基于機器人的鍛鑄件基準制備系統
2017-6-15 來源:北京航空航天大學 作者:何小磊,屈新河,彭偉杰
摘要:針對無基準鍛鑄件毛坯的數控加工化率低和廢品率高的問題,提出了一種以毛坯的數字化模型與CAD模型的配準技術、機器人調姿技術以及低熔點合金澆鑄工藝的基準制備方法。在分析了毛坯件的結構特點及傳統加工工藝要求的基礎上,建立了以點云數據向理論模型進行配準對齊得到旋轉量和移動量,機器人根據該旋轉量和移動量對毛坯件進行調姿,從而使毛坯件處于理論的加工位置,利用低熔點合金將毛坯件和澆鑄盒固定成一個整體,形成以澆鑄盒為毛坯件的加工基準。最后通過實驗論證了此方法的可行性,實現了無基準鍛鑄件毛坯的基準自動化制備。
關鍵詞:基準制備;配準對齊;機器人;調姿;低熔點合金
0.引言
在傳統的機械生產中,通過對毛坯件整體或者局部的加工得出所需要的成品件,若按照傳統的工藝進行加工定位,則會存在加工時間長、可靠性差、鍛鑄件毛坯的數控化率低等問題。對一些無基準的毛坯件由于缺乏加工基準,則更難對零件進行加工;若毛坯件的加工基準不準,則會導致余量加工不均勻甚至不足或超差等問題,嚴重影響零件的加工誤差;隨著鍛鑄件毛坯數量的增加,傳統手工劃線方式越來越不能滿足實際生產加工的要求。因此需要利用數控加工方式代替傳統手工劃線的方式,保證毛坯件的加工部分留有余量而非加工面能夠保證余量均勻。因此,如何保證毛坯件的精確定位是無基準毛坯件數控加工的核心問題。
本文所提出的機器人鍛鑄件基準制備技術結合了鍛鑄件毛坯的點云數據向理論模型進行配準對齊技術、機器人調姿技術以及利用低熔點合金澆鑄工藝,從而準確得出澆鑄后毛坯件在加工坐標系下的位置和姿態。鍛鑄件毛坯傳統的加工方式采用手工劃線方式,各個工序之間加工基準無法統一,導致毛坯件加工的精度較差,漫長才、何世安[1]等針對加工基準統一對加工精度的影響進行了研究。蔡澤、張樹生[2]等提出了利用三維工序的投影視圖與當前工序圖的關聯,通過分析加工基準的類型和特點,提出了加工基準的獲取方法,并且介紹了加工基準的匹配算法。董天毅[3]以輕型汽車SF130傳動箱為例驗證了定位基準的選擇對加工質量的影響。針對不同的零部件基準的選擇也不盡相同,向文俊[4]針對發動機缸體的基準選擇進行了研究。蔣利洋[5]等提出了鍛鑄件毛坯數控加工原點定位技術,利用點云數據向理論模型進行配準對齊,準確計算出點云數據相對于理論模型的偏差量。
本文以某類無基準鍛鑄件的基準制備為研究對象,該類零件的結構特點為沒有加工基準、部分加工面不進行加工但是要保證余量均勻。利用點云數據向理論模型配準技術、機器人調姿技術以及低熔點合金澆鑄工藝組成的基準制備系統,將毛坯件調姿到理論的位置處,并且使調姿后的位置能夠包圍住理論模型,從而確定毛坯在加工坐標系下的位置和姿態,以該加工坐標系形成理論模型的刀具軌跡文件,利用該刀具軌跡文件加工毛坯。
1.鍛鑄件傳統加工缺點
鍛鑄件的傳統加工方式存在以下四個方面的問題:
1)毛坯件進廠之前缺乏科學檢驗手段,不能提前剔除余量不足的毛坯件,導致在后續的加工中零件報廢,并且浪費前期加工工序所消耗的時間。
2)無基準鍛鑄件缺乏定位基準,采用傳統手工劃線的方式確定零件的加工基準,導致準備時間長、可靠性差、不確定因素太多,使最終加工零件的廢品率高。
3)傳統手工劃線方式中間的工序繁多,加工周期長、數控化率底。以某類零件為例,20道加工工序中其中只有3道數控加工工序,并且加工周期為55天。
4)鍛鑄件數量的劇增,鍛鑄件零件越是復雜,采用手工劃線的方式工作量也急劇增加。2 鍛鑄件基準制備系統 基于機器人的鍛鑄件基準制備技術方法總體分為七個步驟,其流程圖如圖1所示。
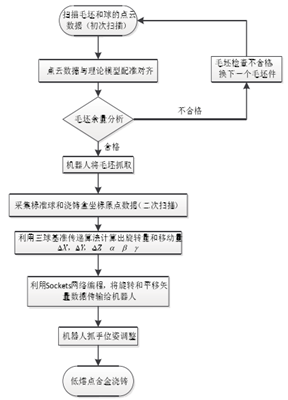
圖1 鍛鑄件基準制備總體方案
1)配準對齊:獲取毛坯件及三個標準球的點云數據,將掃描完整的點云數據向CAD模型進行配準對齊,利用已經開發的各種配準對齊和余量優化分配功能模塊,使得毛坯的點云數據包圍在CAD模型的外表面,此時毛坯的點云數據與CAD模型處于最優的相對位姿;
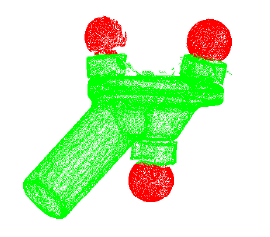
圖2 毛坯和三個標準球的點云數據
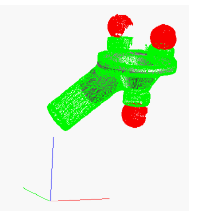
圖3 配準對齊
2)三球基準傳遞:利用激光掃描儀獲取毛坯上三個標準球的點云數據以及澆鑄盒角點的點云數據并且在澆鑄盒的角點上建立測量坐標系。在測量坐標系下,利用三球基準傳遞技術,將機器人端三個標準球依次向圖3中三個標準球的點云數據對齊。
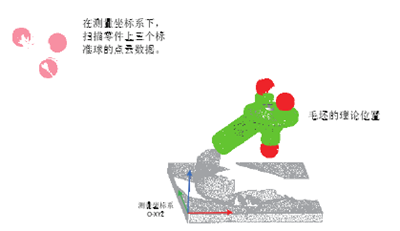
圖4 配準對齊數據和測量坐標系下三球數據
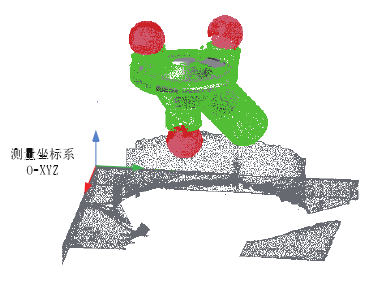
圖5 三球基準傳遞
根據三球基準傳遞技術,計算出在測量坐標系下的移動量和旋轉量 如表1所示。
表1 三球基準傳遞的旋轉量和移動量
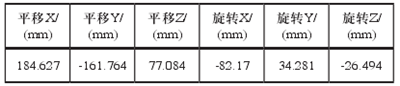
3)初始位姿補償:將 補償到機器人的初始位姿Ts,計算出機器人末端執行器調姿后的位置和姿態Te;
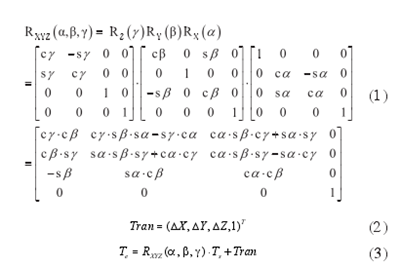
4)通訊控制與機器人調姿:根據Sockets網絡編程原理,利用服務器-客戶端模式,在配準系統中開發計算機與機器人之間的通訊控制程序,利用已經開發的通訊控制程序將Te傳輸到機器人控制柜中,此時機器人將毛坯件放入澆鑄盒中;

圖6 機器人調姿后零件在澆鑄盒中的位置和姿態
5)澆入低熔點合金:機器人調姿完成之后,向澆鑄盒中澆入低熔點合金,待低熔點合金冷卻之后,形成了以澆鑄盒為零件的加工基準。
2 .系統實現的關鍵技術
2.1 毛坯點云數據與
CAD模型配準對齊技術該技術的目的是實現掃描點云與CAD模型的最佳相對位姿,對于鍛鑄件毛坯,配準對齊的目的是追求加工余量均勻分配,那么最佳擬合對齊算法是個較為理想的選擇,最佳擬合對齊首先計算掃描點在曲面模型表面的匹配點,然后運用ICP迭代算法[6],最小化匹配點對的距離偏差,以實現最佳擬合對齊的目的。
2.1.1 最佳擬合對齊具體的實施流程
1)對配準的點云數據P1進行精簡,減少參與配準的點云數量,利用精簡后的點云數據P形成最大包圍盒Box1,剔除不在包圍盒中的點集,目的是為了提高配準的效率;
2)求取曲面模型中各張曲面的面積,并且根據面積的大小進行排序,按照采樣的比例提取面積較大的曲面集F2參與配準,在保證CAD曲面模型整體外形信息較為完整的基礎上,減少參與配準的曲面個數,提高了配準的效率;
3)點云P和曲面集合F2進行ICP迭代配準算法,實現參與配準數據的最佳擬合對齊,進而輸出最終對齊的變換矩陣M,最后用M對整體的掃描點云P1進行姿態調整,實現掃描點云與CAD曲面模型的最佳擬合對齊。
2.1.2 ICP配準算法原理分析
原始ICP算法的基本描述是在另一個點云Q中求取與點云P的最近點(理想狀態下本應重合的點),計算相應點的歐式距離平方的平均值,然后通過迭代算法,最小化平均值,這樣不斷更新點云片間的相對位置,達到點云片之間配準對齊的效果,如圖7所示。
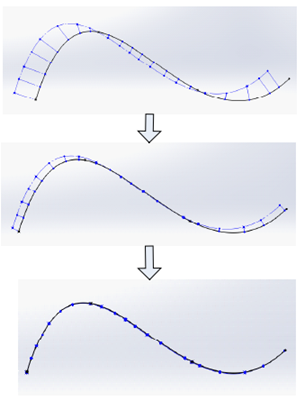
圖7 ICP配準過程示意圖
本章中提到的掃描點云與CAD模型最佳擬合對齊是利用奇異值分解法、四元組法找出掃描點云與模型表面對應點的變換矩陣,多次迭代直至目標函數滿足一定的精度為止。其目標函數為:
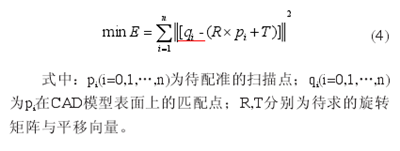
2.2 三球基準傳遞技術
本文提到的三球定位基準傳遞方法基本實施的思路如下:先后兩次在不同的坐標系下獲取三個標準球的球心坐標,使三對球心依次重合,反求出旋轉平移矩陣,并將該變換作用于毛坯掃描點云,使得毛坯掃描點云從初始的坐標系下變換到了指定的坐標系下。在初始坐標系F0下,毛坯掃描點云集合為Dscan,三個標準球的球心坐標分別為P1、P2、P3;將毛坯件固定在機器人的末端執行器上,在測量坐標系Fm(通常將此時的測量坐標系設置為加工坐標系)下再次獲取三個標準球的球心坐標Q1、Q2、Q3,通過使P1、P2、P3與Q1、Q2、Q3分別重合,反求出旋轉矩陣R和平移向量T。
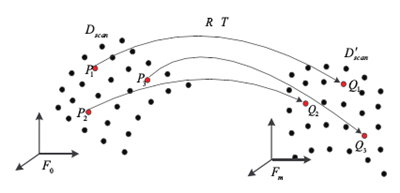
圖8 三球基準傳遞示意圖
1)以坐標系P1、P2、P3為基礎數據,建立以P1作為坐標原點的標架的三個坐標軸。以坐標點Q1、Q2、Q3為基礎數據,建立以Q1作為坐標原點的標架的三個坐標軸。
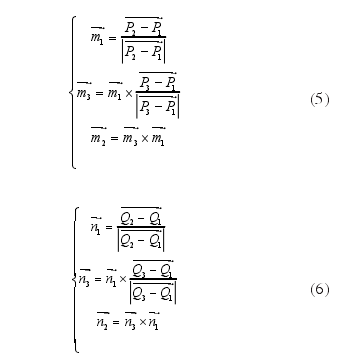
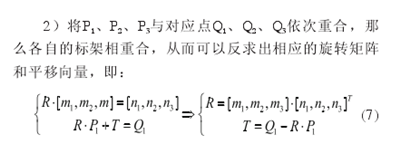
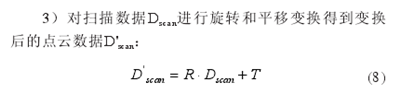
3 .實例驗證
針對某類鍛鑄件毛坯,利用鍛鑄件基準制備系統,結合點云數據向理論模型的配準技術、機器人調姿技術以及低熔點合金澆鑄工藝,確定該類鍛鑄件與澆鑄盒的相對位置,形成以澆鑄盒的外表面為毛坯件的加工基準,利用數控機床加工該類毛坯件。
首先利用激光掃描儀獲取毛坯件和三個標準球完整的點云數據。如圖9(b)所示,機器人將毛坯件調整到空間中的任意一個位置和姿態,利用激光掃描儀獲取此時零件上三個標準球的點云數據以及澆鑄盒角點的點云數據。利用三球基準傳遞技術計算出旋轉量和移動量
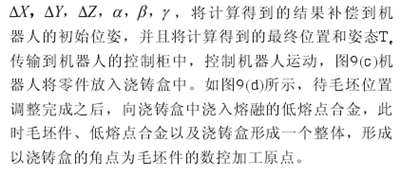
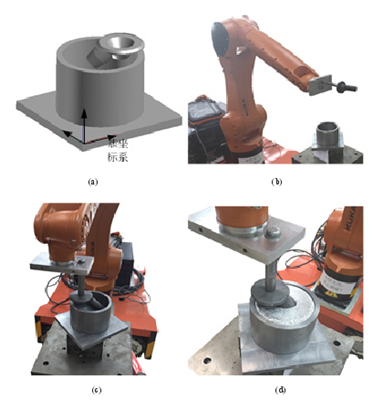
圖9 機器人調姿過程
4.結論
針對無基準鍛鑄件毛坯缺少加工基準問題,本文采用機器人抓取毛坯件進行調姿使最終調整的位置能夠均勻的包圍住原先設定理論模型的外表面,利用理論模型生成的刀具軌跡文件加工調姿后的毛坯件,是本文研究的核心內容。最后利用激光掃描儀再次獲取調姿后毛坯件的點云數據,并且與理論位置進行對比得出最終的位置和姿態滿足精度要求,因此通過實例驗證了本文無基準鍛鑄件基準制備加工方案的可行性。
投稿箱:
如果您有機床行業、企業相關新聞稿件發表,或進行資訊合作,歡迎聯系本網編輯部, 郵箱:skjcsc@vip.sina.com
如果您有機床行業、企業相關新聞稿件發表,或進行資訊合作,歡迎聯系本網編輯部, 郵箱:skjcsc@vip.sina.com
更多相關信息