刀具表面織構對刀-屑界面摩擦學特性的影響
2020-2-27 來源:河南科技學院 機電學院 作者:逄明華,聶永芳,申福猴,馬利杰
摘要:刀具快速磨損限制了金屬切削的進一步發展,表面織構技術的提出為改善刀-屑界面摩擦提供了新思路,也是目前降低刀具表面磨損的有效方法之一。從刀-屑界面切削液存儲與潤滑、微/納織構、織構方向、織構類型及形狀、織構位置等五個方面,概述了現有刀具表面織構對刀-屑界面摩擦學特性的影響,總結了刀具表面織構的共性作用機理,并進行了分類歸納。相應分析結果表明,刀具表面織構改變了刀-屑界面內空體集團的數量及微通道分布,增加了界面內切削液的滲入存儲,同時捕捉存儲了界面內的磨屑顆粒,改善了刀-屑界面潤滑摩擦;且在此過程中,潤濕性因素對界面內切削液的滲入、存儲及潤滑油膜的形成等均存在影響。最后對刀具表面織構技術的發展進行了總結與展望,為刀具表面磨損的調控提供了參考。
關鍵詞:刀具;表面織構;刀-屑界面;摩擦學特性;潤濕性
金屬切削過程中,刀具與工件之間的惡劣摩擦以及切削熱的協同作用會引發刀具的快速磨損,尤其在高速切削難加工材料時,切削環境更為惡劣,刀具耐用度更低。此外,刀-屑界面摩擦也是刀具切削能量損耗的主要因素之一,因此,減小刀-屑界面摩擦是實現高效、綠色切削的關鍵。切削液的使用改善了刀-屑界面摩擦,降低了刀具的切削溫度及能耗,究其原因為切削液滲入刀-屑界面,帶走了大量的切削熱,同時又改善了界面潤滑。
目前常用的切削液供給方式為澆注式,盡管該方式的切削液用量很大(10~20 L/min),然而切削液僅能冷卻潤滑刀-屑界面滑移區,在高速切削難加工材料時,切削液對刀-屑界面的冷卻潤滑基本不存在。為此,增加刀-屑界面切削液的滲入,改善界面冷卻及潤滑,降低刀具磨損,對于提高刀具壽命和降低切削能耗均具有重要的意義。
表面及界面直接影響機械設備的能量交換、運動和信號傳遞,早在 1942 年 SCHLESINGER 就指出“表面的質量對于其正確的功能極其重要”[18-19]。這表明設計者們已意識到表面形態的重要性,并試圖通過改變表面的紋理或織構來改善表面機械、物理及化學性能。為此,表面織構技術被提出并應用于工程表面。表面織構是指利用電沉積、電火花、激光及光刻等加工方法在平整材料表面加工出具有一定排列規律和形狀參數的微細結構,從而得到具有某種特定性能的非光滑表面[18]。現有研究表明表面織構能夠存儲潤滑 液及容納磨屑,從而改善界面潤滑、摩擦,提高其承載能力],已逐漸成為國內外學者研究的熱點。近年來表面織構被應用于刀具表面,以此改善刀-屑界面的潤滑及摩擦,減緩刀具磨損。目前學者們采用激光等加工方法在刀具表面制備了微/納米級織構,研究了織構類型、形狀及參數等對刀-屑界面潤滑摩擦、刀具切削力及工件表面加工質量等的影響。
結果表明,刀具表面織構能夠改變刀-屑界面切削液的滲入及存儲,改善界面潤滑及摩擦,降低刀具的切削力,提高工件表面加工質量。 盡管刀具表面織構的相關機理研究已取得較大進展,然而刀-屑界面作用劇烈,織構效果無法直接觀察及測量,致使其內部機理還未完全清晰。鑒于國內刀具表面織構的作用機理綜述較少,為此,本文從表面織構對刀-屑界面潤滑摩擦的影響出發,綜述了現有的研究成果,提取了刀具表面織構的內部共性機理,同時對刀具表面織構技術的發展進行了總結與展望,為改善刀具的切削性能,降低切削能耗奠定理論基礎。
1、表面織構常用加工方法
表面織構是指借助于加工設備和技術手段,在固體表面生成具有相應規律和尺寸的微小結構(如圖 1所示),以此提高表面或界面性能。隨著表面織構技術的不斷發展及應用領域的推廣,加工方法逐漸豐富,常用加工方法如表 1 所示。

圖 1 固體表面織構形貌
表 1 表面織構常用加工方法
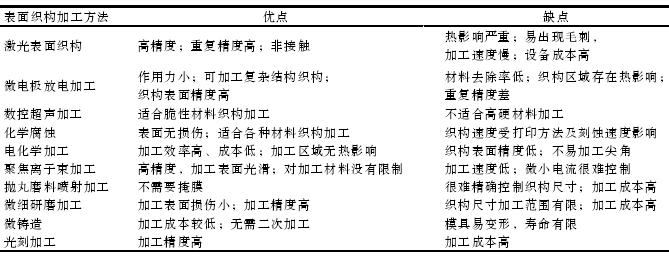
2、表面織構對刀-屑界面摩擦學特性影響
表面織構能夠改善刀具的切削性能,澄清表面織構的作用機理是設計織構刀具的前提,綜述現有的研究成果是系統化機理的基礎。目前機械表面織構的四大機理已基本得到歸納、總結和驗證,而刀具表面織構技術出現時間較晚、研究不多,從刀-屑界面切削液滲入及潤滑摩擦影響方面進行機理綜述目前鮮有報道。為此,本文從刀-屑界面切削液存儲與潤滑、微/納織構、織構方向、織構類型及形狀、織構位置等五個方面,綜述了現有刀具表面織構對刀-屑界面摩擦學特性影響的研究結果,并以此為基礎歸納、提取刀具表面織構的共性作用機理。
2.1 刀-屑界面切削液存儲與潤滑
表面織構引入刀具表面,改變了刀-屑界面的接觸特性,影響了切削液在界面內的滲入,從而改善了刀-屑界面潤滑及摩擦。KAWASEGI 等利用飛秒激光技術在 WC/Co 硬質合金刀具表面加工了微米(深1.3 μm、寬 2.2 μm)和納米(深 150 nm、寬 800 nm) 溝槽(見圖 2),并進行了鋁合金(A5052)車削實驗。結果表明,微量切削液潤滑條件下,刀具表面織構增加了刀-屑界面內切削液的滲入及存儲,減小了刀-屑界面摩擦與粘結,進而降低了刀具的切削力。ENOMOTO 等利用鈦寶石飛秒激光加工技術在硬質合金(K10)刀具表面加工了微/納米溝槽陣列織構(深度 100~150 nm、間隔 700 nm),端面銑削鋁合金實驗表明,濕切削條件下,微/納溝槽織構刀具的抗粘附特性得到明顯改善,其原因為刀具表面織構的“儲油”特性。
隨后,ENOMOTO 等[37-42]又進行了微/納米織構刀具切削碳素鋼實驗,結果發現納米級織構刀具的減磨效果不如微米級織構刀具。其原因為,當織構刀具切削軟金屬時,微米級織構尺寸較大,切屑很容易陷入刀具表面,因此刀-屑界面抗粘結特性改善較??;而納米級織構尺寸較小,切屑很難陷入刀具表面,因此刀具抗粘結特性提高明顯。當織構刀具切削硬金屬材料時,刀具切削力較大,而刀-屑界面粘結較輕,故潤滑對金屬切削過程的影響更明顯。納米級織構尺寸較小,切削液的滲入及存儲能力較差,故潤滑能力有限;而微米級織構尺寸較大,切削液的滲入及存儲能力較強,因此,微米織構的減磨效
果優于納米織構。
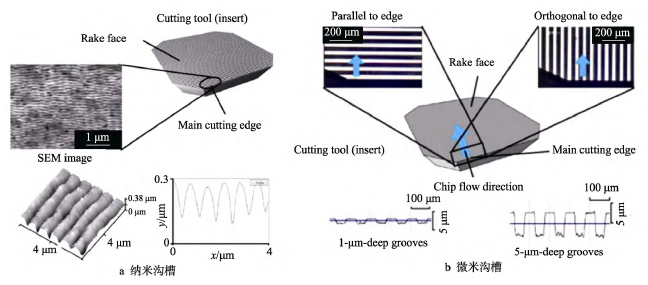
圖 2 刀具表面微/納溝槽織構
LEI 等在鈦合金刀具(WC)前刀面加工了錐形凹坑織構(見圖 3),45#鋼切削實驗表明,濕切削條件下,刀具表面錐形凹坑織構降低了刀具的切削力及刀-屑界面接觸長度,同時也改變了切屑的形態。其原因為刀具表面織構增加了刀-屑界面切削液的滲入存儲,改善了界面潤滑摩擦,從而降低了刀-屑接觸長度及刀具切削力。
ZHANG 等 對不同潤滑狀態下刀具表面織構的效果進行了對比研究。結果表明,在潤滑油充足的情況下織構的減磨效果最好,在乏油潤滑狀態下織構的減磨效果變差。主要原因為潤滑液充足時,刀具表面織構能夠存儲更多的切削液,進而更好地冷卻潤滑刀-屑界面,降低刀具的切削力。國內的戚寶運等利用激光打標機在鎢鈷類硬質合金刀具(YG8)表面加工了凹槽織構(寬 27 μm、深 12 μm、間距 100 μm),鈦合金切削實驗表明,濕切削條件下,刀具表面織構改善了刀-屑界面摩擦及粘結,降低了刀具的切削力及溫度。
其原因為表面織構增加了切削液的滲入,改善了界面潤滑與摩擦。楊超等 在硬質合金刀具(WC/Co)表面加工了圓形離散凹坑織構(直徑 80~ 200 μm、深 7 μm、織構面積比10%~30%),并進行了 45#鋼切削實驗。分析發現,刀具表面織構增強了切削液的鋪展及存儲,改善了刀-屑界面潤滑及摩擦,進而降低了刀具的切削力。由上述研究結果可得刀具表面織構有兩個作用:首先,刀具表面形貌是刀-屑界面微通道的來源,而刀具表面織構的存在影響了界面內微通道的存在、分布及幾何尺寸等,改變了界面內切削液的滲入;再者,切屑沿刀具前刀面快速滑移,帶走了界面內已滲入的切削液,而刀具表面微凹坑單元能存儲切削液,并提供二次潤滑。
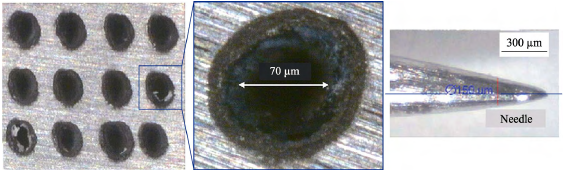
圖 3 刀具表面錐形凹坑織構
2.2 微/納米尺度織構
織構尺寸對表面織構的效果有顯著影響,合理調控 織構的尺度能明顯提高刀具的切削性能。KAWASEGI等對微米/納米級織構硬質合金刀具的抗粘結特性進行了對比研究,鋁合金(A5052)切削實驗結果表明,微米級織構刀具的抗粘結特性較差,而納米級織構刀具的抗粘結特性較好。究其原因為,微米級織構的尺寸較大,鋁合金切屑硬度較小,切削過程中切屑很容易陷入到織構內部,致使刀具表面織構快速被掩埋,刀具切削效果迅速變差。而納米級織構尺寸較小,切屑不容易陷入到織構內部,刀具表面織構不易被掩埋,刀具切削效果較好,其切削后的形貌如圖 4 所示。 在此基礎上,ENOMOTO 等[23,37-42]利用微米/納米級織構硬質合金刀具分別切削了鋁合金(A5052)及碳鋼。結果表明,切削鋁合金時納米級織構刀具的效果較好,而切削碳鋼時微米級織構刀具的效果較好。究其原因為,切削鋁合金(A5052)時,切屑是否陷入刀具表面是影響刀具效果的主要因素;而切削碳鋼時,刀具表面切削液的存儲能力至關重要。這表明刀具表面織構尺寸對刀具切削效果影響明顯,當切削硬度較高的金屬材料時,刀具表面織構的尺度不易太小;而切削軟金屬時,刀具表面織構的尺度不易太大。
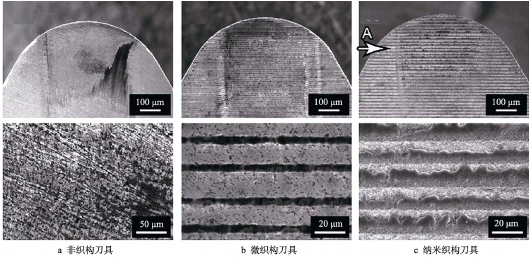
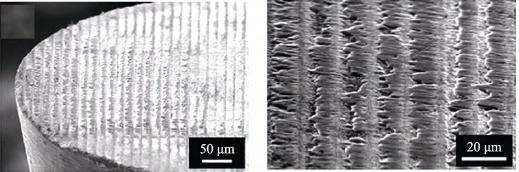
圖 4 金屬切削后刀具表面 SEM 形貌
2.3 刀具表面織構方向
表面織構能夠增加切削液在界面內的滲入存儲,那么溝槽織構的方向就不能忽略。溝槽織構的方向不僅決定界面內切削液的滲入情況,也決定切屑與界面內切削液之間的相互作用。KAWASEGI 等 的研究結果表明,溝槽織構方向對刀具的切削性能有著重要的影響。其中,垂直切屑流出方向的溝槽織構刀具效果最佳,其原因為該方向的溝槽能有效保持滲入的切削液,并形成良好的潤滑(見圖 5 所示)。ENOMOTO等[23,40]的研究結果表明,平行主切削刃方向的微/納米溝槽織構刀具的抗粘結性能最好。OBIKAWA 等利用光刻方法在硬質合金刀具(K10)表面制備了垂直/平行凹槽陣列、方凸/凹陣列,并涂覆了 DLC 涂層。干/濕狀態下的鋁合金(A5052)切削實驗表明,刀具表面平行切削刃方向的溝槽織構潤滑減磨效果最優。由此表明刀具表面溝槽織構方向對刀具的切削效果影響明顯,其中平行切削刃方向的織構刀具效果最佳。
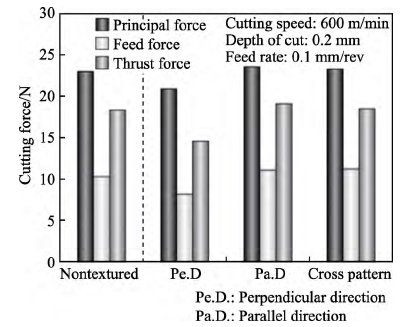
圖 5 刀具表面溝槽織構方向與切削力關系
2.4 刀具表面織構類型及形狀
織構類型及形狀是表面織構的一個常用表征參數,目前刀具表面織構類型及形狀的研究較少,僅限于溝槽、離散凹坑等織構類型。KOSHY 等利用電火花加工技術在刀具的前刀面加工了離散和連續兩種織構類型(見圖 6 所示),并對其效果進行了研究。結果分析發現,兩種類型織構均促進了切削液在刀-屑界面內的滲入,改善了刀-屑界面摩擦,降低了刀具的切削力,但其作用效果存在差異,面織構的效果優于離散織構。而 OBIKAWA 等[48]的研究結果表明,平行切削刃方向的溝槽織構及正方形凸織構的潤滑減磨效果最優。從上述結果可以看出,織構形狀確實對刀具表面織構的效果存在影響。根據 KOSHY 的研究結果可判定,面織構的效果好于離散織構,而離散織構中溝槽與方/圓陣列織構的效果各有其特點。溝槽織構在其切削液供給方面更具有優勢,而離散方/圓陣列織構在界面流體動壓承載方面更具優勢]。
這表明研究刀具表面織構的作用機理時,織構形狀因素應該給予考慮,合理選擇織構類型及形狀能更好地發揮刀具表面織構的效果。
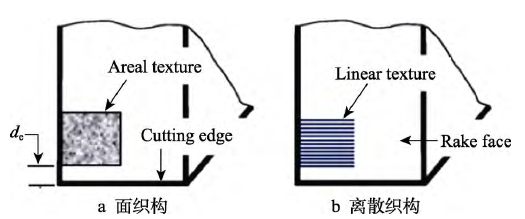
圖 6 刀具表面織構
2.5 刀具表面織構位置
織構加工在刀具表面上時,織構在刀具表面的位置就成為織構加工中必不可少的一個參數,其中織構區域相對刀具主切削刃的距離是最重要的參數之一,直接影響織構刀具的效果(甚至使刀具表面織構呈現反效果 。刀具切削過程中,刀-屑界面接觸長度一般很?。s 1 mm 左右,具體與工件材料、切削參數 等因素相關 ) , 且又分為兩 區—粘結區(1/2~2/3)與滑移區(1/3~1/2)。在粘結區內,刀-屑界面具有較高的應力(1 GPa)、溫度(700~1200 ℃)及化學活性,且界面材料相互粘結。在滑移區內,刀-屑界面應力、溫度及化學活性大大降低,界面材料相對滑動,僅在峰點接觸處才存在粘結現象[4-5]。刀-屑界面粘結區內切削液不能進入 ,刀具表面織構也不能改變該區切削液的滲入,相反還容易造成刀具表面織構的切屑嵌入,增大了界面的相互作用(見圖 7)。
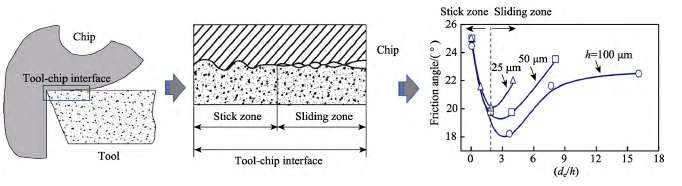
圖 7 刀-屑界面接觸特性及織構區域位置
為此,KOSHY 等研究了織構的位置對刀具切削效果的影響,研究發現當織構位置距離刀具切削刃 2~3倍進給量時,刀具表面織構的效果最優。究其原因為織構的位置直接影響刀-屑界面內切削液的滲入及潤滑油膜的形成,織構區域距離刀具的主切削刃太近,這不但不能形成潤滑油膜,反而增加了界面粘結。OBIKAWA 等[48]的研究結果表明,刀具表面織構位置對織構效果有明顯的影響,當織構區域距刀具主切削刃 100 μm 時,織構刀具的切削效果最好。目前關于刀具表面織構位置的研究結論見表 2
表 2 刀具表面織構區域相對主切削刃的最優位置

3 、刀具表面織構共性作用機理
刀具切削過程是一個多因素耦合的復雜系統,在此系統中,刀具表面形貌與刀-屑界面切削液的滲入、潤滑效應、界面接觸力學行為及刀-屑界面摩擦相互關聯。切削液的滲入途徑為界面微通道,而微通道的來源為刀具表面形貌的刮擦和犁耕作用??棙嫺淖兞说毒弑砻娴男蚊?,影響了刀-屑界面切削液的滲入存儲、潤滑效應,進而影響刀-屑界面摩擦。
3.1 刀-屑界面切削液滲入存儲
刀具切削過程中,冷卻潤滑對刀具切削力及刀具表面磨損具有重要的影響,尤其在高速切削難加工材料時,潤滑比冷卻更為重要[9,10,32]。刀具表面織構能影響刀-屑界面切削液的滲入存儲,改善界面潤滑及 摩擦。由圖 8 可以看出,刀具表面織構影響了刀-屑界面內空體集團的數量及分布,更多的切削液能進入界面內,從而改善了界面潤滑及摩擦。而刀具表面織構的形狀及參數又與刀-屑界面內空體集團的數量及分布改變程度相關,所以合理設計刀具表面織構的形狀及參數能提高刀具的切削性能。再者,由刀-屑界面原位觀測得出,切削液不能進入界面粘結區[53-54],此區域內的織構雖然改變了刀具表面的拓撲結構,但不能增加切削液的滲入,并且還加重界面粘結,增加了刀具的切削力及刀-屑界面摩擦。對于刀具表面溝槽織構,該織構類型為切削液滲入提供了微通道途徑,也增加了界面內切削液的存儲。而切屑與刀具前刀面存在相對運動,垂直切屑流出方向的溝槽織構其內部的切削液能形成流體動壓效果,改善界面內的潤滑[23,36,40]。為此,與切屑流出方向垂直的刀具表面溝 槽織構效果最好,而與切屑流出方向平行的刀具表面溝槽織構效果較差。綜上分析,在刀-屑界面滑移區合理設計織構類型、參數及位置,能有效增加界面內切削液的滲入及存儲,進而在切屑滑移時形成流體動壓,改善刀具的切削性能。
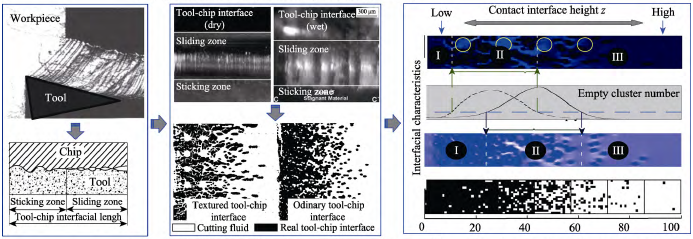
圖 8 刀-屑界面切削液滲入機理及與空體集團數量的關聯
3.2 刀-屑界面織構磨屑存儲
切屑沿刀具前刀面滑移時,刀具表面微結構對切屑有劃擦和犁耕作用,此時界面內必然產生大量的磨屑,致使界面潤滑及摩擦惡化 。刀具表面織構能夠儲存和容納磨屑[22-23],減少了界面內磨屑的數量;此外,表面織構還能夠減少摩擦副間的實際接觸面積,降低界面間的粘著摩擦、磨損,如圖 9 所示。
3.3 織構表面潤濕性對刀-屑界面潤滑的 影響
切削液與刀-屑界面的物理/化學吸附是界面潤滑、減磨的基礎,潤濕性直接影響微通道內切削液的 滲入、存儲及界面油膜的形成。楊超等[34]的研究結果表明,刀具表面織構能夠影響切削液的鋪展,織構表面切削液的鋪展速度越快,刀-屑界面的潤滑效果越好,刀具切削力越低,表明織構刀具表面的潤濕性與刀具切削性能存在關聯。宋曉路等[55-56]的研究結果表明織構刀具表面的潤濕性對刀具切削性能存在影響,微量切削液潤滑條件下,無織構刀具的表面磨損嚴重,并出現了冷焊現象。親油微/納織構表面的引入減緩了刀具表面磨損,而疏油微/納織構表面的引入則進一步降低了刀具表面磨損。究其原因為親油微/納織構能增加刀-屑界面內切削液的滲入及存儲,改善界面潤滑及摩擦;而疏油微/納織構能進一步加快切削液在刀-屑界面內的聚集速度,使刀-屑界面的潤滑狀態由邊界潤滑轉化為流體潤滑,如圖 10。由此可知,表面形貌、潤濕性、界面微通道及切削液鋪展等因素相互耦合并存于刀-屑界面,為此,澄清刀具表面織構的作用機理必須從宏觀系統的角度來澄清它們之間的耦合作用。
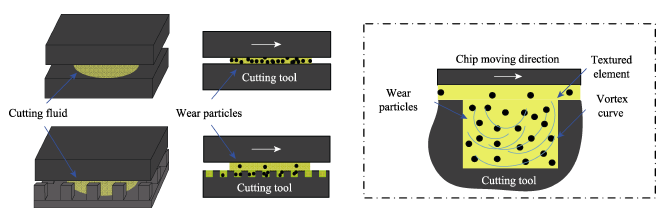
圖 9 刀-屑界面織構磨屑存儲機理
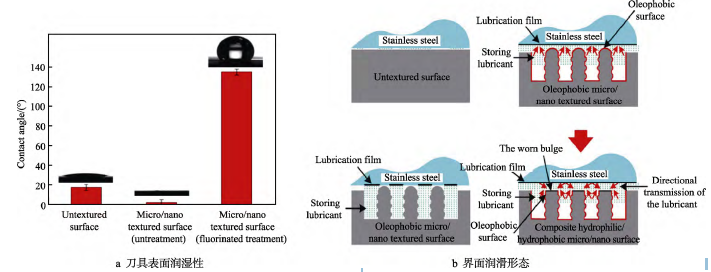
圖 10 刀具表面織構潤濕性與界面潤滑形態關聯機理
4 、結論與展望
表面織構技術的提出為改善刀-屑界面摩擦提供了新思路,成為目前降低刀具磨損的有效方法之一。實際刀-屑界面不能直接觀察及測量,致使刀具表面織構的具體作用機理不夠清晰,這限制了該技術的發展。基于刀-屑界面潤滑摩擦的表面織構影響研究結果及共性機理分析,在此指出刀具表面織構技術的未來發展方向,為刀具表面織構技術的發展提供參考。
1)潤濕性直接影響界面內流體的滲入、潤滑及界面摩擦學特性,而在目前摩擦學的研究中往往忽略了該因素的影響。將潤濕性與刀具表面形貌、界面內液體滲入及潤滑摩擦相結合去闡明表面織構的作用機理更具有實際意義。
2)刀具切削過程是一個多因素耦合的復雜系統,刀具表面形貌影響刀-屑界面切削液的滲入、潤滑效應及界面接觸力學行為,進而影響刀-屑界面摩擦。為此,刀具表面織構的研究必須放入到刀具切削系統中,建立數學及計算機動態模擬模型,從系統的角度去分析刀具表面織構的機理,優化表面織構參數。
3)應采用定量探索與定性分析相結合的方法去研究典型耐磨表面織構的耐磨機制及影響規律,建立刀具表面織構的仿生評價依據和量化計算模型,從而定量評價刀具表面織構的效果。
投稿箱:
如果您有機床行業、企業相關新聞稿件發表,或進行資訊合作,歡迎聯系本網編輯部, 郵箱:skjcsc@vip.sina.com
如果您有機床行業、企業相關新聞稿件發表,或進行資訊合作,歡迎聯系本網編輯部, 郵箱:skjcsc@vip.sina.com