn)熱流入切屑的比例月。增大,流人工件的比例1一月。減小,切削熱絕大部分由切屑帶走,以上兩方面的影響使得傳人工件的熱量基本不變,測量溫度基本不變。
由圖9(b)及圖10(b)可見,軸向力F大于徑向合力F,這是因為在螺旋銑孑L過程中,同時存在底刃的連續(xù)鉆削及側(cè)刃的斷續(xù)銑削兩種加工形式,以銑削和鉆削方式去除材料的體積之比(R)可由式(2)計算。計算可知本試驗中銑削作用和鉆削作用的比例為4,9,鉆削比銑削的貢獻大,從而使軸向力E大于徑向合力F。

切削溫度對刀具狀態(tài)和鈦合金孑L出口質(zhì)量有重要影響。溫度過高時使鈦合金切屑軟化,容易滯留在排屑槽中,甚至粘附于前刀面,導(dǎo)致切削刃的切削能力減弱,孔出口處的一部分材料靠刀具的擠壓去除,所以在出口處出現(xiàn)飛邊及毛刺現(xiàn)象。較高的切削溫度不僅降低加工孔的質(zhì)量,同時也影響刀具的使用壽命。
4.結(jié)論
開展了鈦合金螺旋銑孔試驗研究,分析了加工參數(shù)對切削力、切削溫度及制孑L質(zhì)量的影響,得出以下主要結(jié)論。
(1)在螺旋銑孑L加工過程中,測量點的溫度由于傳熱與散熱相互影響而先上升后下降,局部溫度曲線呈周期性波動,波動周期即為刀具公轉(zhuǎn)周期。
(2)螺旋銑孔加工中F。、E隨刀具的公轉(zhuǎn)呈周期性波動,在每個周期內(nèi),只、F。大小及變化趨勢一致,但存在900的相位差。
(3)切削速度增加時,切削溫度明顯上升,切削力基本保持不變;軸向每齒進給量及切向每齒進給量增加,切削溫度無明顯變化,切削力上升。切削溫度是影響鈦合金加工孔表面質(zhì)量的主要因素。切削溫度高,切屑流動性變差,容易粘附在排屑槽中堵塞刀具,降低刀具的切削能力,導(dǎo)致在工件表面出口處有大量毛刺存在,降低加工孔的質(zhì)量。
(4)在需同時保證加工效率及加工質(zhì)量的前提下,應(yīng)盡量選擇大的切向每齒進給量、大的軸向每齒進給量和較低的切削速度。
投稿箱:
如果您有機床行業(yè)、企業(yè)相關(guān)新聞稿件發(fā)表,或進行資訊合作,歡迎聯(lián)系本網(wǎng)編輯部, 郵箱:skjcsc@vip.sina.com
如果您有機床行業(yè)、企業(yè)相關(guān)新聞稿件發(fā)表,或進行資訊合作,歡迎聯(lián)系本網(wǎng)編輯部, 郵箱:skjcsc@vip.sina.com
更多相關(guān)信息
業(yè)界視點
| 更多
行業(yè)數(shù)據(jù)
| 更多
- 2025年5月 新能源汽車銷量情況
- 2025年5月 新能源汽車產(chǎn)量數(shù)據(jù)
- 2025年5月 基本型乘用車(轎車)產(chǎn)量數(shù)據(jù)
- 2025年5月 軸承出口情況
- 2025年5月 分地區(qū)金屬切削機床產(chǎn)量數(shù)據(jù)
- 2025年5月 金屬切削機床產(chǎn)量數(shù)據(jù)
- 2025年4月 新能源汽車銷量情況
- 2025年4月 新能源汽車產(chǎn)量數(shù)據(jù)
- 2025年4月 基本型乘用車(轎車)產(chǎn)量數(shù)據(jù)
- 2025年4月 軸承出口情況
- 2025年4月 分地區(qū)金屬切削機床產(chǎn)量數(shù)據(jù)
- 2025年4月 金屬切削機床產(chǎn)量數(shù)據(jù)
- 2025年1月 新能源汽車銷量情況