高速滾珠軸承電主軸熱態特性分析(下)
2018-10-16 來源: 哈爾濱工業大學深圳研究生院 廣州市昊 作者:姜本剛 雷 群 杜建軍
3 、電主軸熱態特性的有限元分析與試驗
為了便于實驗驗證仿真結果,以 DGZ60E. S 球軸承高速電主軸為研究對象進行 ANSYS 仿真。這款電主軸的前、后軸承均為 FAG hcs7003c 脂潤滑軸承,內置電機為GZ1-060,額定功率為 1. 8 k W,效率為 10% 。
3. 1 電主軸有限元分析模型
電主軸整體上可以看作軸對稱結構,選取其剖視圖的 1 /2 作為熱分析模型,將電機等效為圓柱筒,省略螺釘孔等細微結構。在保證相應結構精度的情況下,簡化后的模型導入有限元分析軟件 ANSYS,選擇 PLANE55 單元,經過處理后的有限元模型如圖8 所示。
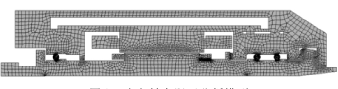
圖 8 電主軸有限元分析模型
3. 2 電主軸溫度場分析
所研究對象為油脂潤滑軸承支承的電主軸單元,則潤滑劑的散熱影響可忽略。在進行電主軸單元的熱仿真分析前,需要進行以下假設:( 1) 電主軸工作環境溫度 Te為 25 ℃ ;( 2) 電主軸選用水冷進行冷卻,冷卻水的流量為 0. 5 L/min,入口水溫 Ti為 20 ℃ ,出口水溫 To根據實驗監測確定為 40 ℃ ,則定性溫度 Tf為 30 ℃ 。表 2 所示為該條件下電主軸的熱邊界條件。
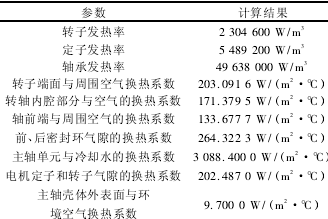
表 2 電主軸單元的熱邊界條件
為了研究穩定的熱載荷對高速電主軸溫度場的影響,需要對電主軸進行穩態熱分析。在進行瞬態熱分析之前一般需要先進行穩態熱分析,以確定電主軸初始溫度分布場或瞬態熱分析最后一步的溫度場分布情況。將表 2 熱邊界條件加載到電主軸的有限元模型,圖 9 所示即為求解所得的電主軸的穩態溫度分布云圖??芍?,電主軸穩態溫度最高點出現在內置電機轉子靠近定子一側區域的中間部分,為 63. 890 4 ℃ ,同時可以通過比較計算得到電主軸整體最高溫升高達38. 890 4 ℃ ,這是由于電機轉子本身生熱率比較大,并且電機整體處于一個封閉的空間,冷卻液對其溫度影響也有限,這樣就形成一種生熱多、散熱困難的情況。前、后軸承的最高溫度都出現在軸承滾珠的中心位置,其中,前軸承組的最高溫度在 62. 5 ℃ 左右,后軸承的最高溫度則為 62 ℃ 左右,由此可知,電主軸的軸承溫升為 37 ℃ 左右。支承軸承溫度較高的原因主要有 2 個: 一是電主軸高速旋轉導致軸承磨損加劇,從而使得軸承發熱量較高; 二是由于電機轉子的發熱量通過接觸件的熱傳導作用影響到軸承的發熱。
另外,可以看到,不論前、后軸承,軸承內圈的平均溫度均要遠高于軸承外圈,大約平均高出 30 ℃ ,這是因為軸承內圈與溫度較高的主軸直接接觸,而軸承外圈則是距離冷卻管路更近,由于熱傳導的作用,產生了該現象。電機定子的發熱率也是比較高,但是它的最高溫度大約只有 39 ℃ ,這里,流過電主軸殼體的冷卻水起到了關鍵作用,帶走了定子產生的大部分熱量。
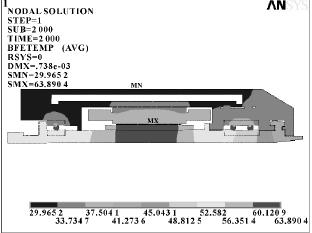
圖 9 電主軸溫度分布
高速電主軸瞬態熱分析用于分析其溫度場隨時間的變化情況。瞬態熱分析與穩態熱分析的區別在于其載荷是隨時間變化的?,F假設電主軸空載運行了1 000 s,對電主軸進行瞬態熱分析。在電主軸前軸承、后軸承、電機轉子上分別選取溫度較高的節點,相應地繪制各節隨時間變化的溫度曲線,如圖 10 所示。
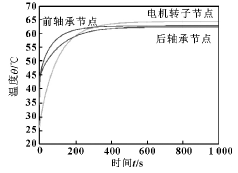
圖 10 電主軸特定節點溫升曲線
由圖 10 可知,在 0 ~ 400 s,不論電機轉子、前軸承和后軸承節點,它們的溫度上升速率在整個溫升過程中都為最大,其中,前軸承升溫速率比后軸承大,而后軸承的溫升速率又比電機轉子大; 在 400 ~800 s 區間,三者的溫度上升趨勢逐漸趨于平緩,并持續保持轉子溫度高于前軸承,前軸承溫度高于后軸承; 從 800 s 左右開始,三者都基本達到穩態溫度,溫度大小排序維持不變?;谝陨犀F象,有如下分析: 電主軸的溫度上升主要經歷了急劇上升、緩慢上升和穩定 3 個階段。在第一階段,由于前軸承為 2 個軸承組成的軸承組,而后軸承為單一的軸承,則后軸承的發熱量明顯低于前軸承,因此出現了前軸承溫升大于后軸承的現象。在第二、第三階段,主要由于冷卻水的持續作用,使得電主軸的溫升逐漸趨于平穩,并最終達到穩定狀態。通過以上分析可見,在該電主軸以60 000 r/min轉速開始工作前,先讓其空轉 800 s左右以達到預熱目的,然后再進行加工操作,從而可以大大降低由于主軸溫升造成的加工誤差。為了分析電主軸的熱位移及熱應力分布情況,需要進行熱 - 結構耦合分析。本文作者采用間接法進行熱 - 結構耦合分析。在前述穩態熱分析的基礎上,進行如下操作:
(1) 在前處理器中轉換熱分析單元 PLANE55 為相對應的結構單元 PLANE182。(2) 設置添加電主軸材料的物理參數。將電主軸各部件材料的彈性模量、線膨脹系數和泊松比進行設置。(3) 將上述穩態熱分析的結果以溫度載荷的形式加載到有限元模型。(4) 指定電主軸的參考溫度為 25 ℃ 。默認在參考溫度時,熱應力為 0。(5) 進行求解及后處理。按照上述步驟操作完畢后,電主軸軸向位移場如圖 11 所示。
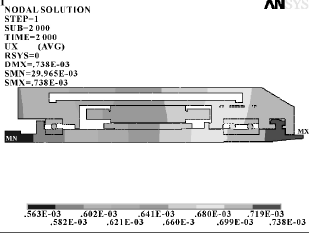
圖 11 電主軸軸向位移場
由圖 11 可知: 在穩態溫度熱載荷作用下,主軸的軸向位移量基本上是從軸的前端向后端逐漸減小,電主軸整體的軸向熱位移最大點出現在主軸的最前端,為 0. 738 mm,熱位移最小點出現在主軸的最末端,為 0. 563 mm,這一情況對電主軸的加工精度的影響是明顯的,由此可見對電主軸適當冷卻散熱的重要性。另外,通過采用彈性模量較大或熱膨脹系數較小的材料作為電主軸材料可以達到減小主軸軸向變形量的目的。圖 12—14 示出了電主軸軸向、徑向和周向的熱應力分布云圖。
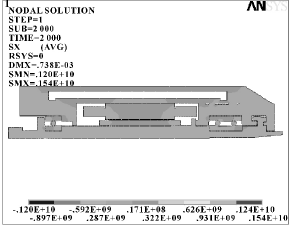
圖 12 電主軸軸向應力場
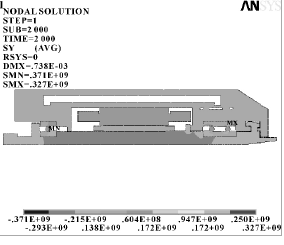
圖 13 電主軸徑向應力場
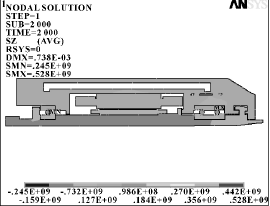
圖 14 電主軸周向應力場
3. 3 實驗
為了驗證理論計算及仿真分析的可行性,設計溫度測定實驗,裝置如圖 15 所示。
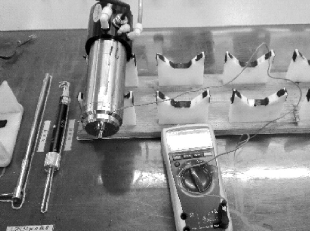
圖 15 實驗裝置
電主軸以 60 000 r/min 轉速空轉 1 h 后,分別選取電主軸外壁、前端及主軸內壁靠近轉子部分若干點,采用萬用表和熱敏電阻測量各點溫度,并與仿真結果中對應各點溫度進行比較,如表 3 所示。測量數據與仿真數值的偏差基本維持在 10% 以內,說明文中的理論方法是可行的。
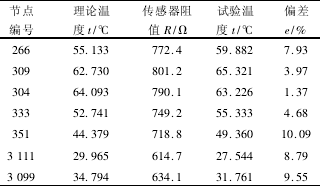
表 3 節點溫度的理論值與實際值
4、 結論
(1) 采用局部熱計算方法計算滾珠軸承生熱功率,分析發現軸承轉速及軸向受力都對軸承生熱具有顯著影響,且 軸 承 滾 珠 自 旋 是 軸 承 的 主 要 的 發 熱形式。(2) 利用有限元分析軟件 ANSYS 對電主軸模型的溫度場、軸向位移場及應力場進行仿真,分析發現電主軸的最高溫度出現在內置電機轉子上且轉軸前端的軸向位移最大,說明電主軸的熱源生熱對其加工精度及穩定性具有決定性的影響。(3) 通過溫升 測定實驗 驗 證了理論方 法的可行性。
投稿箱:
如果您有機床行業、企業相關新聞稿件發表,或進行資訊合作,歡迎聯系本網編輯部, 郵箱:skjcsc@vip.sina.com
如果您有機床行業、企業相關新聞稿件發表,或進行資訊合作,歡迎聯系本網編輯部, 郵箱:skjcsc@vip.sina.com
更多相關信息