數控滾齒機滾刀主軸振動特性研究(下)
2018-10-15 來源:(重慶機床(集團)有限責任公司 作者:李先廣 楊勇
3、滾齒機滾刀主軸振動測試數據分析
通過對滾齒機滾刀主軸振動測試信號提出與分析,獲得主軸結構時域、頻域響應數據,并根據振動加速度數據獲得主軸 X 向振型或振動位移數據。為了對表 1 與表 2 中理論數據進行對比分析,對應提取與分析了第 1、3 及 5 階振動測試響應特性數據曲線。
3.1 滾齒機主軸振動頻率響應分析
根據滾刀主軸振動試驗信號,提取前 5 階振動頻率值、振動加速度及振動位移響應特性數據。前5 階振動頻率值如表 4 所示。

表 4 滾刀主軸前 5 階振動頻率
由表 4 可知,滾刀主軸前 5 階振動頻率,均大于或偏離滾刀主軸工作轉速對應諧次激振頻率(滾刀參數:單頭滾刀,槽數為 10;工作轉速 40 r/min對應一諧次頻率為: 1×(40×1×10)÷60=6.67 Hz,二諧次頻率為:2×(40×1×10)÷60=13.33 Hz,同理可得三諧次頻率為:20 Hz,四諧次頻率為:26.67 Hz,五諧次頻率為:33.33 Hz;通常情況下,滾齒機工作轉速遠低于最高轉速,則不考慮最高轉速對應激振頻率),表明主軸設計結構不會出現共振現象,剛度滿足工程設計要求,且有優化減重空間。
3.2 振動加速度響應分析
由圖 8 可知,當滾齒機工件滾切深度ht =45 mm,主軸轉速5n =40 r/min,且均固定不變時,滾刀主軸各階振動加速度隨著滾齒時間均呈等幅值周期性變化,滾刀主軸在 X 方向出現左右擺振,表明滾齒加工中滾刀與工件的摩擦切削嚙合,對滾刀主軸振動響應是以周期性動態激勵為主要影響。由圖8 有,滾刀主軸第 1 階最大加速度幅值約為 66.8 m·s?2,第 3 階最大加速度幅值約為 181.8 m·s2,第 5 階最大加速度幅值約為 184.5 m·s?2。 根據表 2 與圖 8 可得,由滾刀主軸最大振動加速度幅值理論模型計算與測試對比數據的表 5 可知,理論與測試值間的相對誤差均小于 5%,即理論計算與測試值的一致性較好,驗證了該型號滾齒機滾刀主軸振動加速度響應理論推導模型的正確性,該方法為其他系列滾齒機主軸振動特性理論與試驗研究提供經驗借鑒與參考作用。 為了深入分析主軸振動特性,將主軸振動測試的加速度值與滾齒轉速建立了加速度-轉速關系曲線。由圖 9 可知,當滾切深度ht =45 mm 且固定不變時,齒輪加工初期與低轉速情況下滾刀主軸振動加速度較大;并且隨著轉速與振動階次的增加,主軸各階振動加速度均呈周期性波動逐漸減小,前期波動幅度較大,最后直至趨于平穩。而在滾齒機低轉速切削時,主軸出現顫振現象,對齒輪加工精度與質量具有較大影響,明滾齒機在低轉速加工初期振動響應影響極為顯著。當ht =45 mm,5n =10 r/min 時,第 1 階最大加速度幅值約為 580.5 m·s2,第 3 階最大加速度幅值約為 1580.5 m·s?,第 5 階最大加速度幅值約為 1604 m·s?2。由此可見滾齒機加工中,高轉速滾削齒輪比低轉速更為穩定.
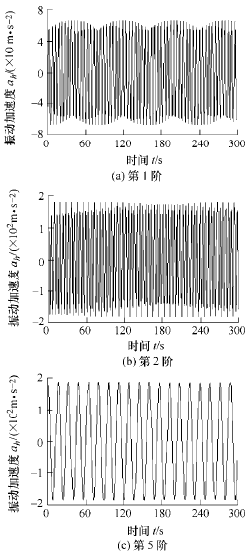
圖 8 滾刀主軸振動加速度-時間關系曲線
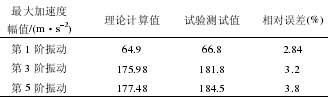
表 5 為滾刀主軸振動最大加速度幅值的理論模型計算與試驗測試對比
由主軸振動測試加速度值與滾齒切削深度的加速度-切削深度關系曲線圖 10 可知,當滾齒機主軸轉速5n 為 40 r/min 且不變時,滾刀主軸振動加速度隨著滾切深度與振動階次增加而增大,主軸各階振動加速度均呈周期性波動逐漸增大,且波動幅度也較大。滾齒機采用大滾切深度切削時,主軸產生顫振現象越嚴重,將對加工精度與質量造成較大影響,表明隨著滾切深度量的增加主軸振動響應影響較為顯著。當ht =150 mm,5n =40 r/min 時,第 1 階的最大加速度幅值達到約 169.4 m·s?2,第 3 階的最大加速度幅值達到約 468.7 m·s?2,第 5 階的最大加速度幅值達到約 478.9 m·s?2。由此可見滾齒機加工中,采用小滾切深度量與多刀次滾削齒輪比大滾切深度量更為穩定。
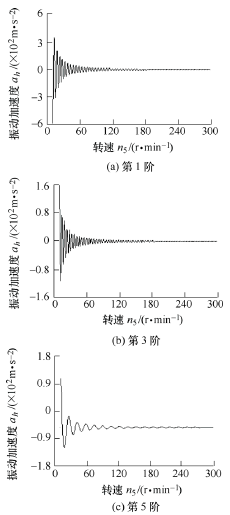
圖 9 滾刀主軸振動加速度-轉速關系曲線
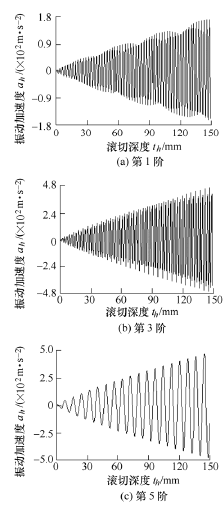
圖 10 滾刀主軸振動加速度-滾切深度關系曲線
3.3 滾刀主軸振動位移響應分析
由圖 11 有,當滾齒機滾切深度ht =45 mm,主軸轉速5n =40 r/min,且均不變時,滾刀主軸 X 方向振動位移隨滾齒時間均呈等幅值周期性變化,滾刀主軸在 X 向呈現左右擺振現象;表明滾齒加工中滾刀與工件摩擦切削嚙合,對滾刀主軸振動響應是以周期性動態激勵為主要影響,但該結構滾刀主軸動平衡效果較好。
由圖 11 可知,當ht =45 mm,5n =40 r/min 時,滾刀主軸第 1 階的最大位移幅值約為 1.086×10-3 mm,第 3 階的最大位移幅值約為 3.6×10?5 mm,第5 階的最大位移幅值約為 4.8×106mm;當滾齒機主軸轉速5n 為 40 r/min,工件滾切深度ht 為 45 mm 時。 由表 1 與圖 11 可得,滾刀主軸振動最大位移幅值的理論模型計算與測試對比數據(表 6);由表 6可知,理論與測試值間的相對誤差均小于 5%,即理論計算與測試值的一致性較好,驗證了該型號滾齒機滾刀主軸振動位移響應理論推導模型的正確性,該方法為其他系列滾齒機主軸振動特性理論與試驗研究提供經驗借鑒與參考作用。
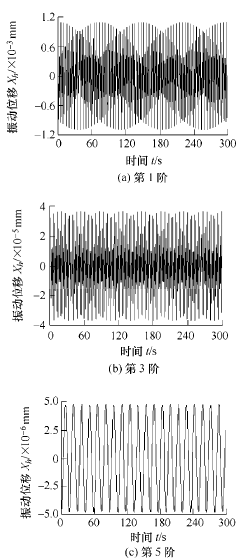
圖 11 滾刀主軸振動位移量-時間關系曲線
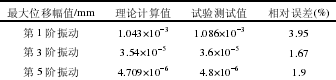
表 6 為滾刀主軸振動的最大位移幅值理論模型計算與試驗測試對比
圖 12 為獲取的機床主軸振動位移與主軸轉速建立了振動位移-主軸轉速關系曲線,當滾切深度ht為 45 mm 且不變時,在齒輪加工初期與低轉速工況下,滾刀主軸振動位移量較大;且隨著轉速與振動階次的增加,主軸振動位移量均呈周期性波動逐漸減小,前期波動幅度較大,最后逐漸趨于平穩且變化量很小,表明該主軸系統幾何精度及動平衡控制較好。
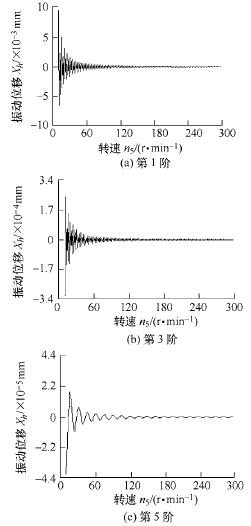
圖 12 滾刀主軸振動位移量-轉速關系曲線
在滾齒機低轉速切削時,主軸出現顫振,振動位移相對較大,對齒輪加工精度與質量將會產生直接影響,表明滾齒機在低轉速加工初期振動響應影響較為明顯。當ht =45 mm,5n =10 r/min 時,第1階的最大位移幅值約為 9.47×10?3 mm,第 3 階的最大位移幅值約為 3.18×10?4 mm,第 5 階的最大位移幅值約為 4.2×10?5 mm。由此可見,滾齒機高轉速滾削加工齒輪比低轉速更為穩定。
圖 13 可知(同理,整理出主軸振動位移量-切削深度關系曲線),當滾齒機主軸轉速5n 為 40 r/min且不變時,滾刀主軸振動位移量隨著滾切深度與振動階次的增加而增大,且波動幅度也較大。滾齒機
采用大滾切深度切削時,主軸顫振現象較為顯著,對齒輪加工精度與質量的影響大,表明隨著滾切深度量的增加主軸振動響應影響較為明顯。當ht =150 mm,5n =40 r/min 時,第 1 階的最大位移幅值約 2.85×10?3 mm,第 3 階的最大位移幅值約9.6×105 mm,第 5 階的最大位移幅值約 1.2×10?5 mm,由此可見滾齒機齒輪加工中,采用小滾切深度與多刀次滾削齒輪比大滾切深度更為穩定,且振動位移量也較小,可降低或減小滾齒位置偏差。
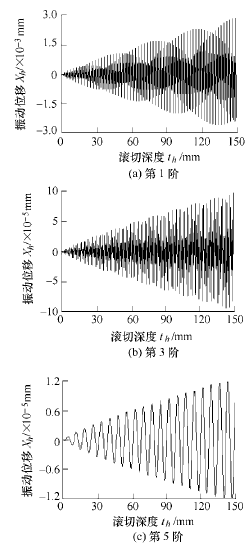
圖 13 滾刀主軸振動位移量-滾削深度關系曲線
由以上分析可知,滾刀主軸在滾齒機低轉速加工初期,將會產生較為嚴重振動現象,但在滾削深度不變情況下振動位移響應逐漸減小,直至趨于平穩。在轉速不變情況下,主軸振動位移隨著滾削深度的增長而呈波動性快速增加。滾刀主軸在 X 方向的左右擺振,使齒輪齒面出現振紋。因此,滾齒加工中,盡量采用大轉速、小滾切量及多刀次切削加工齒輪,使機床主軸振動響應更為穩定,可降低或減少滾齒機振動,從而降低或減少對齒輪加工精度與質量的影響。
4、結論
(1) 采用簡支梁與 Euler-Bemoulli 梁理論,推導出滾齒機滾刀主軸振動加速度與位移響應函數模型,并根據主軸結構與加工工藝參數,可直接計算各振動階次對應的振動加速度與位移數據。
(2) 通過對滾刀主軸振動最大加速度、位移幅值的理論模型計算與測試數據比較分析可知,理論與測試值之間的相對誤差均小于 5%,表明理論與試驗值一致性較好,驗證了該型號滾齒機滾刀主軸振動響應函數理論推導模型的正確性。
(3) 由振動加速度、位移測試數據曲線可知,滾齒機滾刀主軸在 X 方向發生左右擺振,使滾齒切削點產生相應振擺,將造成齒輪齒向、切向或螺旋線錐度誤差。
(4) 經對振動加速度、位移分別同主軸工作轉速、滾削深度的測試數據曲線分析可知,滾齒加工中盡量提高滾刀主軸轉速,降低切削力,采用小滾切深度與多刀次切削加工齒輪,會降低或減少滾齒機振動,從而可降低齒面振紋,確保機床振動響應與加工穩定性,減小或降低機床由振動引起加工誤差,提高齒輪加工精度與質量。
(5) 該研究工作為滾齒機工件主軸振動特性,非接觸式傳感器應用,滾刀主軸與齒輪工件主軸間相對振動特性,以及機床故障診斷等方面問題后期深入、實用性的理論與試驗研究奠定了基礎。
投稿箱:
如果您有機床行業、企業相關新聞稿件發表,或進行資訊合作,歡迎聯系本網編輯部, 郵箱:skjcsc@vip.sina.com
如果您有機床行業、企業相關新聞稿件發表,或進行資訊合作,歡迎聯系本網編輯部, 郵箱:skjcsc@vip.sina.com